How to Identify and Use Business Process Improvement Frameworks
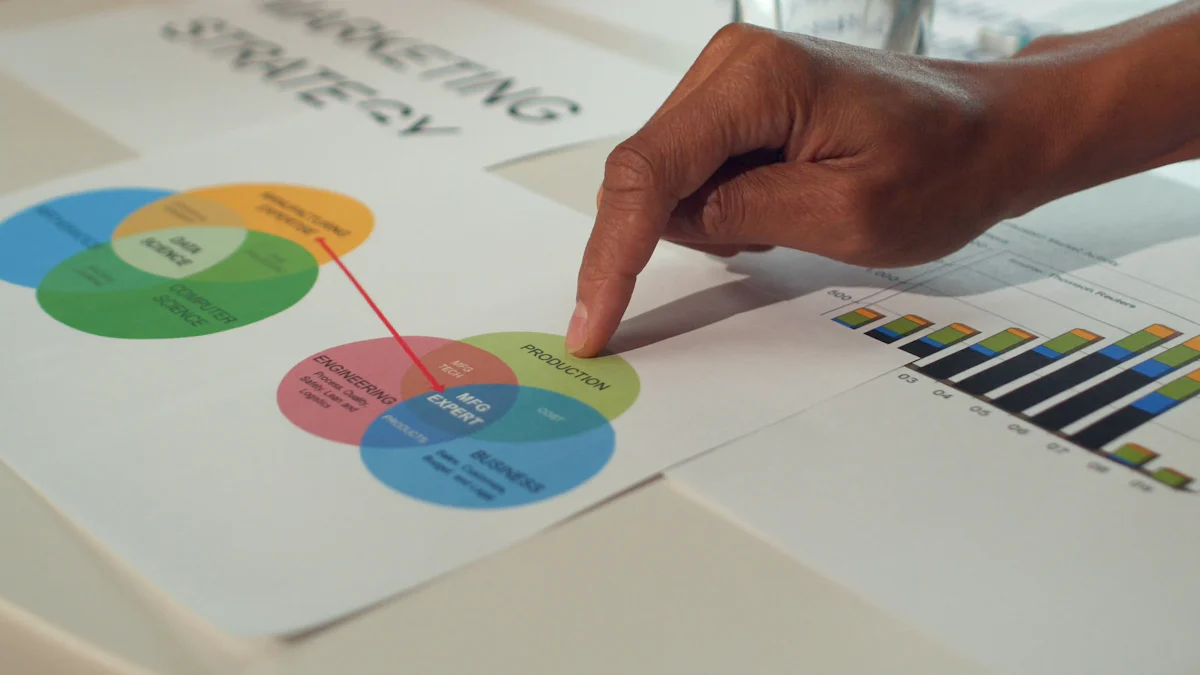
Business Process Improvement Methodologies offer structured approaches to optimize operations and enhance organizational performance. These methodologies empower businesses to streamline workflows, eliminate inefficiencies, and achieve measurable outcomes. For instance, organizations utilizing these frameworks have reported productivity gains of 30% to 50%, far surpassing traditional IT or ERP projects. By focusing on quality, cost reduction, and customer satisfaction, these methodologies drive tangible results. Gaining the right Knowledge about these frameworks tailored to specific business needs ensures alignment with goals, enabling teams to adapt and thrive in competitive markets, particularly in the realm of Sales and Business Management.
Key Takeaways
Business process improvement frameworks streamline operations, leading to productivity gains of 30% to 50%.
These methodologies enhance customer satisfaction by optimizing service delivery and reducing errors.
Selecting the right framework involves assessing your business goals, current challenges, and industry-specific needs.
Engaging stakeholders and building a dedicated team are crucial for successful implementation of process improvement initiatives.
Utilizing technology and tools like Kanban boards can significantly enhance workflow visualization and task management.
Continuous monitoring and adapting based on feedback ensure that improvements remain effective and aligned with business objectives.
Fostering a culture of continuous improvement empowers employees to contribute to ongoing enhancements, driving long-term success.
What Are Business Process Improvement Frameworks?
Business process improvement frameworks serve as structured systems designed to analyze, enhance, and optimize workflows. These frameworks provide organizations with a clear roadmap to identify inefficiencies, implement changes, and achieve measurable outcomes. By focusing on continuous improvement, they empower teams to align processes with business objectives, ensuring long-term success in dynamic markets.
Definition and Purpose
Business process improvement frameworks aim to refine operations by eliminating waste, improving quality, and optimizing resource utilization. They rely on data-driven approaches to evaluate existing processes and identify areas for enhancement. Organizations use these frameworks to create a culture of collaboration and innovation, enabling teams to adapt to evolving challenges. The ultimate goal is to streamline workflows, reduce costs, and deliver superior value to customers.
"Process improvement isn’t just a buzzword; it’s the driving force behind enhanced efficiency, cost savings, improved quality, and heightened customer satisfaction."
These frameworks also act as tools for fostering teamwork. By providing a common language and methodology, they encourage cross-functional collaboration, ensuring that all stakeholders contribute to achieving organizational goals. This structured approach transforms process improvement from a reactive measure into a proactive strategy for growth.
Key Benefits of Using Frameworks
Improved Efficiency and Productivity
Business process improvement methodologies help organizations identify bottlenecks and redundancies in their workflows. By addressing these issues, teams can complete tasks faster and with fewer resources. For example, systems that adopt these methodologies often report significant gains in productivity, as streamlined processes allow employees to focus on high-value activities. This improvement not only enhances operational efficiency but also boosts overall output.
Enhanced Customer Satisfaction
Optimized processes lead to better service delivery, which directly impacts customer satisfaction. When organizations reduce errors and improve response times, customers experience higher-quality interactions. Business process improvement ensures that teams consistently meet or exceed customer expectations, fostering loyalty and trust. This focus on quality strengthens the relationship between businesses and their clients, driving long-term success.
Cost Reduction and Resource Optimization
Inefficient processes often result in wasted time, materials, and labor. Process improvement methodologies address these inefficiencies by identifying areas where resources can be better utilized. Organizations that implement these frameworks often achieve significant cost savings by eliminating unnecessary steps and reallocating resources effectively. This optimization not only reduces expenses but also enhances the sustainability of operations.
Why Are Business Process Improvement Frameworks Important?
Addressing Operational Challenges
Organizations often face inefficiencies, bottlenecks, and quality issues that hinder their performance. Business process improvement frameworks provide structured methodologies to tackle these challenges. For example, the Six Sigma methodology focuses on identifying and eliminating defects in processes. By minimizing variability, teams can enhance the quality of outputs and reduce errors. This approach ensures smoother workflows and better resource utilization.
Historical examples highlight the effectiveness of these frameworks. Xerox, a global print leader, successfully reduced its supplier base and cut manufacturing costs by 50% using Total Quality Management (TQM). Additionally, it decreased quality issues by approximately 67%. These results demonstrate how structured frameworks can address operational inefficiencies and drive measurable improvements.
"Operational challenges are inevitable, but structured frameworks transform them into opportunities for growth."
By adopting these methodologies, organizations can proactively identify weak points and implement solutions. This proactive approach fosters resilience and adaptability, enabling teams to overcome obstacles and maintain consistent performance.
Aligning Processes with Business Goals
Business process improvement frameworks help organizations align their workflows with strategic objectives. Clear alignment ensures that every process contributes to achieving overarching goals. For instance, Lean manufacturing, a methodology rooted in the Toyota Production System, emphasizes waste reduction and value creation. This focus ensures that resources are directed toward activities that add value to the organization.
When processes align with business goals, teams work more cohesively. Cross-functional collaboration becomes seamless, as everyone shares a unified vision. This alignment also enhances decision-making, as leaders can evaluate processes based on their contribution to strategic priorities. The result is a more focused and efficient organization.
Staying Competitive in a Dynamic Market
In today’s fast-paced business environment, staying competitive requires continuous improvement. Business process improvement frameworks enable organizations to adapt to changing market demands. Lean manufacturing, for example, reduces waste and optimizes costs, allowing businesses to offer competitive pricing without compromising quality.
The rise of TQM after World War II marked a pivotal shift in industrial practices. It introduced a comprehensive approach to quality control, which remains relevant in modern markets. Companies that embrace such frameworks can respond quickly to customer needs and industry trends. This agility ensures they remain ahead of competitors.
"Adaptability is the cornerstone of success in dynamic markets."
By implementing these frameworks, organizations can build a culture of innovation and continuous improvement. This culture not only drives operational excellence but also positions businesses as leaders in their industries.
How to Identify the Right Framework for Your Business
Selecting the right business process improvement framework requires a thorough understanding of your organization’s unique needs. A well-chosen framework aligns with business objectives, addresses challenges, and ensures sustainable growth. The following steps provide a structured approach to identifying the most suitable framework.
Assessing Your Business Goals and Objectives
Every organization operates with specific goals in mind. These goals may include improving efficiency, reducing costs, or enhancing customer satisfaction. Identifying these objectives serves as the foundation for selecting an appropriate framework. For example, if the primary goal is to minimize defects in production, Six Sigma might be the ideal choice due to its focus on quality and precision.
"Aligned training programs deliver tangible business results and measurable ROI."
By aligning the framework with business goals, organizations can achieve better outcomes. This alignment ensures that every process improvement effort contributes directly to strategic priorities. Teams can then focus their energy on initiatives that drive measurable success.
Evaluating Current Challenges and Pain Points
Understanding existing challenges is crucial for determining the right framework. Organizations often face bottlenecks, inefficiencies, or resource constraints that hinder performance. A detailed evaluation of these pain points helps identify areas requiring immediate attention. For instance, if delays in workflow are a recurring issue, Lean methodologies may offer solutions by eliminating waste and streamlining processes.
A comprehensive assessment also highlights gaps in current operations. Addressing these gaps with a targeted framework enhances communication and drives process adoption. This proactive approach supports broader business process management efforts, ensuring smoother implementation and long-term success.
Considering Industry-Specific Needs
Different industries have unique requirements that influence the choice of a framework. Manufacturing sectors often benefit from Lean or Total Quality Management (TQM) due to their emphasis on efficiency and quality. On the other hand, service-based industries may find Agile or Kaizen more suitable for fostering adaptability and continuous improvement.
Organizations must also consider regulatory requirements and market dynamics. For example, healthcare providers may prioritize frameworks that enhance patient care while complying with strict regulations. By tailoring the framework to industry-specific needs, businesses can ensure relevance and effectiveness in their improvement efforts.
Analyzing Resource Availability and Constraints
Organizations must evaluate their available resources and identify constraints before selecting a business process improvement framework. This step ensures that the chosen methodology aligns with the organization’s capacity to implement and sustain changes effectively.
Assessing Human Resources
Teams play a critical role in process improvement. Organizations should evaluate whether they have skilled personnel to lead and execute the framework. For instance, methodologies like Six Sigma require trained professionals, such as Black Belts or Green Belts, to analyze data and implement solutions. If internal expertise is lacking, investing in training programs becomes essential.
"Aligned training programs deliver tangible business results and measurable ROI."
By equipping employees with the necessary skills, organizations can enhance their ability to adopt and sustain process improvements. This investment not only builds internal capabilities but also fosters a culture of continuous learning and innovation.
Evaluating Financial Resources
Implementing a business process improvement framework often involves costs, including training, software tools, and potential process redesigns. Organizations must assess their budgets to determine what level of investment is feasible. For example, Lean methodologies may require minimal financial outlay, focusing on waste reduction using existing resources. In contrast, frameworks like Total Quality Management (TQM) might demand more extensive financial commitments for quality control systems.
A clear understanding of financial constraints helps organizations prioritize initiatives and allocate resources effectively. This approach ensures that process improvement efforts remain sustainable without straining budgets.
Considering Technological Capabilities
Technology serves as a backbone for many process improvement frameworks. Tools for process mapping, data analysis, and workflow automation can significantly enhance implementation. Organizations should evaluate their current technological infrastructure to determine its compatibility with the chosen framework. For example, adopting Kanban may require digital boards or software to visualize workflows and track progress.
If existing systems fall short, upgrading technology becomes a priority. Investing in tools like Lucidchart or Microsoft Visio can streamline process mapping and foster better communication among teams. These tools enhance collaboration and ensure smoother adoption of the framework.
Identifying Operational Constraints
Operational constraints, such as time limitations or regulatory requirements, can impact the feasibility of certain frameworks. For instance, industries with strict compliance standards, like healthcare, may need frameworks tailored to meet these demands. Organizations should also consider the time required to implement changes. Frameworks like Kaizen, which focus on incremental improvements, may suit businesses with limited capacity for large-scale overhauls.
By addressing operational constraints early, organizations can select frameworks that align with their unique circumstances. This proactive approach minimizes disruptions and ensures a smoother transition during implementation.
"A Business Process Framework enhances communication and drives process adoption."
Analyzing resources and constraints provides a realistic foundation for process improvement. This evaluation ensures that organizations choose frameworks that match their capabilities, enabling teams to achieve measurable success. For further guidance on aligning resources with the right framework, reach out to our experts today.
Overview of Key Business Process Improvement Methodologies
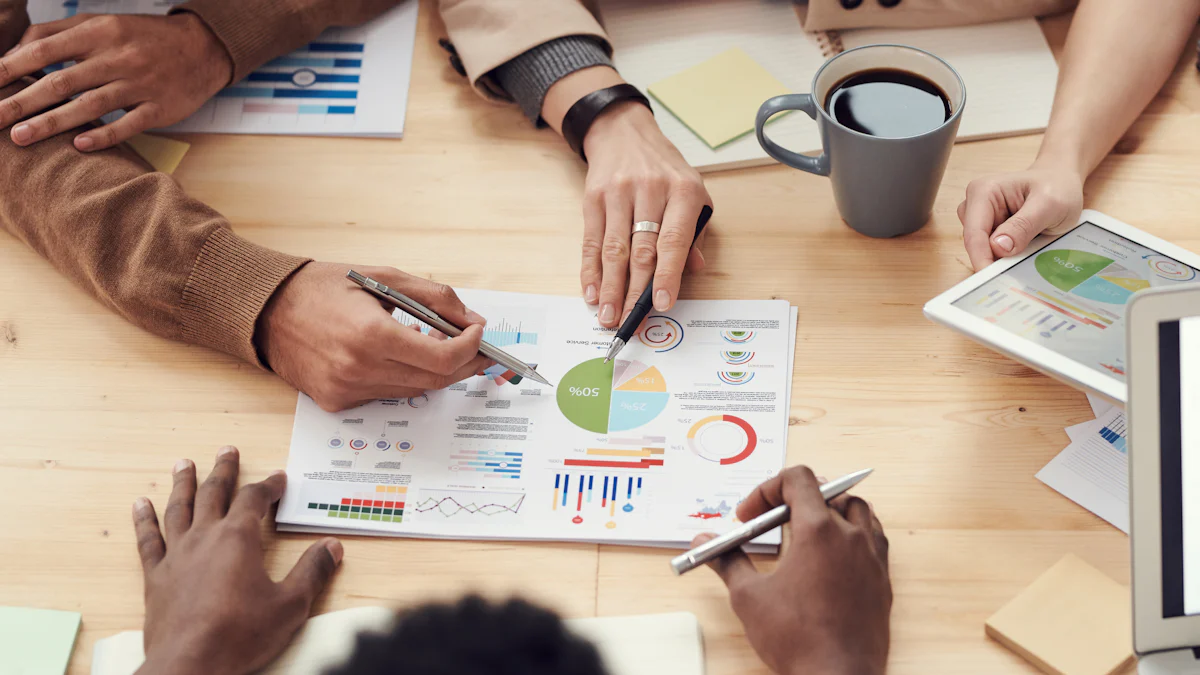
Business process improvement methodologies provide structured approaches to enhance workflows, reduce inefficiencies, and achieve measurable outcomes. Each methodology offers unique principles and tools tailored to address specific business challenges. Below is an exploration of three widely adopted methodologies: Six Sigma, Lean, and Kanban.
Six Sigma
Overview and Core Principles
Six Sigma focuses on reducing process variation and eliminating defects to improve quality and efficiency. Developed by Motorola in the 1980s, this methodology uses a data-driven approach to identify and resolve issues within processes. The core principles of Six Sigma include:
Define: Clearly outline the problem and project goals.
Measure: Collect data to understand current performance.
Analyze: Identify root causes of inefficiencies or defects.
Improve: Implement solutions to address these root causes.
Control: Monitor changes to ensure sustained improvements.
The six sigma methodology emphasizes precision and consistency, making it ideal for industries requiring high-quality standards, such as manufacturing and healthcare.
Example Applications in Business
Organizations use Six Sigma to enhance production processes, reduce waste, and improve customer satisfaction. For instance, a manufacturing company might apply Six Sigma to minimize defects in assembly lines, leading to higher product quality and reduced costs. Similarly, service-based businesses can use this methodology to streamline operations, such as reducing wait times in customer support centers. These applications demonstrate how Six Sigma drives tangible improvements across diverse sectors.
Lean
Overview and Core Principles
Lean methodology prioritizes waste elimination and value creation. Originating from the Toyota Production System, Lean focuses on delivering maximum value to customers with minimal resources. Its core principles include:
Value Identification: Determine what customers value most.
Value Stream Mapping: Analyze workflows to identify waste.
Flow Optimization: Ensure smooth and uninterrupted processes.
Pull System: Produce only what is needed, based on demand.
Continuous Improvement: Regularly refine processes to maintain efficiency.
Lean encourages teams to adopt a customer-centric mindset, ensuring that every activity contributes to delivering value.
Example Applications in Business
Lean has proven effective in industries ranging from manufacturing to healthcare. A hospital, for example, might use Lean to reduce patient wait times by streamlining administrative processes. In retail, businesses can optimize inventory management to prevent overstocking or stockouts. These examples highlight Lean’s versatility in improving operational efficiency and customer satisfaction.
Kanban
Overview and Core Principles
Kanban is a visual workflow management tool designed to improve task organization and efficiency. Originating from Lean principles, Kanban uses visual boards to track progress and identify bottlenecks. Its core principles include:
Visualize Work: Use boards to display tasks and their statuses.
Limit Work in Progress (WIP): Restrict the number of tasks being worked on simultaneously.
Focus on Flow: Ensure tasks move smoothly through the workflow.
Continuous Improvement: Regularly evaluate and refine processes.
Kanban promotes transparency and collaboration, enabling teams to manage workloads effectively.
Example Applications in Business
Kanban is widely used in software development, project management, and other industries requiring task prioritization. A software development team might use Kanban boards to track coding, testing, and deployment stages, ensuring timely project completion. Similarly, marketing teams can manage campaign tasks, such as content creation and distribution, using Kanban to maintain clarity and focus. These applications demonstrate Kanban’s ability to enhance productivity and teamwork.
Total Quality Management (TQM)
Overview and Core Principles
Total Quality Management (TQM) represents a comprehensive approach to improving quality across all organizational processes. This methodology emphasizes the importance of customer satisfaction, continuous improvement, and employee involvement. TQM integrates quality control into every aspect of operations, ensuring that all processes align with organizational goals.
The core principles of TQM include:
Customer Focus: Prioritizing customer needs and expectations in every process.
Total Employee Involvement: Encouraging all employees to participate in quality improvement initiatives.
Process-Centered Approach: Concentrating on optimizing workflows to enhance efficiency and output.
Integrated System: Aligning all departments and processes to achieve shared objectives.
Continuous Improvement: Regularly evaluating and refining processes to maintain high standards.
Fact-Based Decision Making: Using data and analysis to guide improvements and resolve issues.
TQM fosters a culture of accountability and collaboration. By involving employees at all levels, organizations can create a unified effort toward achieving excellence.
Example Applications in Business
Organizations across various industries have successfully implemented TQM to enhance quality and performance. For example, manufacturing companies often use TQM to reduce defects in production lines. By focusing on process optimization and employee training, these businesses achieve higher product quality and lower operational costs.
In the healthcare sector, TQM helps improve patient care by streamlining administrative processes and ensuring compliance with regulatory standards. Hospitals adopting TQM often report reduced errors and improved patient satisfaction. These examples highlight how TQM drives measurable improvements in both product and service-based industries.
Business Process Reengineering (BPR)
Overview and Core Principles
Business Process Reengineering (BPR) focuses on fundamentally redesigning workflows to achieve dramatic improvements in performance. Unlike incremental improvement methodologies, BPR seeks to overhaul processes entirely, eliminating inefficiencies and redundancies.
The core principles of BPR include:
Focus on Outcomes: Designing processes to achieve specific results rather than adhering to existing workflows.
Radical Redesign: Rethinking processes from the ground up to maximize efficiency and effectiveness.
Use of Technology: Leveraging advanced tools and systems to automate tasks and enhance productivity.
Cross-Functional Collaboration: Encouraging teams from different departments to work together in redesigning processes.
BPR challenges traditional methods by encouraging organizations to question established practices. This methodology aims to create streamlined workflows that align with strategic objectives.
Example Applications in Business
Many organizations have used BPR to transform their operations. For instance, a retail company might redesign its supply chain to reduce delivery times and improve inventory management. By implementing automated systems and restructuring workflows, the company can achieve faster order fulfillment and lower costs.
In the financial sector, BPR has helped banks optimize loan approval processes. By eliminating unnecessary steps and integrating digital tools, banks can provide quicker responses to customers while maintaining accuracy. These applications demonstrate how BPR enables businesses to achieve significant performance gains.
Plan-Do-Check-Act (PDCA)
Overview and Core Principles
The Plan-Do-Check-Act (PDCA) cycle is a systematic approach to continuous improvement. Originally developed by Walter Shewhart and popularized by W. Edwards Deming, PDCA provides a structured framework for testing and refining processes.
The four stages of PDCA include:
Plan: Identify a problem or opportunity and develop a strategy to address it.
Do: Implement the plan on a small scale to test its effectiveness.
Check: Evaluate the results to determine whether the plan achieved its objectives.
Act: Make necessary adjustments and implement the solution on a larger scale.
PDCA promotes iterative improvement, allowing organizations to adapt quickly to changing conditions. This methodology encourages teams to learn from each cycle and build on their successes.
Example Applications in Business
PDCA has proven effective in various industries. In manufacturing, companies use PDCA to refine production processes. For example, a factory might test a new assembly line configuration to reduce waste and improve efficiency. After evaluating the results, the company can implement the changes across all production lines.
Service-based organizations also benefit from PDCA. A customer support team might use the cycle to improve response times. By testing new communication tools and analyzing their impact, the team can identify the best solutions for enhancing customer satisfaction. These examples illustrate how PDCA supports continuous improvement in diverse settings.
Kaizen
Overview and Core Principles
Kaizen, a Japanese term meaning "continuous improvement," represents a philosophy that encourages incremental changes to enhance processes, systems, and workflows. This methodology focuses on involving every employee, from top management to frontline workers, in identifying inefficiencies and implementing solutions. By fostering a culture of collaboration and innovation, Kaizen ensures that organizations continuously refine their operations to achieve better results.
The core principles of Kaizen include:
Employee Involvement: Encouraging all team members to contribute ideas for improvement.
Incremental Changes: Implementing small, manageable adjustments rather than large-scale overhauls.
Focus on Process: Prioritizing the optimization of workflows to eliminate waste and inefficiencies.
Standardization: Establishing consistent practices to maintain improvements over time.
Continuous Feedback: Using regular evaluations to identify new opportunities for refinement.
Kaizen methodology emphasizes simplicity and practicality. It avoids complex strategies, focusing instead on actionable steps that deliver immediate and measurable benefits. This approach creates a dynamic environment where teams remain proactive in addressing challenges and seizing opportunities for growth.
"Kaizen transforms improvement into a daily habit, empowering teams to achieve excellence through small, consistent efforts."
Example Applications in Business
Kaizen has proven effective across various industries, from manufacturing to healthcare. In manufacturing, teams often use Kaizen to streamline production lines. For example, a factory might identify bottlenecks in assembly processes and implement minor adjustments to reduce delays. Over time, these changes lead to significant gains in efficiency and output.
In service-based industries, Kaizen enhances customer experiences by improving response times and service quality. A customer support team, for instance, might analyze call handling procedures and introduce small changes to reduce wait times. These adjustments not only improve customer satisfaction but also boost team productivity.
Healthcare organizations also benefit from Kaizen methodology. Hospitals frequently apply this approach to optimize patient care processes. By involving staff in identifying inefficiencies, they can reduce wait times, enhance treatment accuracy, and improve overall patient outcomes. These examples highlight Kaizen's versatility in driving continuous improvement across diverse sectors.
Kaizen's success lies in its ability to engage employees at all levels. By fostering a culture of shared responsibility and ongoing learning, organizations can sustain long-term improvements and adapt to evolving challenges. Teams that embrace Kaizen methodology consistently achieve higher efficiency, better quality, and greater customer satisfaction.
How to Effectively Implement Business Process Improvement Frameworks
Setting Clear Goals and Objectives
Establishing clear goals and objectives forms the foundation of any successful implementation of business process improvement frameworks. Organizations must define what they aim to achieve through these frameworks, whether it is reducing costs, improving efficiency, or enhancing customer satisfaction. Clear objectives provide direction and ensure that all efforts align with the organization’s strategic priorities.
For instance, teams implementing Lean Six Sigma often begin by identifying specific problems, such as production delays or high defect rates. By setting measurable goals, such as reducing defects by 20% within six months, organizations can track progress and evaluate success. This clarity helps teams focus on actionable steps and avoid unnecessary distractions.
"A well-defined goal transforms a vague ambition into a tangible target."
To ensure effectiveness, organizations should communicate these goals across all levels. Employees must understand how their roles contribute to achieving these objectives. This shared understanding fosters accountability and encourages collaboration, creating a unified effort toward continuous process improvement.
Engaging Stakeholders and Building a Team
Stakeholder engagement plays a critical role in the successful implementation of business process improvement frameworks. Organizations must involve key stakeholders, including leadership, managers, and frontline employees, from the outset. Their input ensures that the framework addresses real challenges and gains the necessary support for implementation.
Building a dedicated team to lead the initiative is equally important. This team should include individuals with diverse expertise, such as process analysts, project managers, and subject matter experts. For example, implementing Total Quality Management (TQM) often requires cross-functional collaboration to optimize workflows and improve quality across departments.
"Engaged stakeholders and cohesive teams drive the success of process improvement initiatives."
Training team members on the chosen framework enhances their ability to execute the plan effectively. For methodologies like Six Sigma, organizations may need to invest in certifications, such as Green Belt or Black Belt training, to equip employees with the necessary skills. This investment not only builds internal capabilities but also fosters a culture of innovation and excellence.
Using Tools and Technology to Support Implementation
The right tools and technology significantly enhance the implementation of business process improvement frameworks. Tools like Kanban boards provide visual representations of workflows, helping teams track progress and identify bottlenecks. These systems promote transparency and enable teams to manage tasks more efficiently.
Process mapping software, such as Lucidchart or Microsoft Visio, allows organizations to analyze existing workflows and design optimized processes. For example, teams using Lean Manufacturing can leverage these tools to identify waste and streamline operations. Similarly, automation tools can reduce manual tasks, freeing up resources for higher-value activities.
"Technology transforms process improvement from a manual effort into a streamlined operation."
Organizations must also ensure that their technological infrastructure aligns with the chosen framework. For instance, implementing Plan-Do-Check-Act (PDCA) may require tools for data collection and analysis to monitor progress and refine strategies. By integrating technology into their approach, organizations can achieve greater efficiency and sustain improvements over time.
Monitoring Progress and Measuring Success
Monitoring progress and measuring success are essential steps in implementing business process improvement frameworks. These actions ensure that organizations stay on track and achieve their desired outcomes. Teams must establish clear metrics to evaluate performance and identify areas for further refinement.
1. Define Key Performance Indicators (KPIs):
Organizations should select KPIs that align with their goals. For example, a team using Lean Manufacturing might track metrics like cycle time, defect rates, or inventory levels. These indicators provide measurable benchmarks to assess the effectiveness of the framework. Regularly reviewing KPIs helps teams identify trends and make data-driven decisions.
2. Leverage Technology for Real-Time Tracking:
Tools like Kanban boards and process mapping software enable teams to monitor workflows visually. These systems highlight bottlenecks and inefficiencies, allowing for immediate corrective action. For instance, a team implementing Lean Six Sigma can use data analytics tools to measure process variation and ensure consistent quality. Technology simplifies tracking and fosters transparency across departments.
3. Conduct Regular Reviews:
Periodic evaluations ensure that improvements remain sustainable. Teams should schedule reviews to assess progress against established KPIs. For example, organizations using the Plan-Do-Check-Act (PDCA) cycle can analyze results during the "Check" phase to determine if adjustments are needed. These reviews encourage continuous learning and adaptation.
4. Celebrate Milestones:
Recognizing achievements motivates teams and reinforces a culture of improvement. Celebrating milestones, such as reducing waste by a specific percentage, boosts morale and encourages further engagement. This practice fosters a sense of accomplishment and commitment to long-term success.
"What gets measured gets managed. Clear metrics and consistent tracking drive meaningful improvements."
Adapting and Iterating Based on Feedback
Adapting and iterating based on feedback ensures that business process improvement frameworks remain effective in dynamic environments. Organizations must remain flexible and responsive to changing conditions.
1. Gather Feedback from Stakeholders:
Stakeholders, including employees and customers, provide valuable insights into the effectiveness of implemented changes. Teams should actively seek input to identify pain points or areas for enhancement. For instance, a company using Total Quality Management (TQM) might conduct employee surveys to understand how process changes impact daily operations.
2. Analyze Data for Continuous Improvement:
Data analysis plays a critical role in identifying trends and opportunities for refinement. Teams using Six Sigma can leverage statistical tools to pinpoint root causes of recurring issues. By addressing these causes, organizations can implement targeted solutions that drive sustained improvements.
3. Embrace Incremental Changes:
Frameworks like Kaizen emphasize small, manageable adjustments rather than large-scale overhauls. This approach allows teams to test changes on a smaller scale before full implementation. Incremental improvements reduce risks and ensure that processes evolve in alignment with organizational goals.
4. Adjust Frameworks to Fit Evolving Needs:
Business environments often change due to market demands, technological advancements, or regulatory requirements. Organizations must adapt their methodologies to remain relevant. For example, a team initially using Lean Manufacturing might integrate elements of Kanban to enhance workflow visualization and responsiveness.
5. Document Lessons Learned:
Recording successes and challenges creates a knowledge base for future initiatives. Teams can refer to these lessons to avoid repeating mistakes and replicate successful strategies. This practice strengthens the organization’s ability to adapt and innovate over time.
"Adaptation is not a one-time event; it is an ongoing process that ensures frameworks remain effective and aligned with business objectives."
Tools and Resources for Business Process Improvement
Software Tools for Process Mapping and Analysis
Software tools play a vital role in enhancing business process improvement efforts. These tools simplify the visualization and analysis of workflows, enabling teams to identify inefficiencies and optimize operations. Lucidchart, Microsoft Visio, and Bizagi are among the most widely used tools for business process mapping and analysis.
Lucidchart: This cloud-based tool allows teams to create detailed process maps and flowcharts. Its intuitive interface makes it easy to collaborate in real time, ensuring that all stakeholders contribute to process optimization.
Microsoft Visio: Known for its versatility, Visio provides advanced diagramming capabilities. Teams can use it to design complex workflows, analyze bottlenecks, and propose streamlined solutions.
Bizagi: This platform combines process mapping with automation features. It enables organizations to model workflows and implement business process automation, ensuring smoother transitions from planning to execution.
These tools empower teams to visualize processes clearly, identify areas for improvement, and implement changes effectively. By leveraging such technologies, organizations can enhance their ability to achieve measurable outcomes.
"Effective process mapping tools transform abstract workflows into actionable insights, driving meaningful improvements."
Training and Certification Programs
Training and certification programs equip teams with the skills and knowledge needed to implement business process improvement methodologies successfully. Programs like Six Sigma Certification, Lean Training, and TQM Workshops provide structured learning opportunities for professionals at all levels.
Six Sigma Certification: This program focuses on data-driven problem-solving techniques. Participants learn to identify defects, reduce variability, and improve quality. Certifications range from Yellow Belt to Black Belt, catering to different expertise levels.
Lean Training: Lean training emphasizes waste reduction and value creation. It equips participants with practical tools to streamline workflows and enhance efficiency. Many organizations use Lean principles to foster a culture of continuous improvement.
TQM Workshops: Total Quality Management workshops focus on creating a company-wide commitment to quality. These sessions teach participants how to align processes with customer expectations and implement continuous improvement strategies.
Investing in training programs builds internal capabilities and fosters a culture of excellence. Organizations that prioritize employee development often achieve better results in their process improvement initiatives.
"Well-trained teams drive the success of business process improvement efforts, ensuring sustainable growth and innovation."
Case Studies and Industry Examples
Real-world examples demonstrate the effectiveness of business process improvement methodologies across various industries. Successful implementations in manufacturing and healthcare highlight the transformative potential of these approaches.
Manufacturing: A global automotive company adopted Lean principles to optimize its production lines. By eliminating waste and improving workflow efficiency, the company reduced production costs by 25% and increased output by 30%. This case underscores the value of aligning processes with customer demands.
Healthcare: A leading hospital implemented Total Quality Management (TQM) to enhance patient care. By streamlining administrative processes and improving communication among staff, the hospital reduced patient wait times by 40% and achieved higher satisfaction rates. This example illustrates how TQM fosters better outcomes in service-based industries.
These case studies highlight the versatility of business process improvement frameworks. They show how organizations can adapt methodologies to address unique challenges and achieve measurable success.
"Real-world success stories inspire teams to embrace process improvement, proving that small changes can lead to significant results."
Common Challenges in Business Process Improvement and How to Overcome Them
Resistance to Change
Resistance to change often emerges as one of the most significant barriers in business process improvement. Employees may feel uncertain about new methodologies or fear that changes could disrupt their routines. This hesitation can slow down progress and hinder the adoption of new frameworks.
To address this challenge, organizations must foster a culture of collaboration and inclusivity. Engaging employees at all levels in the decision-making process helps build trust and reduces resistance. For example, the Kaizen methodology emphasizes involving employees in driving change. By encouraging team members to contribute ideas for improvement, organizations can create a sense of ownership and accountability.
Leaders should also communicate the benefits of the proposed changes clearly. Highlighting how process improvements can reduce workloads, enhance efficiency, or improve job satisfaction can motivate employees to embrace the transformation. Regular training sessions and workshops further equip teams with the skills needed to adapt to new systems.
"Change becomes less intimidating when employees feel empowered to participate in the process."
By addressing concerns proactively and involving employees in the journey, organizations can overcome resistance and ensure smoother transitions.
Lack of Clear Communication
Clear communication serves as the backbone of successful process improvement initiatives. Without it, teams may struggle to understand objectives, roles, or the steps required to implement changes. Miscommunication can lead to confusion, delays, and even project failure.
To overcome this challenge, organizations should establish transparent communication channels. Regular meetings, detailed documentation, and visual tools like Kanban boards can help teams stay aligned. These tools provide a clear overview of tasks, progress, and responsibilities, ensuring everyone remains on the same page.
Leaders must also prioritize active listening. Encouraging feedback from employees allows organizations to identify potential misunderstandings and address them promptly. For instance, during the implementation of Total Quality Management (TQM), open communication ensures that all departments work cohesively toward shared goals.
"Effective communication transforms complex processes into manageable steps."
By fostering an environment of open dialogue and clarity, organizations can minimize confusion and enhance collaboration.
Insufficient Resources or Expertise
Limited resources or expertise often pose significant challenges in implementing business process improvement frameworks. Organizations may lack the financial capacity, skilled personnel, or technological tools required to execute changes effectively.
To address resource constraints, organizations should start by conducting a thorough assessment of their current capabilities. Identifying gaps in human resources, technology, or finances helps prioritize initiatives and allocate resources strategically. For example, frameworks like Kaizen focus on small, incremental changes that require minimal investment. This approach allows organizations to achieve improvements without overburdening their budgets.
Investing in employee training programs also builds internal expertise. Certifications such as Six Sigma Green Belt or Lean Training equip teams with the knowledge needed to implement frameworks successfully. Additionally, leveraging cost-effective tools like Lucidchart or Microsoft Visio can streamline process mapping and analysis.
"Resource limitations should not hinder progress; strategic planning and incremental improvements pave the way for success."
By addressing resource gaps and building internal capabilities, organizations can overcome this challenge and sustain long-term improvements.
Measuring and Sustaining Long-Term Success
Measuring and sustaining long-term success in business process improvement requires a structured approach. Organizations must focus on tracking progress, maintaining improvements, and fostering a culture of continuous enhancement. These steps ensure that the benefits of process improvement frameworks remain impactful over time.
Establishing Key Performance Indicators (KPIs)
Defining clear and measurable KPIs is essential for evaluating the success of implemented frameworks. Metrics should align with organizational goals and provide actionable insights. For example, teams using Kaizen methodology might track metrics such as waste reduction, productivity gains, or customer satisfaction levels. These indicators help organizations monitor progress and identify areas requiring further refinement.
"What gets measured gets improved. KPIs provide a roadmap for sustaining success."
Regularly reviewing these metrics ensures that teams stay focused on their objectives. By analyzing trends and patterns, organizations can make data-driven decisions to maintain efficiency and quality.
Conducting Periodic Audits and Reviews
Periodic audits play a critical role in sustaining improvements. These reviews allow organizations to assess whether processes continue to meet desired standards. For instance, systems implementing Lean principles might schedule quarterly evaluations to ensure waste elimination efforts remain effective. Audits also help identify new opportunities for optimization.
Teams should document findings from these reviews to create a knowledge base. This repository serves as a valuable resource for future initiatives, enabling organizations to replicate successful strategies and avoid past mistakes.
Encouraging Employee Involvement
Employee involvement is a cornerstone of sustained success. Engaging team members at all levels fosters accountability and innovation. Frameworks like Kaizen emphasize the importance of involving employees in identifying inefficiencies and proposing solutions. This approach not only enhances morale but also ensures that improvements align with operational realities.
Organizations can encourage participation through regular feedback sessions, workshops, or Kaizen events. These activities empower employees to take ownership of processes and contribute to ongoing enhancements.
"Sustained success stems from a culture where every employee feels empowered to drive improvement."
Leveraging Technology for Continuous Monitoring
Technology provides powerful tools for sustaining long-term success. Process mapping software, such as Lucidchart or Microsoft Visio, enables teams to visualize workflows and track changes over time. Automation tools streamline repetitive tasks, freeing up resources for strategic initiatives.
For example, organizations using Kanban boards can monitor task progress and identify bottlenecks in real time. These tools enhance transparency and ensure that teams remain aligned with their goals.
Building a Culture of Continuous Improvement
A culture of continuous improvement ensures that organizations remain adaptable in dynamic markets. Teams must embrace the philosophy of incremental change, as emphasized by Kaizen methodology. Small, consistent adjustments lead to significant long-term benefits.
Leaders play a vital role in fostering this culture. By recognizing achievements and encouraging innovation, they inspire teams to pursue excellence. Celebrating milestones, such as achieving a 10% reduction in waste, reinforces the value of sustained effort.
"Continuous improvement transforms success into a habit, ensuring organizations thrive in competitive environments."
Adapting to Evolving Needs
Business environments constantly evolve due to market demands, technological advancements, or regulatory changes. Organizations must remain flexible and adapt their frameworks to meet these challenges. For instance, a team initially focused on Lean principles might integrate elements of Six Sigma to enhance precision and quality.
Regularly revisiting goals and strategies ensures that process improvements remain relevant. This adaptability positions organizations to seize new opportunities and maintain a competitive edge.
By combining measurable metrics, employee engagement, and technological support, organizations can sustain the benefits of business process improvement frameworks. For tailored guidance on achieving long-term success, reach out to our experts today.
Real-World Examples of Successful Business Process Improvement
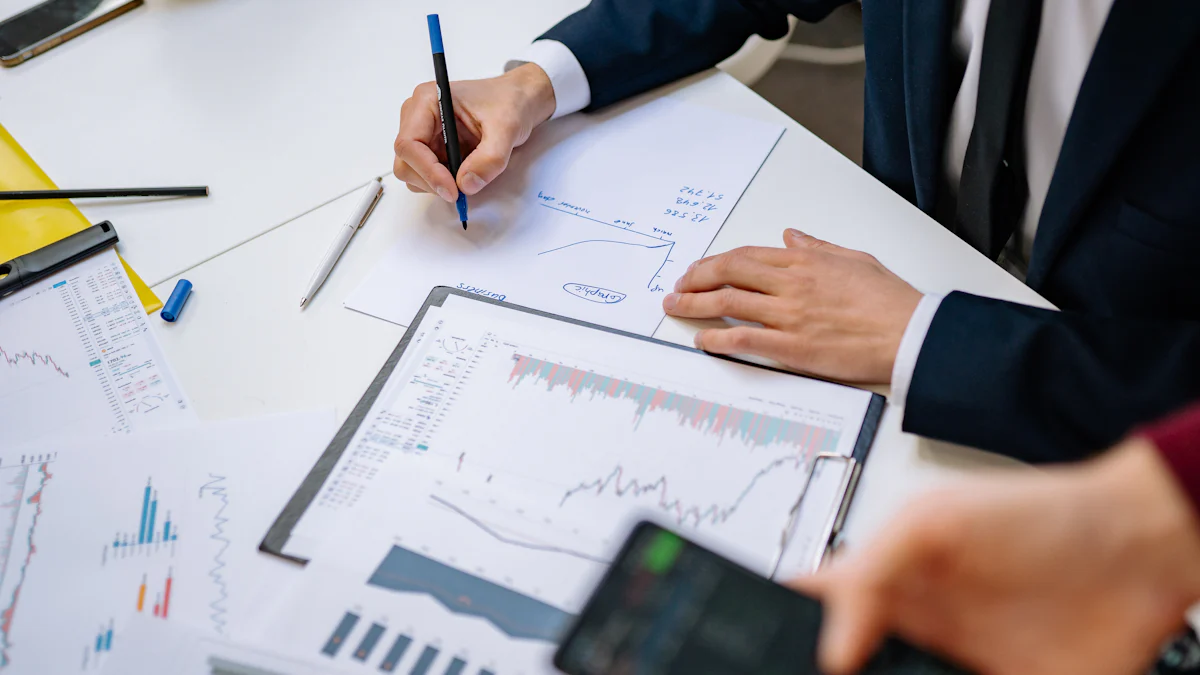
Case Study 1: Toyota and Lean Manufacturing
Toyota revolutionized the automotive industry by adopting Lean Manufacturing principles. This methodology, rooted in the Toyota Production System, focuses on eliminating waste and maximizing value for customers. Toyota identified inefficiencies in its production processes and implemented strategies to streamline workflows. By emphasizing continuous improvement, the company achieved remarkable results.
One of Toyota's key practices involved the use of "just-in-time" production. This approach ensured that materials arrived precisely when needed, reducing inventory costs and minimizing waste. Additionally, Toyota empowered its employees to identify and address inefficiencies on the production line. This culture of collaboration and accountability contributed to significant productivity gains.
The results of Toyota's Lean Manufacturing efforts were transformative. The company reduced production costs, improved product quality, and shortened delivery times. These achievements not only enhanced customer satisfaction but also solidified Toyota's position as a global leader in the automotive industry.
"Lean Manufacturing at Toyota demonstrates how a focus on value creation and waste elimination can drive operational excellence."
Case Study 2: Motorola and Six Sigma
Motorola pioneered the Six Sigma methodology in the 1980s to address quality issues and enhance operational efficiency. This data-driven approach aimed to reduce process variation and eliminate defects. Motorola's leadership recognized the need for a structured framework to improve performance and meet customer expectations.
The company implemented Six Sigma by training employees at various levels, including Green Belts and Black Belts, to lead improvement projects. Teams used the Define-Measure-Analyze-Improve-Control (DMAIC) framework to identify root causes of defects and implement targeted solutions. For example, Motorola applied Six Sigma to its manufacturing processes, reducing errors and improving product reliability.
The impact of Six Sigma at Motorola was profound. The company reported savings of over $16 billion within a decade of implementation. Additionally, Motorola's commitment to quality earned it the prestigious Malcolm Baldrige National Quality Award. This success story highlights the power of Six Sigma in driving measurable improvements and achieving long-term business goals.
"Motorola's adoption of Six Sigma showcases the effectiveness of data-driven methodologies in enhancing quality and efficiency."
Lessons Learned from These Examples
The success stories of Toyota and Motorola offer valuable insights into the implementation of business process improvement frameworks:
Leadership Commitment: Both companies demonstrated the importance of strong leadership in driving change. Leaders championed the adoption of Lean Manufacturing and Six Sigma, ensuring alignment with organizational goals. Research shows that when executives actively support learning initiatives, engagement rates triple.
Employee Involvement: Empowering employees to contribute to process improvement fosters a culture of collaboration. Toyota encouraged workers to identify inefficiencies, while Motorola trained teams to lead Six Sigma projects. This approach ensures that improvements are sustainable and widely adopted.
Focus on Measurable Outcomes: Both companies prioritized clear metrics to evaluate success. Toyota tracked waste reduction and delivery times, while Motorola measured defect rates and cost savings. These metrics provided actionable insights and guided continuous improvement efforts.
Adaptability and Innovation: Toyota and Motorola embraced change and innovation to remain competitive. By adopting Lean Manufacturing and Six Sigma, they addressed operational challenges and positioned themselves as industry leaders.
These lessons underscore the transformative potential of business process improvement frameworks. Organizations seeking similar results must prioritize leadership support, employee engagement, and a focus on measurable outcomes. For tailored guidance on implementing these methodologies, reach out to our experts today.
Business process improvement frameworks play a vital role in driving operational success. They empower organizations to enhance quality, boost productivity, and elevate customer experiences. With 58% of professionals actively engaged in these initiatives, the impact is evident across industries. Identifying the right framework involves assessing goals, challenges, and resources. Implementing it requires clear objectives, stakeholder involvement, and continuous monitoring. Organizations must take the first step by evaluating their processes and exploring suitable methodologies. By doing so, they can unlock measurable outcomes and foster a culture of continuous improvement. Reach out to learn how to begin this transformative journey.
FAQ
What is a business process improvement framework?
A business process improvement framework is a structured methodology designed to analyze, optimize, and enhance workflows within an organization. These frameworks help identify inefficiencies, eliminate waste, and align processes with business objectives. By using these systems, teams can achieve measurable outcomes such as cost reduction, improved efficiency, and enhanced customer satisfaction.
How do I choose the right framework for my business?
Selecting the right framework requires assessing your business goals, challenges, and resources. Start by identifying your objectives, such as reducing defects or improving customer service. Evaluate current pain points and consider industry-specific needs. For example, manufacturing teams often benefit from Lean or Six Sigma, while service-based industries may prefer Kaizen or Agile. Analyzing resource availability, including financial, human, and technological capacities, ensures the chosen framework aligns with your organization’s capabilities.
What are some popular business process improvement methodologies?
Several methodologies are widely used across industries:
Six Sigma: Focuses on reducing defects and process variation.
Lean: Prioritizes waste elimination and value creation.
Kanban: Visualizes workflows to improve task management.
Total Quality Management (TQM): Emphasizes quality improvement across all processes.
Kaizen: Encourages continuous, incremental improvements.
Each methodology offers unique tools and principles tailored to specific business needs.
How can technology support business process improvement?
Technology plays a crucial role in streamlining and supporting process improvement efforts. Tools like Lucidchart and Microsoft Visio assist in process mapping, while platforms such as ProjectManager provide real-time dashboards to monitor progress. Kanban boards, for instance, visually represent workflows, making it easier to identify bottlenecks and delays. By leveraging these tools, teams can enhance collaboration, track performance, and sustain improvements.
What are the benefits of using a visual tool like Kanban?
Kanban offers a clear visualization of workflows, enabling teams to track tasks and identify bottlenecks. By mapping out work stages on a Kanban board, team members gain real-time insights into task statuses. This transparency improves communication and helps prioritize tasks effectively. Additionally, Kanban promotes continuous improvement by encouraging teams to refine processes based on workflow observations.
How do I overcome resistance to change during process improvement?
Resistance to change often stems from uncertainty or fear of disruption. To address this, involve employees in the decision-making process and communicate the benefits of the changes clearly. Highlight how improvements can reduce workloads or enhance job satisfaction. Frameworks like Kaizen emphasize employee involvement, fostering a sense of ownership and accountability. Regular training sessions and open communication channels also help ease transitions.
What tools can help monitor progress during implementation?
Monitoring progress requires tools that provide real-time insights and data analysis. Platforms like Forecast offer dashboards to review project progress at a glance, helping teams identify bottlenecks or resource constraints. Similarly, ProjectManager consolidates data into project metrics, allowing teams to track performance efficiently. These tools ensure that organizations stay aligned with their goals and make data-driven decisions.
Can small businesses benefit from process improvement frameworks?
Yes, small businesses can greatly benefit from these frameworks. Methodologies like Kaizen and Lean focus on incremental changes and waste reduction, making them ideal for businesses with limited resources. Small teams can use tools like Kanban boards to visualize workflows and improve task management. By adopting these approaches, small businesses can enhance efficiency, reduce costs, and remain competitive.
How do I measure the success of a process improvement initiative?
Measuring success involves setting clear Key Performance Indicators (KPIs) aligned with organizational goals. Metrics such as defect rates, cycle times, or customer satisfaction scores provide actionable insights. Tools like Forecast and ProjectManager enable real-time tracking of these metrics. Regular reviews and audits ensure that improvements remain sustainable and aligned with business objectives.
What are the long-term benefits of adopting a business process improvement framework?
Adopting a business process improvement framework fosters a culture of continuous improvement. Organizations experience enhanced efficiency, reduced costs, and improved customer satisfaction. Over time, these frameworks help businesses adapt to market changes, maintain competitiveness, and achieve sustainable growth. Teams that embrace these methodologies consistently deliver higher-quality outcomes and drive innovation.