How to Master Six Sigma Process Mapping in 2025
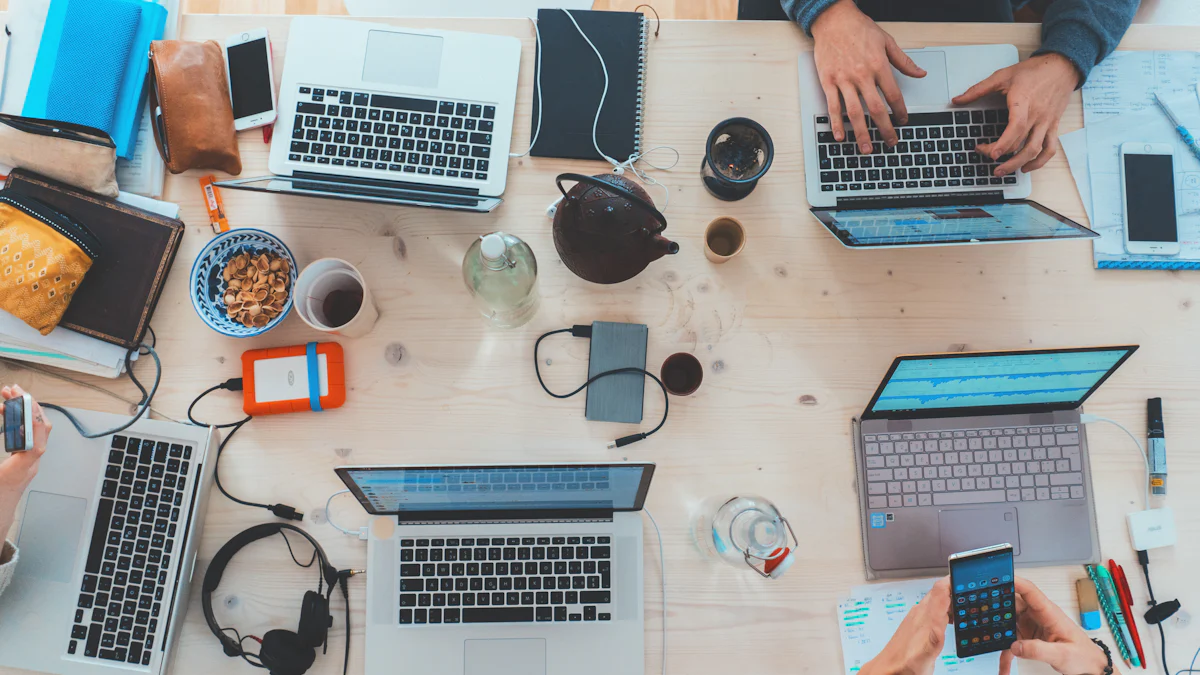
Six Sigma process mapping serves as a visual representation of workflows, enabling organizations to identify inefficiencies and optimize operations. It plays a pivotal role in process improvement by breaking down complex workflows into manageable steps. Businesses in 2025 face increasing pressure to streamline operations due to rapid technological advancements and evolving customer expectations. Mastering this skill ensures they remain competitive in a dynamic market.
Modern tools and trends have revolutionized process mapping. For instance, cloud-based platforms and AI-powered analytics provide real-time insights, making it easier to adapt to changes. A recent study highlights this shift, showing that only 12% of BPM projects now incorporate Six Sigma, compared to 21% in 2013:
Year | Percentage of BPM Projects with Six Sigma | Percentage of BPM Projects without Six Sigma |
---|---|---|
2013 | 21% | 79% |
2023 | 12% | 88% |
By leveraging these advancements, systems and teams can enhance hiring systems, improve business management, and sustain long-term success.
Process mapping is a critical tool in the Six Sigma methodology for identifying inefficiencies and waste in a project and streamlining it for maximum efficiency. It can be learned through online Six Sigma training. By mapping out each step in the project plan, Six Sigma practitioners can better understand how a project works and identify ways to optimize it.
Key Takeaways
Six Sigma process mapping shows how work is done and finds problems.
New tools like cloud apps and AI make mapping easier.
To make a process map, define the steps and collect data.
Working with different teams helps find hidden problems and share ideas.
Updating maps often keeps them correct and useful for current work.
Teaching workers Six Sigma gives them skills to improve processes.
Tracking things like time and mistakes helps measure progress.
Simple maps with clear details make them easier to understand.
Understanding Six Sigma Process Mapping
What Is Six Sigma Process Mapping
Six Sigma process mapping is a structured approach to visually representing workflows within an organization. It breaks down complex processes into smaller, manageable steps, making it easier to identify inefficiencies and areas for improvement. This method is a cornerstone of the Six Sigma methodology, which focuses on reducing variability, improving quality, and eliminating waste. By creating a process map, teams can better understand how tasks flow, pinpoint bottlenecks, and ensure that every step adds value to the final output.
Key principles define Six Sigma process mapping:
Reduction of Variability: Identifying and eliminating sources of inconsistency leads to more predictable outcomes.
Improvement of Quality: Mapping helps uncover defects and streamline workflows to enhance output quality.
Facilitation of Communication: Process maps serve as a shared visual tool, fostering collaboration among stakeholders.
Documentation and Standardization: They provide a clear, documented process for training and future improvements.
Key Components of Six Sigma Process Maps
Inputs, Outputs, and Process Steps
Every process map includes three critical elements: inputs, outputs, and the steps in between. Inputs represent the resources or information required to start the process. Outputs are the results or deliverables produced at the end. Process steps detail the sequence of activities that transform inputs into outputs. A clear visual representation of these elements helps teams identify inefficiencies and focus on value-added activities.
Roles and Responsibilities
A well-designed process map clarifies roles and responsibilities. It assigns accountability to specific individuals or teams for each step. This reduces confusion and ensures that everyone understands their part in achieving process improvement. For example, in a value stream map, roles are often linked to specific tasks, making it easier to track progress and address delays.
Metrics and Measurements
Metrics and measurements are essential for evaluating process performance. They provide data-driven insights into areas like cycle time, defect rates, and resource utilization. These metrics align with the DMAIC process (Define, Measure, Analyze, Improve, Control), enabling teams to monitor progress and sustain improvements over time.
Component | Contribution to Process Improvement |
---|---|
Documentation and Standardization | Provides a documented version of the process for training and future improvements, ensuring quality improvements are standardized and sustained. |
Purpose of Six Sigma Process Mapping
Identifying Inefficiencies and Waste
Six Sigma process mapping helps organizations uncover inefficiencies and eliminate waste. For instance, in the aerospace industry, inefficient maintenance procedures were identified through process mapping. This led to streamlined scheduling and reduced turnaround times, improving safety and reliability.
Streamlining Workflows
Process maps simplify workflows by visualizing the sequence of activities. This allows teams to remove unnecessary steps and focus on value-added tasks. In healthcare, for example, process mapping reduced patient wait times by 20%, enhancing care and satisfaction.
Enhancing Communication and Collaboration
Process maps act as a shared language for stakeholders. They improve communication by providing a clear visual representation of workflows. This fosters collaboration and ensures that everyone works toward the same goals. Teams can also use process mapping tools to track progress and measure key performance indicators (KPIs).
Step-by-Step Guide to Creating a Six Sigma Process Map
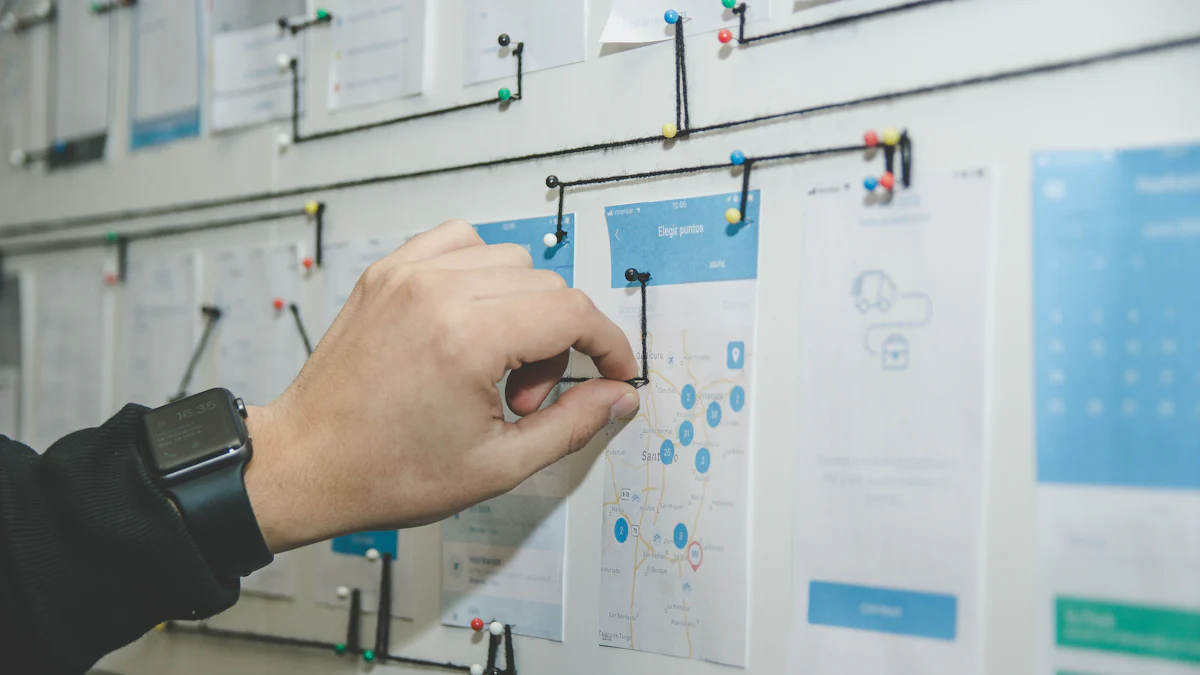
Step 1: Define the Process Context and Scope
Defining the context and scope is the foundation of creating an effective process map. This step ensures clarity about what the process entails and its boundaries. Follow these steps to define the context and scope:
Identify the specific process to map. For example, choose a hiring process or a customer onboarding workflow.
List all tasks, actions, and resources required to complete the process. This includes identifying tools, personnel, and materials involved.
Define the process scope by determining its start and end points. Specify who initiates the process and what constitutes successful completion.
Additionally, consider the following:
Determine the objectives of the process. For instance, is the goal to reduce cycle time or improve quality?
Identify interactions with external entities, such as suppliers or customers.
Establish critical milestones that indicate progress within the process.
By clearly defining the context and scope, systems and teams can ensure alignment and focus on the most critical aspects of the process.
Step 2: Gather Data and Identify Stakeholders
Accurate data and stakeholder involvement are essential for creating a reliable process map. Begin by defining the purpose of the map. This helps determine what information is needed and why. Next, identify all stakeholders, including process owners, team members, and external parties affected by the process.
Follow these steps to gather data and engage stakeholders:
Talk to individuals directly involved in the process. Their insights provide valuable details about day-to-day operations.
Review existing documentation, such as standard operating procedures or previous process maps.
Determine each stakeholder’s involvement and interest. For example, a process owner may focus on efficiency, while a customer may prioritize quality.
Plan how to engage stakeholders effectively. Use stakeholder mapping to analyze their roles and develop management plans.
Engaging stakeholders ensures the process map reflects real-world operations and gains buy-in for future improvements.
Step 3: Map the Process Flow
Mapping the process flow involves visually representing the sequence of activities. This step transforms raw data into a structured diagram that highlights how tasks connect and progress.
Using Flowcharts and Symbols
Flowcharts are a common tool for process mapping. Use standard symbols to represent different elements:
Ovals indicate start and end points.
Rectangles represent tasks or activities.
Diamonds show decision points.
Keep the flowchart simple and follow established rules. Ensure decision paths are clear and easy to differentiate. Avoid overloading the diagram with unnecessary images or colors, as this can reduce readability.
Sequencing Activities
Arrange activities in the correct order to reflect the actual process flow. For linear processes, use a straightforward workflow view. For processes involving multiple functional areas, consider a swim lane diagram. Swim lanes clearly show ownership and handoffs between teams, making it easier to identify bottlenecks.
By following these best practices, systems and teams can create accurate and comprehensive process maps that support decision-making and continuous improvement.
Step 4: Validate the Process Map
Validation ensures the process map accurately reflects real-world operations and aligns with organizational goals. This step involves reviewing the map with stakeholders and refining it based on their feedback. A validated process map serves as a reliable foundation for process improvement initiatives.
Techniques for Effective Validation
Teams can use several techniques to validate a process map effectively. These methods ensure the map is comprehensive and free of errors:
Technique | Description |
---|---|
Validate the process map with the mapping team and relevant stakeholders to ensure accuracy. | |
Encourage feedback | Solicit input from stakeholders to refine the map and incorporate necessary changes. |
Distribute the completed process map to major stakeholders for feedback and adjustments. | |
Diligent walkthrough | Team members should carefully review the map to ensure all steps are included and accurate. |
Stakeholder involvement is critical during this phase. Their insights help identify overlooked steps, clarify ambiguities, and confirm that the map aligns with organizational objectives. For example, a diligent walkthrough by team members can reveal missing decision points or redundant activities. Sharing the map with stakeholders also fosters collaboration and ensures buy-in for future process changes.
Tip: Use collaborative tools like cloud-based platforms to share the process map with stakeholders. These tools allow real-time feedback and streamline the validation process.
Step 5: Analyze the Process for Improvement Opportunities
Once validated, the process map becomes a powerful tool for identifying improvement opportunities. Analysis focuses on uncovering inefficiencies, bottlenecks, and non-value-added activities. Teams can then implement targeted solutions to enhance process performance.
Common Improvement Opportunities
Organizations often use methodologies like Lean, Kaizen, and Total Quality Management (TQM) to analyze processes. These approaches reveal specific areas for improvement and deliver measurable results:
Methodology | Improvement Opportunities | Results Achieved |
---|---|---|
Lean | Waste reduction in processes | |
25% improvement in quality | ||
Kaizen | Continuous improvement culture | 70% reduction in process-related problems |
45% improvement in employee engagement | ||
Total Quality Management (TQM) | Customer-focused quality standards | 40% fewer customer complaints |
35% higher customer satisfaction rates | ||
Business Process Reengineering (BPR) | Radical redesign of processes | 65% reduction in process cycle times |
75% decrease in process costs |
For example, Lean methodology focuses on eliminating waste, such as unnecessary steps or excessive handoffs. Kaizen fosters a culture of continuous improvement, encouraging teams to make incremental changes that enhance efficiency. By applying these methods, systems and teams can achieve significant reductions in cycle times, costs, and defects.
Steps for Process Analysis
Identify Bottlenecks: Examine the process map to locate delays or inefficiencies. For instance, a bottleneck may occur when approvals take too long.
Evaluate Non-Value-Added Activities: Highlight steps that do not contribute to the final output. Removing these steps can streamline workflows.
Assess Resource Utilization: Analyze how resources like time, labor, and materials are allocated. Optimizing resource use can improve overall efficiency.
Prioritize Improvement Areas: Focus on high-impact changes that align with organizational goals. For example, reducing cycle time in a manufacturing process may lead to faster delivery and higher customer satisfaction.
Note: Teams should use data-driven insights, such as defect rates or cycle times, to guide their analysis. Metrics from the process map provide a clear baseline for measuring improvement.
By following these steps, systems and teams can transform validated process maps into actionable roadmaps for success. This approach not only enhances operational efficiency but also supports long-term business growth.
Benefits of Six Sigma Process Mapping
Identifying Inefficiencies and Reducing Waste
Six Sigma process mapping provides a structured approach to uncover inefficiencies and eliminate waste. By visually representing workflows, systems and teams can identify unnecessary steps, bottlenecks, and non-value-added activities. For example, a value stream map highlights areas where delays or redundancies occur, enabling teams to focus on streamlining operations. This approach not only reduces waste but also enhances overall productivity.
The measurable benefits of using Six Sigma process mapping to reduce waste include improved understanding, increased efficiency, and cost reduction. The table below outlines these advantages:
Benefit | Description |
---|---|
Improved Understanding | Provides a visual representation of processes, aiding in identifying inefficiencies and waste. |
Increased Efficiency | Streamlines processes, reduces cycle times, and identifies root causes of inefficiencies. |
Enhanced Customer Satisfaction | Improves product/service quality by addressing inefficiencies, leading to higher customer loyalty. |
Cost Reduction | Identifies and eliminates waste, reducing costs and improving profitability. |
Improved Communication | Establishes a common framework for discussing processes, enhancing collaboration and decision-making. |
By focusing on eliminating defects and waste, organizations can achieve significant cost savings and improve customer satisfaction. This makes process mapping an essential tool for process improvement initiatives.
Improving Process Performance and Quality
Six Sigma process mapping enhances process performance by providing a clear visual representation of workflows. This clarity helps systems and teams understand inputs, outputs, and the steps involved. Identifying areas of waste, such as overproduction or unnecessary processing, allows teams to streamline workflows and improve efficiency.
Key benefits of process mapping for performance and quality include:
Reduction of Variability: Visualizing the process helps identify and eliminate sources of variability, leading to consistent outcomes.
Improvement of Quality: Understanding process flow aids in identifying and removing defects, enhancing output quality.
Facilitation of Communication: Process maps serve as effective tools for stakeholder communication, fostering collaboration.
For instance, a manufacturing company used process mapping to reduce cycle times and improve product quality. By addressing inefficiencies, they achieved higher profitability and customer satisfaction. These improvements demonstrate how mapping supports both operational excellence and long-term business success.
Enhancing Collaboration Across Teams
Six Sigma process mapping fosters collaboration by creating a shared understanding of workflows. Teams can use tools like flowcharts and swimlane diagrams to clarify roles and responsibilities, reducing confusion and improving efficiency. For example, a marketing team visualized their campaign workflows, which reduced delivery times by 30% and improved coordination.
Lean Six Sigma process mapping also helps resolve bottlenecks that disrupt workflows. By visually representing each step, teams can identify delays and inefficiencies, leading to smoother operations. A tech company, for instance, used SIPOC diagrams to enhance communication between development and customer support teams. This reduced response times for customer issues by 40%, improving overall service quality.
Standardizing processes through mapping further enhances collaboration. A manufacturing company introduced automated quality checks and standardized document requirements, resulting in a 20% reduction in operational costs. These examples highlight how process mapping strengthens teamwork and drives process improvement across departments.
Tip: Teams should regularly update process maps to reflect changes in workflows. This ensures continued alignment and fosters ongoing collaboration.
Supporting Data-Driven Decision-Making
Six Sigma process mapping empowers organizations to make data-driven decisions by providing a clear visual representation of workflows. This structured approach allows systems and teams to identify inefficiencies and areas for improvement with precision. Instead of relying on intuition, decision-makers can use accurate data to guide their strategies and actions.
Process maps highlight the strengths and weaknesses of a workflow. Each step’s contribution becomes visible, enabling teams to pinpoint bottlenecks, redundancies, or defects. For example, a manufacturing team might discover that excessive handoffs between departments slow production. By addressing these inefficiencies, they can streamline operations and improve overall performance.
Organizations also benefit from the ability to analyze processes holistically. Process mapping provides a bird’s-eye view of workflows, making it easier to evaluate how different steps interact. This perspective helps teams identify opportunities for optimization, such as reducing cycle times or reallocating resources. For instance, a healthcare provider used process mapping to analyze patient intake procedures. The insights gained led to a 15% reduction in wait times and improved patient satisfaction.
Data-driven decision-making becomes even more effective when combined with metrics and measurements. Process maps often incorporate key performance indicators (KPIs) like cycle time, defect rates, or resource utilization. These metrics provide a baseline for evaluating performance and tracking improvements over time. Teams can use this data to prioritize high-impact changes and measure the success of their initiatives.
The graphical nature of process maps also enhances communication among stakeholders. Visual tools make complex data more accessible, ensuring that everyone involved understands the process and its challenges. This shared understanding fosters collaboration and alignment, which are critical for implementing successful changes. For example, a logistics company used process mapping to improve warehouse operations. By involving cross-functional teams, they reduced order fulfillment times by 20%.
In today’s competitive landscape, data-driven decision-making is essential for achieving operational excellence. Six Sigma process mapping equips organizations with the tools they need to analyze workflows, eliminate inefficiencies, and drive continuous improvement. Systems and teams that embrace this approach can achieve measurable results and sustain long-term success.
Tip: To maximize the benefits of process mapping, teams should regularly update their maps and integrate real-time data. This ensures that decisions remain aligned with current operational realities.
Advanced Tools and Techniques for Six Sigma Process Mapping in 2025
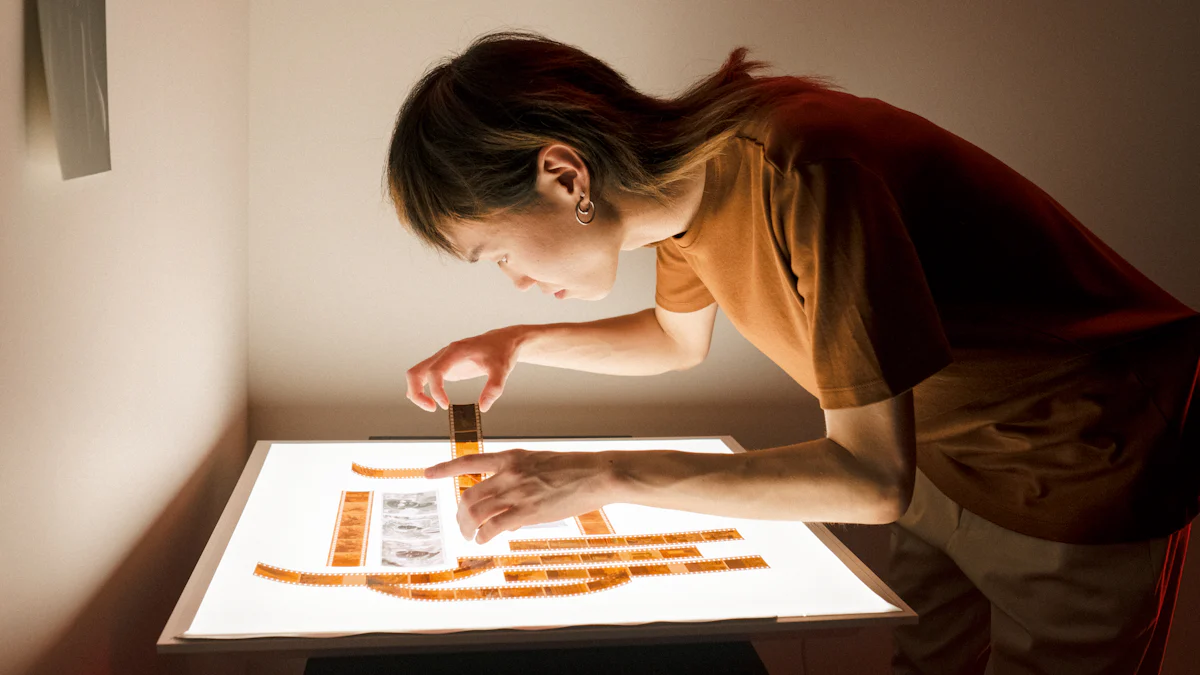
Leveraging Modern Software for Process Mapping
Cloud-Based Tools
Cloud-based tools have become indispensable for Six Sigma process mapping in 2025. These tools enable teams to collaborate in real time, regardless of location, fostering efficiency and inclusivity. Popular platforms like Creately, Lucidchart, and MindMeister offer features tailored to modern business needs.
Software Tool | Features | Notable Users |
---|---|---|
Creately | Visual workspace, no-code tools, BPMN shape libraries, real-time collaboration | Netflix, NASA, Facebook |
Lucidchart | Intelligent diagramming, cloud-based collaboration, integrates with Microsoft 365, Zoom, Slack | N/A |
MindMeister | Collaborative mind mapping, user-friendly design, customization options | N/A |
These tools simplify the creation of process maps by providing intuitive interfaces and pre-built templates. Systems and teams can use them to streamline workflows, reduce inefficiencies, and enhance communication. For example, Creately’s BPMN libraries allow users to standardize process representation, improving clarity and consistency across departments.
AI-Powered Process Analysis
Artificial intelligence (AI) has transformed the way organizations approach process mapping. AI-powered tools enhance traditional Six Sigma methodologies like DMAIC by automating data analysis and providing predictive insights.
AI tools reduce human error and accelerate decision-making.
They streamline processes by identifying inefficiencies and suggesting improvements.
Predictive analytics help teams anticipate potential bottlenecks and address them proactively.
For instance, a standardized process map created with AI tools can reduce variability, leading to a 25% drop in customer complaints and a 15% decrease in product returns. These advancements empower systems and teams to achieve higher levels of efficiency and quality.
Emerging Trends in Process Mapping
Real-Time Process Monitoring
Real-time monitoring has emerged as a game-changer in process mapping. Advanced tools now allow teams to track workflows as they occur, providing immediate insights into performance. This capability helps organizations identify and resolve issues before they escalate. For example, real-time dashboards can highlight delays in approval processes, enabling faster interventions.
Integration with Business Intelligence Platforms
Integrating process mapping tools with business intelligence (BI) platforms has become essential. This integration allows organizations to analyze data from multiple sources, providing a holistic view of operations. BI platforms enhance decision-making by offering detailed reports and analytics. For instance, combining process maps with BI tools can reveal trends in resource utilization, helping teams optimize allocation and reduce costs.
Best Practices for Using Advanced Tools Effectively
To maximize the benefits of advanced tools, systems and teams should follow these best practices:
Alignment with Business Goals: Ensure that process mapping aligns with organizational objectives.
Inclusivity in Design: Engage team members in the mapping process to create practical and user-friendly tools.
Regular Review Cycles: Schedule periodic reviews to assess the effectiveness of process maps and update them as needed.
Focus on Clarity: Keep maps simple and easy to understand by avoiding unnecessary details.
Leverage Technology: Use modern process mapping tools to enhance collaboration and simplify workflows.
Build Process Literacy: Train team members to read and interpret process maps effectively.
By adhering to these practices, organizations can fully leverage the capabilities of modern tools and sustain continuous improvement.
Tip: Regularly update process maps to reflect changes in technology and business objectives. This ensures that systems and teams remain agile and aligned with evolving market demands.
Common Challenges in Six Sigma Process Mapping
Misaligned Stakeholder Expectations
Misaligned stakeholder expectations often create significant obstacles in Six Sigma process mapping. Systems and teams frequently encounter challenges when trying to align diverse perspectives and priorities. Several factors contribute to this issue:
Difficulty in identifying and engaging the right stakeholders.
Varying levels of knowledge and experience among stakeholders.
Conflicting interests and agendas that hinder consensus.
Resource constraints that limit participation or input.
Struggles with effective group decision-making.
Competing priorities that divert attention from process mapping goals.
These challenges can lead to incomplete or inaccurate process maps, reducing their effectiveness. For example, when stakeholders lack a shared understanding of the process, they may overlook critical inefficiencies or fail to agree on improvement strategies. To address this, organizations should prioritize stakeholder engagement early in the process. Clear communication, regular updates, and collaborative workshops can help bridge gaps and align expectations.
Tip: Use stakeholder mapping tools to identify key participants and clarify their roles. This ensures that all relevant voices are heard and considered during the mapping process.
Overcomplicating the Process Map
Overcomplicating process maps is another common challenge. Teams often include excessive details, making the maps difficult to understand and use. This complexity can overwhelm stakeholders and obscure the primary objectives of the mapping exercise. Simplifying process maps requires a strategic approach:
Choose the right level of detail for the audience and purpose. Adjust the level of abstraction based on the map's intended use.
Eliminate unnecessary steps that do not add value or create waste. Techniques like value stream mapping can help identify and remove these steps.
Group related steps that share a common goal or input. Logical organization improves clarity and reduces clutter.
Use clear and consistent labels for all elements in the process map. This enhances readability and ensures stakeholders can easily interpret the map.
Review and refine the process map for accuracy and clarity. Seek feedback from stakeholders to identify areas for improvement.
For instance, a manufacturing team simplified their process map by grouping related tasks and removing redundant steps. This reduced confusion and improved decision-making. By focusing on clarity and relevance, systems and teams can create process maps that are both effective and user-friendly.
Note: Avoid adding unnecessary symbols or colors to process maps. Simplicity ensures that the focus remains on the workflow rather than the design.
Lack of Accurate Data or Information
Accurate data forms the backbone of effective process mapping. Without reliable information, teams risk creating maps that fail to reflect real-world operations. This can lead to flawed analyses and ineffective improvement strategies. Common causes of inaccurate data include outdated documentation, incomplete records, and limited access to key metrics.
To overcome this challenge, systems and teams should adopt a structured approach to data collection:
Conduct interviews with individuals directly involved in the process. Their firsthand insights provide valuable context.
Review existing documentation, such as standard operating procedures or historical process maps.
Use automated tools to gather real-time data, ensuring accuracy and relevance.
Validate collected data by cross-referencing it with multiple sources.
For example, a healthcare organization improved its patient intake process by using real-time data to identify bottlenecks. This approach enabled them to create a more accurate process map, leading to a 15% reduction in wait times. Reliable data ensures that process maps serve as effective tools for identifying inefficiencies and driving improvements.
Tip: Regularly update process maps to reflect changes in workflows or data. This ensures that the maps remain accurate and actionable over time.
Resistance to Change and Adoption
Resistance to change remains one of the most significant challenges when implementing Six Sigma process mapping. Many individuals and teams hesitate to adopt new workflows due to fear of the unknown, lack of understanding, or concerns about increased workload. This reluctance can slow progress and undermine the success of process improvement initiatives. Addressing these concerns requires a proactive and structured approach.
Clear communication plays a vital role in overcoming resistance. Systems and teams must explain the purpose of Six Sigma process mapping and how it benefits the organization. Sharing specific examples, such as reduced cycle times or improved quality, helps stakeholders understand the value of the change. Transparent communication also builds trust, ensuring that everyone feels informed and included.
Comprehensive training is another critical factor. Many employees resist change because they feel unprepared to adapt to new processes. Providing hands-on training sessions and resources equips team members with the skills they need to succeed. For example, interactive workshops can teach employees how to use process mapping tools effectively, boosting their confidence and engagement.
Involving stakeholders in the process fosters collaboration and reduces resistance. When individuals contribute to creating the process map, they feel a sense of ownership and are more likely to support the changes. This approach also allows teams to address concerns early, ensuring that the final process map reflects real-world operations. Stakeholder involvement builds trust and demonstrates that their input matters.
Demonstrating the benefits of change further encourages adoption. Leaders can highlight measurable improvements, such as cost savings or enhanced customer satisfaction, to show the positive impact of Six Sigma process mapping. For instance, a logistics team might showcase how streamlined workflows reduced delivery times by 20%, emphasizing the tangible results of the initiative.
Enhancing credibility strengthens the case for change. Teams can achieve this by involving experienced Six Sigma practitioners or using data-driven insights to support their recommendations. Credible leaders and evidence-based strategies reassure stakeholders that the proposed changes are well-founded and achievable.
Tip: Systems and teams should regularly update stakeholders on progress and celebrate small wins. Recognizing achievements reinforces the value of the change and motivates continued participation.
By addressing resistance through clear communication, training, stakeholder involvement, and demonstrated benefits, organizations can create a smoother transition to Six Sigma process mapping. These strategies ensure that systems and teams remain aligned, engaged, and focused on achieving long-term success.
Actionable Tips for Mastering Six Sigma Process Mapping
Focus on Simplicity and Clarity
Simplicity and clarity form the foundation of effective Six Sigma process mapping. Overcomplicated maps can confuse stakeholders and hinder improvement efforts. Systems and teams should aim to create process maps that are as simple as necessary for their intended audience.
To maintain simplicity and clarity:
Group related steps that share a common goal, input, or output. This organization reduces clutter and enhances readability.
Use clear and consistent labels for steps, inputs, outputs, and decisions. Consistency ensures stakeholders can easily interpret the map.
Regularly review and refine process maps to ensure accuracy and completeness. Refinement helps eliminate unnecessary details and keeps the map relevant.
For example, a manufacturing team streamlined their process map by grouping tasks and using consistent labels. This approach improved understanding and reduced errors during implementation. By focusing on simplicity, systems and teams can create maps that effectively guide decision-making and process improvement.
Tip: Avoid adding excessive symbols or colors. A clean design keeps the focus on the workflow rather than the aesthetics.
Involve Cross-Functional Teams in the Mapping Process
Engaging cross-functional teams in the mapping process brings diverse perspectives to the table. This collaboration ensures a comprehensive understanding of workflows and fosters a culture of shared ownership. Team members from various areas can identify inefficiencies that might otherwise go unnoticed.
Key benefits of involving cross-functional teams include:
Enhanced collaboration through a shared understanding of workflows.
Active participation and idea-sharing, which lead to innovative solutions.
Clearer roles and responsibilities using tools like swimlane diagrams. These diagrams reduce confusion and ensure accountability.
For instance, a logistics company involved their operations, sales, and IT teams in creating a process map for order fulfillment. This collaboration revealed bottlenecks in communication and led to a 15% reduction in delivery times. By involving diverse teams, systems and teams can uncover hidden inefficiencies and drive meaningful improvements.
Tip: Use collaborative tools to engage team members in real time, especially when working across different locations.
Continuously Update and Refine Process Maps
Process maps should evolve alongside organizational changes. Regular updates ensure maps remain accurate and actionable, reflecting current workflows and priorities. Continuous refinement also supports long-term improvement and adaptability.
Benefits of updating and refining process maps include:
Improved operational efficiency by addressing outdated steps.
Enhanced resource utilization through optimized workflows.
Better communication and collaboration among stakeholders.
Support for training and onboarding by providing up-to-date documentation.
Facilitation of continuous process improvement, ensuring sustained success.
For example, a healthcare provider regularly updated their patient intake process map to incorporate new technologies. This practice reduced wait times by 20% and improved patient satisfaction. Systems and teams that prioritize updates can maintain alignment with business goals and adapt to evolving market demands.
Note: Schedule periodic reviews of process maps to identify areas for refinement. This proactive approach ensures maps remain relevant and effective.
Invest in Training and Modern Tools for Process Mapping
Investing in training and modern tools equips systems and teams with the skills and resources needed to excel in Six Sigma process mapping. As workflows grow more complex, organizations must prioritize continuous learning and adopt advanced technologies to stay competitive.
The Importance of Training
Training builds foundational knowledge and enhances process mapping expertise. It ensures that team members understand Six Sigma principles and can apply them effectively. Well-trained individuals can identify inefficiencies, streamline workflows, and drive measurable improvements.
Key benefits of training include:
Skill Development: Employees gain the ability to create accurate and actionable process maps.
Consistency: Training ensures that all team members follow standardized methodologies.
Problem-Solving: Teams learn to analyze workflows and implement data-driven solutions.
Organizations can offer training through workshops, online courses, or certifications. For example, Lean Six Sigma Green Belt programs provide in-depth knowledge of process mapping techniques. These programs also teach participants how to use tools like SIPOC diagrams and value stream maps.
Tip: Encourage employees to pursue certifications to validate their expertise and boost their confidence.
Leveraging Modern Tools
Modern tools simplify process mapping and enhance collaboration. Cloud-based platforms, AI-powered software, and real-time monitoring tools enable teams to create dynamic and interactive maps. These technologies reduce manual effort and provide actionable insights.
Popular tools for process mapping include:
Lucidchart: Offers intuitive diagramming and real-time collaboration.
Creately: Provides BPMN libraries and no-code tools for process visualization.
Minit Process Mining: Uses AI to analyze workflows and identify inefficiencies.
These tools help systems and teams visualize complex processes, track performance, and make data-driven decisions. For instance, AI-powered tools can automatically detect bottlenecks and recommend improvements. This capability saves time and ensures accuracy.
Combining Training and Tools for Success
Training and tools work best when used together. Employees trained in Six Sigma methodologies can maximize the potential of modern tools. They can interpret data, validate process maps, and implement effective changes.
Organizations that invest in both training and tools see significant results. Teams become more efficient, workflows improve, and customer satisfaction increases. For example, a logistics company reduced delivery times by 20% after combining process mapping training with AI-powered analysis tools.
Note: Systems and teams should regularly evaluate their training programs and tools to ensure alignment with organizational goals.
To learn more about how training and tools can transform your process mapping efforts, reach out to us. Our experts can guide you in selecting the right resources and building a roadmap for success.
Mastering Six Sigma process mapping in 2025 remains essential for businesses aiming to stay competitive. This methodology enables systems and teams to identify inefficiencies, reduce waste, and improve workflows. By adopting this approach, organizations can achieve higher quality, better collaboration, and sustained growth.
Modern tools and techniques play a pivotal role in achieving process excellence. Businesses can leverage:
AI-driven automation to predict bottlenecks and enhance customer experiences.
Hyper-automation to streamline multiple functions across departments.
Low-code/no-code platforms to empower non-technical users in process optimization.
To improve process mapping skills and sustain improvements, systems and teams should:
Define the purpose of the process map and analyze current workflows.
Engage stakeholders to gather diverse perspectives.
Regularly update maps to reflect process changes and maintain relevance.
By taking these steps, organizations can optimize operations and drive long-term success. For tailored guidance, reach out to our experts and start transforming your processes today.
FAQ
What is the main purpose of Six Sigma process mapping?
Six Sigma process mapping visually represents workflows to identify inefficiencies, reduce waste, and improve quality. It helps systems and teams streamline operations, enhance collaboration, and achieve measurable improvements in performance.
How does Six Sigma process mapping benefit organizations?
It enables organizations to uncover bottlenecks, eliminate non-value-added activities, and optimize workflows. Systems and teams can use it to improve efficiency, reduce costs, and enhance customer satisfaction.
What tools are recommended for process mapping in 2025?
Modern tools like Lucidchart, Creately, and AI-powered platforms simplify process mapping. These tools offer real-time collaboration, predictive analytics, and customizable templates, helping systems and teams create accurate and actionable maps.
How often should process maps be updated?
Process maps should be updated regularly to reflect changes in workflows, technologies, or business goals. Systems and teams should schedule periodic reviews to ensure maps remain accurate and relevant.
What are common challenges in Six Sigma process mapping?
Challenges include misaligned stakeholder expectations, overcomplicated maps, inaccurate data, and resistance to change. Addressing these issues requires clear communication, stakeholder involvement, and regular refinement of process maps.
How can systems and teams overcome resistance to process mapping?
Clear communication about benefits, hands-on training, and stakeholder involvement can reduce resistance. Demonstrating measurable improvements, such as cost savings or efficiency gains, also encourages adoption.
What metrics should be included in a process map?
Key metrics include cycle time, defect rates, and resource utilization. These metrics help systems and teams evaluate performance, identify inefficiencies, and track improvements over time.
How can organizations learn more about Six Sigma process mapping?
Organizations can reach out to experts for tailored guidance, training, and tool recommendations. Systems and teams can also explore certifications or workshops to deepen their understanding and skills.
Tip: Contact our team for personalized support in mastering Six Sigma process mapping and driving continuous improvement.