How Lean Methodology Drives Continuous Improvement in Organizations
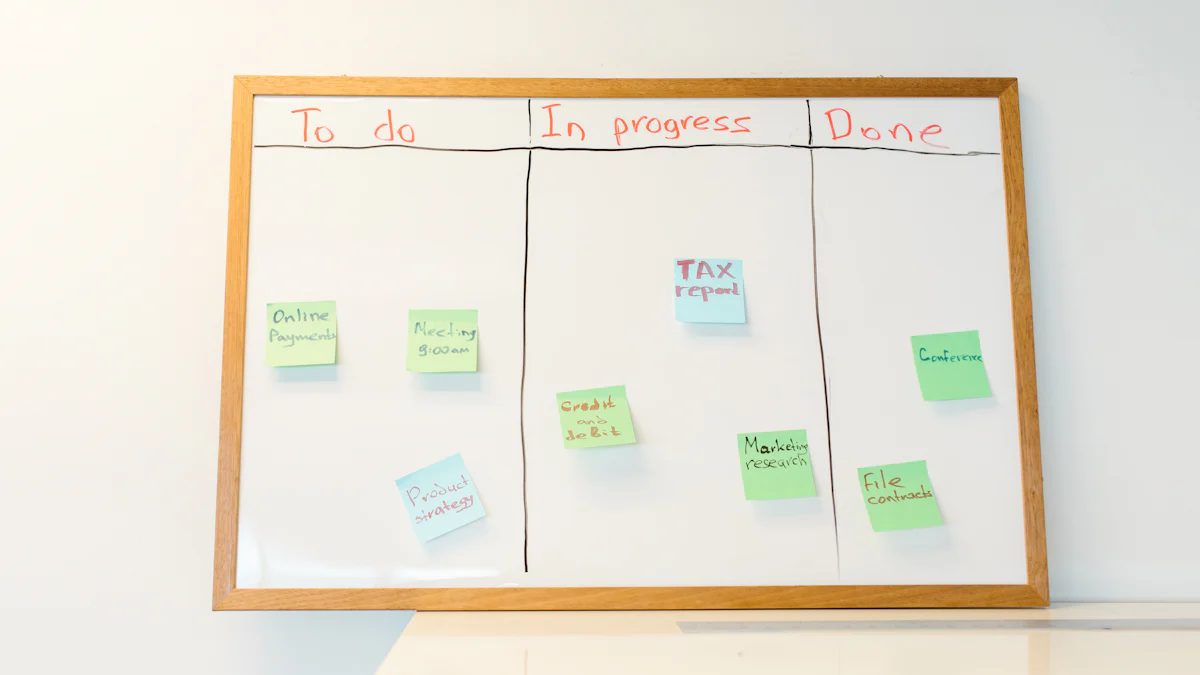
Lean methodology transforms how organizations operate by focusing on eliminating waste and optimizing processes. It prioritizes creating value for customers while ensuring resources are used efficiently. Teams adopting Lean systems often experience significant improvements in productivity and innovation.
Lean companies report savings of up to 30% on development expenses.
Output increases range between 20% to 40%.
Earlier value delivery and faster testing of ideas become achievable.
Unlike rigid systems, Lean methodology promotes adaptability. It enables teams to adjust processes seamlessly, ensuring resilience in dynamic markets. This flexibility empowers organizations to meet clients' needs effectively while fostering a culture of continuous improvement.
Key Takeaways
Lean methods aim to cut waste and improve processes for customers.
Companies can lower costs by 30% using Lean ideas.
Small changes, called Kaizen, bring big improvements over time.
Tools like Value Stream Mapping show problems and fix workflows.
Involving all workers builds responsibility and sparks new ideas in Lean.
Pull systems match production to customer needs, avoiding extra products.
Checking performance often helps improve Lean plans for long-term success.
A culture of improvement helps teams grow and succeed in changing markets.
Understanding Lean Methodology
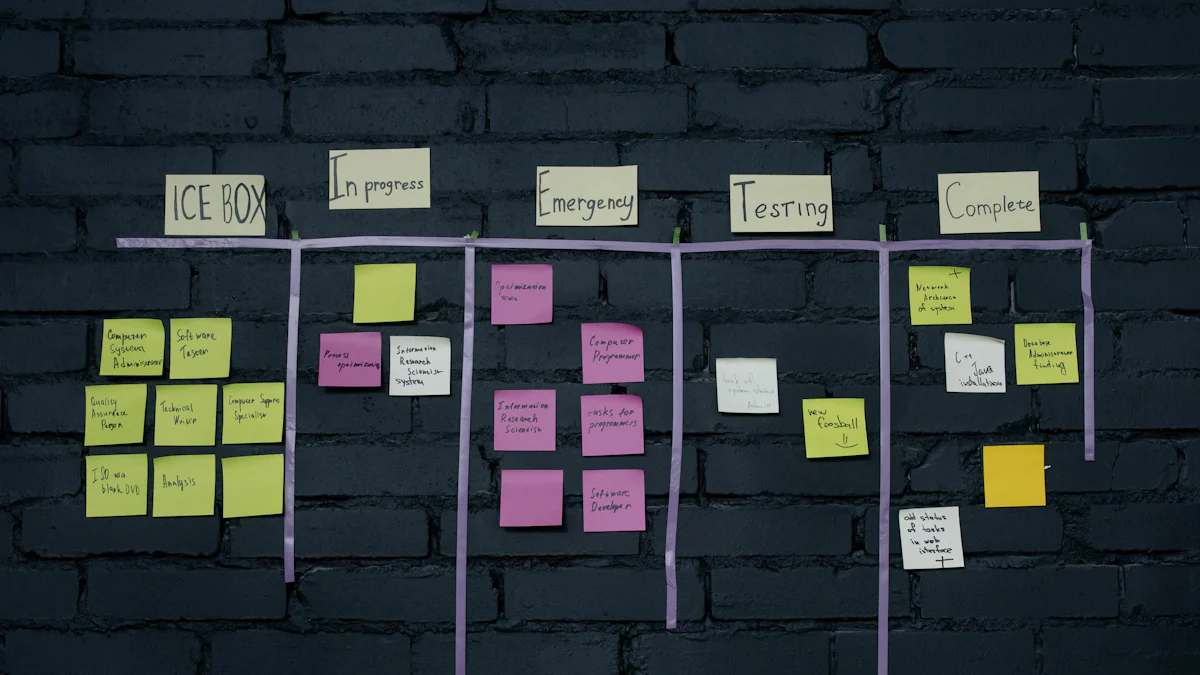
What Is Lean Methodology?
Lean Methodology is a systematic approach designed to enhance efficiency by eliminating waste and focusing on value creation. It prioritizes delivering products or services that meet customer needs while minimizing unnecessary processes. This methodology originated in manufacturing but has since expanded to industries like healthcare, software development, and finance. Its adaptability makes it a valuable tool for organizations seeking continuous improvement.
The methodology emphasizes five key components that differentiate it from other approaches:
Identify value by understanding customer needs.
Map the value stream to visualize and eliminate waste.
Create a flow to ensure smooth progress of work.
Establish pull systems to produce based on customer demand.
Seek perfection through ongoing process improvements.
These principles enable teams to streamline operations, reduce costs, and deliver higher-quality outcomes.
Core Principles of Lean Methodology
Defining Value and Mapping the Value Stream
Defining value begins with understanding what customers truly need. Organizations must identify which products or services provide the most benefit. Once value is defined, mapping the value stream becomes essential. This process involves visualizing every step in the workflow to pinpoint inefficiencies and eliminate waste. Tools like value stream mapping help teams optimize the flow of value from start to finish.
Creating Flow and Using Pull Systems
Creating flow ensures that work progresses smoothly without interruptions. Teams focus on removing bottlenecks and aligning processes to maintain consistency. Pull systems further enhance efficiency by producing only what customers demand. This approach minimizes overproduction and reduces inventory costs, allowing organizations to respond quickly to market changes.
Pursuing Perfection Through Continuous Improvement
Continuous improvement lies at the heart of Lean Methodology. Teams regularly evaluate their processes to identify areas for enhancement. By fostering a culture of innovation, organizations can adapt to evolving customer needs and industry trends. This pursuit of perfection drives long-term success and sustainability.
The Evolution of Lean Methodology
Lean Methodology has evolved significantly since its inception. In the early 20th century, the Ford Motor Company revolutionized manufacturing with assembly line techniques. Decades later, Japanese companies like Toyota refined these practices, introducing concepts such as kaizen and Just-in-Time production. The term "Lean" was officially coined in 1991, formalizing its principles in works like The Machine That Changed the World.
Over time, Lean principles have been adopted across various industries. For example:
In the 1980s and 1990s, Western manufacturers embraced Japanese practices to improve efficiency.
Bank of America applied Lean principles to enhance customer satisfaction and streamline operations.
General Electric utilized Lean management to address challenges and drive innovation.
These examples highlight the adaptability of Lean Methodology and its impact on diverse sectors.
Benefits of Lean Methodology
Enhancing Efficiency and Reducing Waste
Lean Methodology enables organizations to streamline operations by identifying and eliminating inefficiencies. Teams use tools like Value Stream Mapping to visualize workflows and pinpoint wasteful steps. This approach helps reduce bottlenecks, ensuring smoother task distribution and proactive problem-solving. For example, Just-in-Time (JIT) production aligns manufacturing with demand, minimizing excess inventory and lowering operational costs.
By organizing processes visually, teams can enhance efficiency and adapt to changing demands. Continuous Improvement, or Kaizen, plays a crucial role in this process. It encourages incremental enhancements involving all employees, fostering accountability and collaboration. These practices not only reduce waste but also improve overall productivity. Organizations that adopt Lean systems often experience stronger customer relationships and better stakeholder visibility by focusing on delivering value.
Improving Customer Satisfaction
Lean Methodology prioritizes understanding customer needs to deliver value effectively. Teams define value from the customer’s perspective and align their processes to meet these expectations. This customer-centric approach ensures that products and services address specific requirements, enhancing satisfaction levels.
Pull systems, a core principle of Lean, allow organizations to produce goods based on actual demand. This minimizes overproduction and ensures timely delivery, which directly benefits customers. Additionally, the adaptability of Lean systems enables teams to respond quickly to market changes or unexpected challenges. By focusing on quality and efficiency, organizations can build trust and loyalty among their clients.
Fostering a Culture of Continuous Improvement
Continuous improvement is a cornerstone of Lean Methodology. It emphasizes ongoing refinement of processes, fostering a mindset of iterative enhancements. Teams regularly evaluate workflows to identify inefficiencies and implement solutions. This approach promotes collaboration and information sharing across departments, creating a unified effort toward improvement.
Leaders and stakeholders play a vital role by providing regular feedback, which helps teams refine their skills and processes. Employees are empowered to take ownership of their work, contributing to a culture of accountability and innovation. Over time, this mindset leads to sustained progress and higher-quality outcomes. Organizations that embrace continuous improvement often see enhanced productivity and adaptability, ensuring long-term success.
Boosting Employee Engagement and Collaboration
Lean Methodology strengthens employee engagement by empowering individuals to take ownership of their work. Teams gain a sense of purpose when they actively contribute to process improvements. This approach fosters accountability and motivates employees to perform at their best. Organizations that implement Lean principles often see higher morale and stronger commitment from their workforce.
Collaboration thrives in Lean environments. Teams work together to identify inefficiencies and develop solutions. Cross-functional collaboration becomes a key driver of success, as employees from different departments share insights and expertise. This collective effort ensures that processes are optimized from multiple perspectives, leading to more effective outcomes.
Tip: Encouraging open communication among team members can significantly enhance collaboration and problem-solving.
Lean systems also promote transparency. Tools like visual management boards and daily stand-up meetings keep everyone informed about progress and challenges. Employees stay aligned with organizational goals, which reduces misunderstandings and fosters a sense of unity. When teams have a clear understanding of their roles and responsibilities, they can work more efficiently and effectively.
A culture of continuous improvement further boosts engagement. Employees are encouraged to share ideas and participate in decision-making processes. This inclusivity makes them feel valued and respected, which enhances job satisfaction. Leaders play a crucial role by recognizing contributions and providing constructive feedback. Recognition not only motivates individuals but also reinforces a positive work environment.
Lean practices also reduce workplace stress. By eliminating waste and streamlining workflows, employees face fewer bottlenecks and delays. This creates a smoother work experience, allowing teams to focus on delivering value rather than managing unnecessary tasks. A less stressful environment leads to better mental well-being and higher productivity.
Organizations that prioritize employee engagement and collaboration often achieve remarkable results. Teams become more innovative and adaptable, which drives continuous improvement. Clients benefit from these improvements through higher-quality products and services. To learn more about how Lean Methodology can transform your organization, reach out to us today.
Note: Engaged employees are the backbone of successful Lean systems. Investing in their growth and collaboration ensures long-term organizational success.
How Lean Methodology Drives Continuous Improvement
The Role of Kaizen in Continuous Improvement
Kaizen, a Japanese term meaning "change for the better," plays a vital role in driving continuous improvement within Lean Methodology. It focuses on small, incremental changes that collectively lead to significant advancements. Unlike top-down or radical transformations, Kaizen emphasizes collaboration and commitment across all levels of an organization.
Teams identify issues and opportunities for improvement.
They develop and implement solutions to address these challenges.
This process repeats continuously, fostering a cycle of ongoing progress.
Kaizen is a cornerstone of Lean systems, particularly in manufacturing environments like the Toyota Production System. It helps reduce defects, eliminate waste, and boost productivity. Employees are encouraged to take ownership of their work, promoting accountability and innovation. By involving everyone in the improvement process, organizations create a culture where progress becomes a shared responsibility.
Identifying and Eliminating Waste
Waste elimination is central to Lean Methodology. Organizations must first identify inefficiencies to streamline processes effectively. Tools like value stream mapping allow teams to visualize workflows, highlighting both value-added and non-value-added activities. This visualization helps pinpoint areas where resources are wasted.
Other strategies include Pareto analysis, which prioritizes significant problems using the 80/20 rule, and the 5S system, which organizes workplaces to reduce clutter and improve efficiency. Kanban boards visually manage workflows, reducing overproduction and inventory. Poka-yoke, or mistake-proofing, prevents defects by addressing errors at their source. These tools empower teams to optimize operations and focus on delivering value to customers.
The Seven Types of Waste
Lean Methodology identifies seven primary types of waste that hinder efficiency:
Overproduction: Producing more than what is needed.
Waiting: Delays caused by idle time or bottlenecks.
Transportation: Unnecessary movement of materials or products.
Inventory: Excess stock that ties up resources.
Motion: Inefficient movements by employees or equipment.
Over-processing: Performing more work than required.
Defects: Errors that result in rework or discarded products.
By addressing these wastes, organizations can enhance productivity and reduce costs. Teams that adopt Lean systems often experience smoother workflows and improved customer satisfaction. Continuous improvement ensures that waste elimination remains an ongoing priority.
Building Feedback Loops for Sustained Progress
Feedback loops play a critical role in sustaining progress within organizations. They provide teams with actionable insights, enabling them to refine processes and achieve better outcomes. By integrating feedback loops into their operations, organizations can maintain a cycle of learning and improvement.
Effective feedback loops rely on timely and accurate information. Teams must collect data from various sources, such as customer feedback, performance metrics, and employee observations. This data helps identify areas where processes fall short or where opportunities for growth exist. For example, a manufacturing team might use defect rates to pinpoint inefficiencies in production workflows.
Once data is gathered, teams analyze it to uncover patterns and trends. This analysis allows them to prioritize issues and develop targeted solutions. Visual tools like dashboards and charts can simplify complex data, making it easier for teams to understand and act upon. Regular review meetings ensure that feedback is not only collected but also used to drive meaningful changes.
Feedback loops also foster collaboration across departments. When teams share insights and solutions, they create a unified approach to problem-solving. Cross-functional collaboration ensures that improvements benefit the organization as a whole rather than isolated areas. For instance, a software development team might work with customer support to address recurring user complaints, leading to a more user-friendly product.
Technology enhances the effectiveness of feedback loops. Digital tools like project management software and real-time analytics platforms streamline data collection and communication. These tools enable teams to respond quickly to challenges, ensuring that feedback leads to actionable results. Automation can further reduce delays, allowing organizations to adapt to changes more efficiently.
Lean Methodology emphasizes the importance of feedback loops in achieving continuous improvement. By embedding these loops into their systems, organizations can create a culture of adaptability and innovation. Teams that regularly evaluate their performance and implement changes remain competitive in dynamic markets. Feedback loops ensure that progress is not a one-time event but an ongoing journey.
Organizations seeking to implement effective feedback loops should focus on clear communication, data-driven decision-making, and cross-functional collaboration. To learn more about how feedback loops can transform your processes, reach out to us today.
Implementing Lean Methodology in Your Organization
Assessing Current Processes
Organizations must begin their Lean journey by thoroughly evaluating their existing processes. This step involves identifying inefficiencies, bottlenecks, and areas where resources are underutilized. Teams should collect data on workflows, employee activities, and customer interactions to gain a comprehensive understanding of current operations. Tools like process flowcharts and Gemba Walks—where leaders observe work directly on the floor—can provide valuable insights into how tasks are performed.
A detailed assessment helps uncover wasteful practices that hinder productivity. For example, excessive waiting times or redundant approvals may slow down operations. By documenting these inefficiencies, teams can prioritize areas for improvement. Engaging employees during this phase is crucial, as their firsthand knowledge of daily tasks often reveals hidden challenges. This collaborative approach ensures that the assessment captures a complete picture of the organization's processes.
Defining Value from the Customer’s Perspective
Defining value is a cornerstone of Lean Methodology. Organizations must understand what customers perceive as valuable to align their processes accordingly. Value is not limited to price; it encompasses factors like quality, convenience, and reliability. Teams can use tools such as the Voice of the Customer (VOC) to gather insights directly from clients. VOC involves collecting feedback through surveys, interviews, and focus groups to identify customer needs and expectations.
Value Stream Mapping (VSM) is another essential technique for defining value. It allows teams to visualize the flow of value from the customer's perspective, highlighting inefficiencies and opportunities for improvement. To effectively define value, organizations should:
Implement VSM to identify customer requirements and eliminate inefficiencies.
Foster cross-functional collaboration to align objectives and improve data collection.
Establish a customer-centric culture to enhance understanding of customer value.
By focusing on these strategies, teams can ensure that their processes deliver maximum benefit to customers while minimizing waste.
Mapping and Optimizing the Value Stream
Mapping the value stream is a critical step in Lean Methodology. This process involves diagramming every step in the material and information flows required to deliver a product or service. Teams start by creating a current state map, which captures the existing condition of the value stream. This map helps identify waste, such as overproduction or unnecessary transportation, that disrupts efficiency.
Once the current state is documented, teams develop a future state map. This visualization outlines how materials and information should flow to optimize the value stream. For example, a manufacturing team might redesign workflows to reduce waiting times or eliminate redundant steps. Value Stream Mapping exposes inefficiencies and provides a clear roadmap for improvement, making it a fundamental tool for continuous progress.
Organizations across industries can benefit from this approach. Whether in healthcare, software development, or manufacturing, mapping and optimizing the value stream ensures that resources are used effectively. Teams that adopt this practice often experience smoother workflows, reduced costs, and enhanced customer satisfaction.
Tip: Regularly revisiting and updating the value stream map ensures that processes remain aligned with evolving customer needs and market conditions.
Establishing Flow and Pull Systems
Establishing flow and pull systems is essential for optimizing processes in Lean Methodology. Flow ensures that work progresses smoothly without interruptions, while pull systems align production with actual demand. Together, they create a streamlined workflow that minimizes waste and enhances efficiency.
To establish flow, teams must focus on breaking down complex processes into manageable steps. Simplifying workflows reduces delays and ensures consistency. Reconfiguring production steps can further optimize efficiency by eliminating unnecessary actions. Balancing workloads across teams prevents bottlenecks and ensures that resources are utilized effectively. Encouraging collaboration through cross-functional departments improves communication and fosters innovation. Training employees to develop multi-skilled capabilities enhances flexibility, allowing teams to adapt to changing demands.
Pull systems operate on the principle of producing only what is needed when it is needed. This approach minimizes overproduction and reduces excess inventory. Teams can implement pull systems by mapping the value stream, visualizing workflows with tools like kanban boards, and defining clear work-in-progress (WIP) limits. Establishing kanban policies ensures that work progresses systematically, while regular reviews help identify and eliminate inefficiencies.
Description | |
---|---|
Break down steps | Simplifying complex processes into manageable steps to enhance flow. |
Reconfigure production steps | Adjusting the sequence of operations to optimize efficiency and reduce waste. |
Level workload | Balancing the workload across different teams to prevent bottlenecks. |
Create cross-functional departments | Encouraging collaboration among different functions to improve communication and efficiency. |
Train employees | Developing multi-skilled employees to enhance flexibility and adaptability in the workflow. |
Establish Pull | Implementing a system where production is based on actual demand, minimizing excess inventory. |
By integrating these practices, organizations can achieve a seamless flow of work and respond quickly to customer needs. Teams that adopt flow and pull systems often experience reduced lead times, improved quality, and greater customer satisfaction.
Creating a Culture of Continuous Improvement
A culture of continuous improvement drives long-term success in Lean Methodology. This culture encourages teams to regularly evaluate their processes and seek opportunities for enhancement. It fosters a mindset where every employee contributes to incremental improvements, ensuring sustained progress.
Organizations can build this culture by promoting open communication and collaboration. Leaders should empower employees to share ideas and take ownership of their work. Recognizing contributions and providing constructive feedback motivates teams to strive for excellence. Cross-functional collaboration further strengthens this culture by enabling diverse perspectives to address challenges effectively.
Regular training and development programs help employees acquire new skills and adapt to evolving demands. Teams should also use tools like value stream mapping and feedback loops to identify inefficiencies and implement solutions. By embedding continuous improvement into daily operations, organizations can enhance productivity, reduce waste, and maintain a competitive edge.
Measuring and Refining Strategies
Measuring the success of Lean strategies is crucial for achieving continuous improvement. Metrics provide valuable insights into performance and highlight areas for refinement. Organizations should track key indicators such as safety, cost, product quality, and customer satisfaction to evaluate their progress.
Safety metrics monitor workplace incidents and ensure compliance with best practices. Cost metrics help teams control expenses while maintaining quality. Product quality indicators focus on defects and compliance rates, ensuring reliability. Customer satisfaction surveys assess how well processes meet client expectations. Metrics like cycle time and throughput measure efficiency and productivity, while work-in-progress (WIP) limits prevent overload.
Metric | Purpose |
---|---|
Safety | Tracks workplace incidents and ensures safe practices. |
Cost | Monitors expenses to maintain cost-effectiveness. |
Product Quality | Measures defects and compliance rates to ensure reliability. |
Customer Satisfaction | Assesses feedback and loyalty to gauge client satisfaction. |
Cycle Time | Reflects delivery efficiency by measuring task completion time. |
Throughput | Tracks the number of tasks completed in a specific timeframe. |
Work in Progress (WIP) | Limits tasks being worked on simultaneously to prevent overload. |
Teams should analyze these metrics regularly to identify trends and prioritize improvements. Refining strategies based on data-driven insights ensures that Lean initiatives remain effective and aligned with organizational goals. By continuously measuring and refining their approaches, organizations can sustain progress and achieve long-term success.
Real-World Applications of Lean Methodology
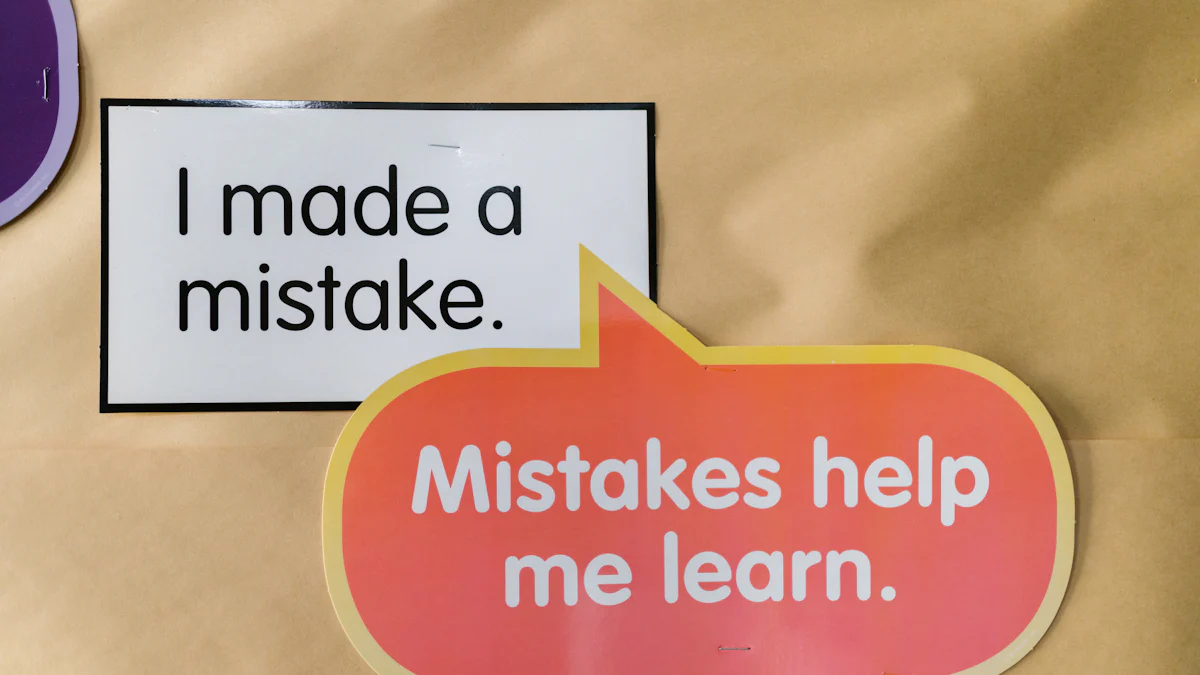
Lean in Manufacturing
Lean methodology has revolutionized manufacturing by enhancing efficiency and reducing waste. Companies in this sector have adopted Lean principles to streamline operations and improve product quality. Several notable examples demonstrate its impact:
Toyota: The Toyota Production System (TPS) emphasizes continuous improvement and employee engagement. This approach generates over 2 million suggestions annually, with a 90% implementation rate.
Starbucks: By applying Kaizen and Lean techniques, Starbucks improved its operations and customer service, leading to better financial performance and higher customer satisfaction.
Motorola: The company used Six Sigma, a Lean tool, to address quality issues in semiconductor production. This initiative reduced defects and increased profitability.
Ford: Lean principles like Kaizen and Total Quality Management helped Ford enhance assembly line efficiency, resulting in better product quality and lower costs.
These examples highlight how Lean methodology fosters innovation and adaptability in manufacturing. By focusing on waste elimination and continuous improvement, organizations can achieve significant cost savings and deliver higher-quality products to customers.
Lean in Healthcare
Healthcare organizations face unique challenges, including rising costs and the need for improved patient outcomes. Lean methodology addresses these issues by enhancing quality and value while reducing waste. Key principles such as continuous improvement and respect for people play a vital role in transforming healthcare systems.
Lean practices have been adapted to improve patient safety, reduce medical errors, and enhance satisfaction. For example, hospitals use value stream mapping to identify inefficiencies in patient care processes. This tool helps teams streamline workflows, ensuring timely treatment and better resource allocation. Additionally, Lean principles encourage collaboration among healthcare professionals, fostering a culture of accountability and innovation.
By eliminating waste and focusing on value creation, healthcare organizations can deliver better care at lower costs. Patients benefit from safer environments and more efficient services, while teams experience improved morale and engagement. Lean methodology continues to drive progress in this critical sector.
Lean in Software Development
Software development teams have embraced Lean methodology to optimize workflows and deliver high-value products. This approach aligns with the industry's need for adaptability and customer-centric solutions. However, applying Lean principles in software development presents unique challenges and benefits.
Benefits of Lean Methodology | |
---|---|
Specialized hiring requirements | Cost savings |
Delayed decision-making | High-value product delivery |
Risk of over-simplification | Enhanced efficiency |
Limited resources | Customer-centric approach |
Organizational change | Fostered collaboration |
| Difficulty in measuring progress and ROI | Continuous improvement | | | Optimal resource utilization | | | Improved employee morale |
Teams use Lean tools like Kanban boards to visualize workflows and manage tasks effectively. These tools help reduce bottlenecks and ensure timely delivery. Continuous feedback loops allow developers to refine their processes, addressing customer needs more efficiently. By fostering collaboration and innovation, Lean methodology enables software teams to adapt to changing demands and deliver superior results.
Lean principles empower software development teams to achieve sustainable growth. Organizations that adopt these practices often experience improved efficiency, higher-quality products, and stronger customer relationships.
Key Takeaways from Successful Implementations
Organizations that have embraced Lean methodology demonstrate its transformative potential. Their experiences highlight essential lessons for teams aiming to achieve continuous improvement. These takeaways provide a roadmap for success and inspire others to adopt Lean principles effectively.
1. Start with a Clear Understanding of Value
Successful implementations emphasize the importance of defining value from the customer’s perspective. Teams that focus on delivering what customers truly need can align their processes to maximize impact. For example, organizations that use tools like Value Stream Mapping often identify inefficiencies that hinder value delivery. This clarity ensures that every action contributes to customer satisfaction.
Tip: Regularly revisit customer feedback to refine your understanding of value and adapt to changing expectations.
2. Engage Employees at All Levels
Lean systems thrive when employees actively participate in the improvement process. Teams that involve workers in identifying waste and proposing solutions often achieve better results. Empowering employees fosters accountability and innovation. For instance, companies like Toyota encourage team members to suggest improvements, creating a culture of shared responsibility.
Note: Recognizing employee contributions boosts morale and strengthens commitment to Lean practices.
3. Focus on Small, Incremental Changes
Kaizen, or continuous improvement, teaches that small changes lead to significant progress over time. Teams that prioritize incremental enhancements avoid the risks associated with large-scale overhauls. This approach allows organizations to adapt gradually while maintaining stability. Many successful Lean adopters credit Kaizen for their sustained growth and adaptability.
4. Leverage Visual Tools for Clarity
Visual tools like Kanban boards and dashboards simplify complex workflows. Teams that use these tools can track progress, identify bottlenecks, and maintain transparency. For example, manufacturing teams often rely on visual management to monitor production and reduce delays. These tools enhance communication and ensure alignment across departments.
Tool | Purpose |
---|---|
Kanban Boards | Visualize workflows and manage tasks. |
Value Stream Maps | Identify inefficiencies in processes. |
Dashboards | Track performance metrics. |
5. Commit to Continuous Learning
Organizations that succeed with Lean methodology view challenges as opportunities to learn. Teams that analyze failures and adapt their strategies often achieve long-term success. This mindset ensures resilience in dynamic markets. Leaders play a crucial role by fostering a culture of learning and encouraging experimentation.
Callout: Teams that embrace learning remain competitive and innovative, even in rapidly changing industries.
6. Measure Progress and Refine Strategies
Tracking key performance indicators (KPIs) helps teams evaluate the effectiveness of their Lean initiatives. Metrics like cycle time, defect rates, and customer satisfaction provide actionable insights. Organizations that regularly review these metrics can refine their strategies and sustain progress.
Example: A software development team might use defect rates to identify coding inefficiencies and improve product quality.
These takeaways illustrate the power of Lean methodology to transform systems and teams. By focusing on value, engaging employees, and committing to continuous improvement, organizations can achieve remarkable results. To learn how Lean principles can benefit your team, reach out to us today.
Addressing Challenges in Lean Methodology Adoption
Overcoming Barriers to Implementation
Organizations often face several challenges when adopting Lean Methodology. These barriers can hinder progress and reduce the effectiveness of improvement initiatives. Addressing these obstacles requires a proactive approach and a clear understanding of common issues.
Resistance to Change: Employees may feel uncertain about new processes, fearing disruptions to their routines.
Lack of Leadership Support: Without strong backing from top management, Lean initiatives may lose momentum.
Inadequate Training and Resources: Teams without proper training or tools may struggle to implement Lean practices effectively.
Difficulty in Data Collection and Analysis: Gathering and interpreting data can be complex, especially in organizations with limited analytical capabilities.
Lack of a Continuous Improvement Culture: A stagnant organizational culture can prevent teams from embracing ongoing enhancements.
To overcome these barriers, organizations should focus on clear communication and employee engagement. Leaders must explain the benefits of Lean practices and involve teams in the decision-making process. Providing adequate training ensures that employees feel confident in their roles. Additionally, investing in tools for data collection and analysis can simplify workflows and improve decision-making. Building a culture that values continuous improvement fosters long-term success.
Gaining Organizational Buy-In
Securing stakeholder support is essential for the successful adoption of Lean Methodology. Teams must engage stakeholders early in the process to align goals and expectations. Several strategies can help organizations gain buy-in:
Conduct stakeholder mapping to identify key individuals and their roles.
Understand stakeholder motivations to highlight how Lean practices benefit them.
Set clear timelines for engagement and feedback collection.
Build a compelling business case that demonstrates the value of Lean initiatives.
Gather feedback to refine project goals and address concerns.
Maintain open communication to ensure ongoing support.
By addressing stakeholder concerns and emphasizing the benefits of Lean practices, organizations can create a unified vision. For example, demonstrating how Lean systems improve efficiency and reduce costs can resonate with decision-makers. Engaging stakeholders throughout the process ensures that their expectations are met, fostering trust and collaboration.
Sustaining Lean Practices Over Time
Sustaining Lean practices requires a long-term commitment to continuous improvement. Organizations must integrate Lean principles into their culture to ensure lasting success. Key factors that contribute to sustainability include:
Cultural Alignment: Aligning organizational values with Lean principles helps overcome resistance and ensures widespread adoption.
Effective Leadership Development: Strong leaders inspire teams and drive the adoption of Lean practices. Leadership training programs can empower managers to champion continuous improvement.
Robust Review Processes: Regular reviews maintain accountability and momentum. Teams should evaluate their progress and refine strategies based on performance metrics.
Embedding Lean practices into daily operations ensures that they become a natural part of the organization’s workflow. Leaders play a critical role in reinforcing these practices by recognizing achievements and encouraging innovation. Establishing review processes helps teams stay focused on their goals, ensuring that Lean principles remain effective over time.
Organizations that prioritize cultural alignment, leadership development, and accountability can sustain Lean practices successfully. Teams that embrace these strategies often experience ongoing improvements in efficiency, quality, and customer satisfaction.
Lean methodology transforms organizations by focusing on value creation and waste elimination. Its principles encourage continuous improvement, enabling teams to refine processes and deliver higher-quality outcomes. By fostering a culture of adaptability, Lean empowers employees to innovate and respond to market changes effectively. Teams benefit from tools that streamline workflows, reduce inefficiencies, and align products with customer needs. These practices not only enhance productivity but also build resilience in dynamic environments. Organizations that embrace Lean methodology achieve long-term success by prioritizing efficiency, collaboration, and customer satisfaction.
Note: Teams that adopt Lean systems can unlock their full potential. To explore how Lean can transform your organization, contact us today.
FAQ
What industries can benefit from Lean Methodology?
Lean Methodology applies to various industries, including manufacturing, healthcare, software development, and finance. Its principles of waste elimination and continuous improvement make it adaptable to any sector seeking efficiency and value creation.
How does Lean Methodology improve customer satisfaction?
Lean focuses on understanding customer needs and aligning processes to deliver value. By reducing waste and ensuring timely delivery, organizations can meet customer expectations, enhance quality, and build trust.
What tools are commonly used in Lean Methodology?
Teams often use tools like Value Stream Mapping, Kanban boards, and the 5S system. These tools help visualize workflows, identify inefficiencies, and streamline operations for better outcomes.
How does Lean Methodology foster employee engagement?
Lean empowers employees by involving them in process improvements. Teams gain ownership of their work, contributing ideas and solutions. This approach fosters accountability, collaboration, and a sense of purpose.
What is the role of Kaizen in Lean Methodology?
Kaizen emphasizes small, incremental changes for continuous improvement. It encourages collaboration across all levels of an organization, promoting innovation and accountability while driving long-term progress.
Can Lean Methodology be applied to small businesses?
Yes, Lean Methodology suits businesses of all sizes. Small businesses can use its principles to optimize resources, reduce costs, and improve customer satisfaction without requiring significant investments.
How does Lean Methodology address waste?
Lean identifies seven types of waste, such as overproduction and defects. Teams use tools like Value Stream Mapping to pinpoint inefficiencies and implement solutions that enhance productivity and reduce costs.
How can organizations sustain Lean practices over time?
Organizations sustain Lean practices by embedding continuous improvement into their culture. Regular training, leadership support, and performance reviews ensure that Lean principles remain effective and aligned with goals.
Note: For more insights on Lean Methodology and its applications, contact us today to explore how it can transform your organization.