How to Use Lean Thinking to Eliminate Waste in 2025
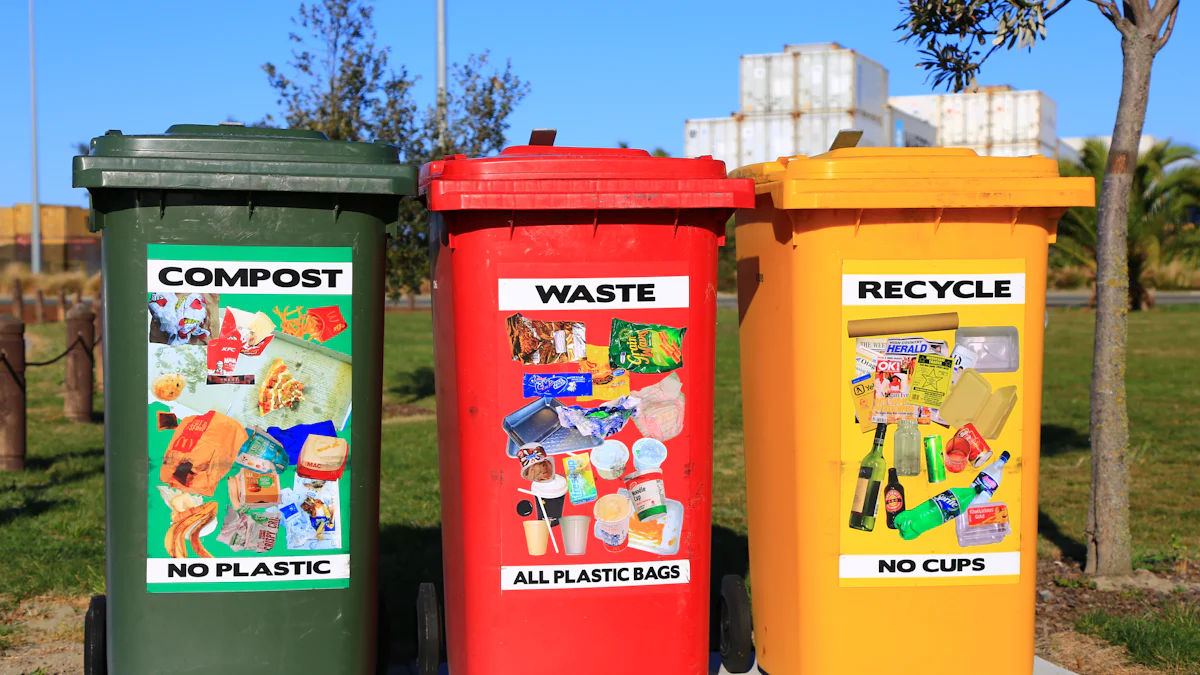
Lean Thinking serves as a strategic approach in Business Management to eliminate waste and improve the flow of processes within systems and teams. By focusing on delivering value to customers, it empowers organizations to streamline operations and enhance efficiency in Sales. In 2025, its importance continues to grow due to mounting economic, environmental, and technological pressures, making Knowledge about Lean Thinking essential for success.
Economic challenges push manufacturers to adopt flexible planning cycles and dynamic pricing models to manage fluctuating costs.
Companies increasingly leverage AI and IoT to optimize processes and diversify product lines.
Environmental concerns drive businesses to reduce resource waste and adopt sustainable practices.
Lean Thinking not only addresses these challenges but also delivers measurable benefits. Studies highlight its ability to increase efficiency, improve employee engagement, and strengthen competitive advantage. By fostering a culture of continuous improvement and enhancing Knowledge, organizations can adapt to evolving market demands and achieve long-term success.
Key Takeaways
Lean Thinking removes waste to improve work and help customers.
Knowing what customers need is important; focus on their real needs.
Mapping steps in work shows waste, helping teams fix processes.
Smooth workflows cut delays and make work faster and better.
Pull systems match making products to what customers want, avoiding extra stock.
Always improve; use the PDCA cycle to make things better over time.
Teaching and involving workers builds a lean mindset and teamwork.
Tools like Value Stream Mapping and Kanban show work steps and improve talks.
The Evolution of Lean Thinking
Origins in Manufacturing: The Toyota Production System
Lean thinking began with the Toyota Production System, a revolutionary methodology developed to maximize efficiency and eliminate waste in manufacturing. Toyota's approach introduced principles like Just-In-Time production and Kaizen, which emphasized continuous improvement and respect for people. These principles allowed Toyota to optimize production lines, enhance quality, and reduce costs. Over time, this system became a benchmark for operational excellence, inspiring organizations worldwide to adopt similar practices.
Lean's purpose is to provide maximum value to customers through the elimination of waste. The cornerstone of Lean is the respect for people and continuous improvement. These principles are applicable across all industries, demonstrating Lean's evolution from its origins in manufacturing to a broader application.
The Toyota Production System laid the foundation for lean thinking, proving that a focus on efficiency and value could transform systems and teams. Its success in manufacturing demonstrated the potential for lean principles to drive innovation and improve outcomes.
Expansion to Other Industries: Healthcare, Software, and Beyond
Lean thinking has transcended its manufacturing roots, finding applications in diverse industries. In healthcare, lean principles streamline patient flow, reduce wait times, and improve outcomes. Service industries use lean to eliminate bottlenecks and boost efficiency. For example:
Healthcare: Enhanced service delivery and patient satisfaction.
Hospitality: Efficient operations leading to improved customer experiences.
Food and Beverage: Targeted cost reductions without compromising quality.
Government: Significant savings through lean practices in projects.
Lean's adaptability has made it a valuable tool for systems and teams across sectors. In construction, it reduces waste and streamlines operations. In software development, it supports agile methodologies by fostering collaboration and iterative improvement. These examples highlight how lean thinking drives transformation and delivers measurable benefits in various contexts.
Adapting Lean Thinking for 2025: Addressing Modern Challenges
Organizations in 2025 face unique challenges that require adaptations to traditional lean principles. Misapplication of lean tools, resistance to change, and a lack of sustained commitment can hinder progress. For example:
Challenge | Description | Mitigation Strategies |
---|---|---|
Misapplication of Lean Principles | Misunderstanding or misusing Lean tools can lead to unintended consequences. | - Education: Train employees thoroughly on Lean concepts. Tailor Lean principles to fit the organization’s unique context. |
Resistance to Change | Employees and leadership may resist altering established processes. | - Communication: Transparently communicate the reasons for Lean adoption and the benefits it brings. Involve employees early on. |
Lack of Sustained Commitment | Lean isn’t a quick fix; it requires ongoing dedication. | - Leadership Buy-In: Ensure leaders champion Lean as a long-term strategy. Regularly assess progress and celebrate achievements. |
Modern systems and teams must also address digital overload, inefficient remote workflows, and resource mismanagement. By integrating advanced technologies like AI and IoT, organizations can enhance lean practices and remain competitive. Tailoring lean principles to fit the unique needs of 2025 ensures that organizations continue to deliver value and eliminate waste effectively.
Core Principles of Lean Thinking
Define Value from the Customer's Perspective
Defining value is the foundation of lean thinking. Systems and teams must understand what the customer considers valuable. This involves identifying the products or services that meet their needs and expectations. Value to the customer is determined by what they are willing to pay for, whether it is a faster delivery time, higher quality, or personalized service. By focusing on this, organizations can eliminate activities that do not contribute to customer satisfaction.
For example, a software development team might prioritize features that enhance user experience rather than adding unnecessary functionalities. This approach ensures that resources are allocated to activities that deliver maximum value to the customer. Defining value also helps align organizational goals with customer expectations, creating a win-win scenario for both parties.
Map the Value Stream to Identify Waste
Mapping the value stream is a critical step in lean thinking. It involves visualizing all the activities required to deliver value to the customer. This process helps identify areas where waste occurs, such as delays, redundant steps, or unnecessary approvals. By analyzing the value stream, systems and teams can pinpoint inefficiencies and focus on eliminating them.
Lean principles categorize waste into eight types, including overproduction, waiting, and defects. For instance, in a manufacturing setup, mapping the value stream might reveal excessive inventory that ties up resources without adding value. In a service industry, it could uncover bottlenecks that slow down customer service. Addressing these issues improves efficiency and ensures a smoother flow of operations.
Teams can use tools like value stream mapping to visualize processes and identify waste. This tool provides a clear picture of how work progresses and highlights areas for improvement. By focusing on the value stream, organizations can streamline operations and enhance overall performance.
Create Flow by Streamlining Processes
Creating flow ensures that processes operate smoothly without interruptions. Once waste is removed from the value stream, systems and teams can focus on maintaining a continuous flow of work. This principle emphasizes reducing delays and ensuring that tasks move seamlessly from one stage to the next.
For example, in a healthcare system, creating flow might involve reorganizing patient intake procedures to minimize waiting times. In a manufacturing environment, it could mean redesigning production lines to eliminate unnecessary movements. The goal is to create a system where work progresses efficiently, delivering value to the customer without delays.
Streamlining processes also involves standardizing workflows and reducing variability. By doing so, teams can maintain consistency and improve predictability. This approach not only enhances productivity but also ensures that customers receive high-quality products or services. Creating flow is a key principle of lean thinking that drives efficiency and customer satisfaction.
Establish Pull Systems to Align with Demand
A pull system ensures that work or production aligns with actual customer demand rather than forecasts. This principle helps systems and teams avoid overproduction, reduce inventory, and respond more effectively to customer needs. By implementing pull systems, organizations can create a lean organization that minimizes waste and maximizes efficiency.
Pull systems operate on the concept of producing or delivering only what the customer requires, exactly when they need it. For example, in a manufacturing setup, a pull system might involve producing components only when the next stage of the process signals a need. In service industries, it could mean processing customer requests as they come in, rather than preemptively completing tasks that may not be necessary.
To establish a pull system, systems and teams can use tools like Kanban boards. These visual management tools help track work progress and ensure that tasks flow smoothly through the value stream. Teams can also implement Just-In-Time (JIT) practices, which focus on delivering the right product or service at the right time. These methods reduce excess inventory and improve responsiveness to customer demands.
A lean mindset is essential for successfully implementing pull systems. Teams must embrace flexibility and adaptability, continuously monitoring demand patterns and adjusting workflows accordingly. By aligning production or service delivery with actual demand, organizations can enhance customer satisfaction and reduce operational inefficiencies.
Pursue Perfection Through Continuous Improvement
Continuous improvement lies at the heart of lean thinking. This principle encourages systems and teams to strive for perfection by consistently identifying and eliminating waste. A lean mindset fosters a culture where every individual seeks opportunities to enhance processes and deliver greater value to customers.
To pursue perfection, organizations can adopt the Plan-Do-Check-Act (PDCA) cycle. This iterative approach involves planning improvements, implementing changes, evaluating results, and refining processes. For example, a lean organization in the healthcare sector might use the PDCA cycle to reduce patient wait times by analyzing bottlenecks and testing new scheduling methods.
Employee engagement plays a critical role in continuous improvement. Teams must feel empowered to suggest changes and experiment with new ideas. Training programs and open communication channels can help build a lean mindset across the organization. Leaders should also recognize and celebrate small wins to maintain momentum and encourage ongoing efforts.
Technology can further support continuous improvement. Tools like data analytics and artificial intelligence enable systems and teams to identify inefficiencies and predict future challenges. By leveraging these technologies, organizations can stay ahead of market demands and maintain a competitive edge.
Pursuing perfection requires commitment and persistence. A lean organization must view improvement as an ongoing journey rather than a one-time goal. By embedding continuous improvement into their culture, systems and teams can achieve sustainable success and deliver exceptional value to their customers.
Types of Waste and How to Identify Them
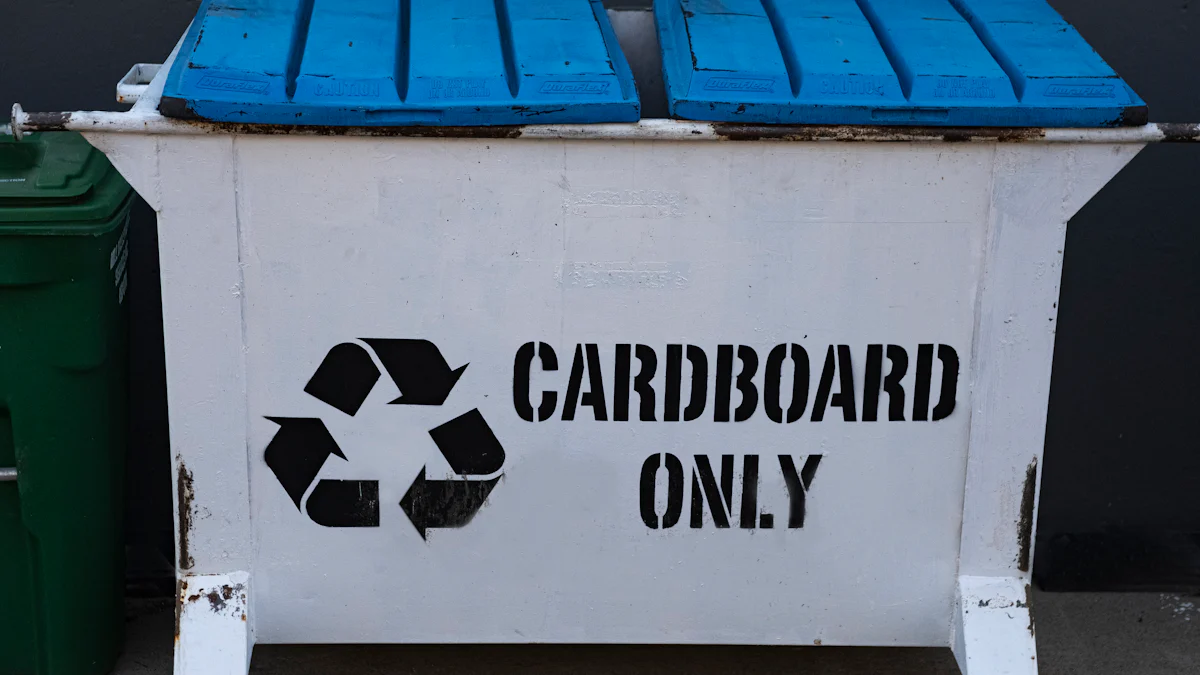
The 8 Wastes of Lean: Overproduction, Waiting, Transport, Overprocessing, Inventory, Motion, Defects, and Unused Talent
Lean thinking identifies eight types of waste that hinder efficiency and reduce value delivery. These wastes include:
Defects: Errors in products or services that require rework or replacement.
Overproduction: Producing more than what is needed, leading to excess inventory.
Waiting: Idle time caused by delays in processes or decision-making.
Non-Utilization of Talent: Failing to leverage employees' skills and expertise.
Transportation: Unnecessary movement of materials or products.
Inventory: Excess stock that ties up resources without adding value.
Motion: Inefficient movements by employees or equipment.
Extra Processing: Performing more work than necessary, such as redundant approvals.
Organizations can identify these wastes by analyzing their processes through tools like Value Stream Mapping (VSM). This tool helps systems and teams separate value-added activities from non-value-added ones, enabling them to optimize processes, reduce costs, and improve product quality.
Tools for Waste Identification: Value Stream Mapping, Gemba Walks, and Root Cause Analysis
Lean six sigma provides several tools to help systems and teams identify and eliminate waste effectively. These tools include:
Value Stream Mapping (VSM): This visual tool maps out all steps in a process, highlighting inefficiencies and areas of waste. It allows teams to design a future state that maximizes value delivery.
Gemba Walks: Leaders and team members observe processes directly on the "shop floor" to identify inefficiencies and gather insights from employees.
Root Cause Analysis: This method digs deep into problems to uncover their underlying causes, ensuring that solutions address the source of waste rather than just the symptoms.
By using these tools, organizations can gain a clearer understanding of their operations and make data-driven decisions to enhance efficiency.
Modern Examples of Waste in 2025: Digital Overload, Inefficient Remote Workflows, and Resource Mismanagement
In 2025, new challenges have emerged that require adaptations to traditional lean principles. Digital overload, for instance, has become a significant source of waste. Employees often face excessive notifications, emails, and digital tools, which disrupt focus and reduce productivity. Systems and teams must streamline digital workflows to minimize this waste.
Inefficient remote workflows also contribute to waste. Poorly designed virtual processes can lead to delays, miscommunication, and duplicated efforts. Organizations must optimize remote work systems by leveraging lean six sigma tools like Kanban boards to improve task management and communication.
Resource mismanagement remains a persistent issue. Overuse of energy, materials, or time can drain resources without adding value. By integrating lean thinking with advanced technologies like IoT, systems and teams can monitor resource usage in real-time and make adjustments to reduce waste.
Addressing these modern examples of waste requires a commitment to continuous improvement and a willingness to adapt lean principles to the unique challenges of the digital age.
A Step-by-Step Framework for Implementing Lean Thinking
Step 1: Assess Current Processes Using Value Stream Mapping
The first step in the framework involves assessing current processes to identify inefficiencies. Systems and teams can use value stream mapping to visualize workflows and pinpoint areas of waste. This tool highlights every step in the process, separating value-added activities from non-value-added ones. For example, a manufacturing team might discover excessive inventory or redundant steps that slow production. In service industries, mapping may reveal bottlenecks in customer service workflows.
To begin, organizations should define their value-driven purpose. This involves asking critical questions such as, "What problem needs solving?" and "What work is required to address it?" Teams must also determine the capabilities and management systems necessary to achieve their goals. By understanding these elements, systems and teams can create a clear roadmap for improvement. Value stream mapping serves as the foundation for implementing lean methodology effectively.
Step 2: Apply the PDCA Cycle (Plan-Do-Check-Act) for Iterative Improvement
The PDCA cycle provides a structured approach to continuous improvement. This iterative process allows systems and teams to test solutions on a small scale, analyze results, and implement successful changes organization-wide. The cycle consists of four stages:
Plan: Identify goals and determine the changes needed to achieve them.
Do: Implement the planned changes on a small scale.
Check: Evaluate the results to measure performance and identify areas for refinement.
Act: Standardize successful changes or restart the cycle to address unresolved issues.
For instance, a healthcare team might use the PDCA cycle to reduce patient wait times. They could plan a new scheduling system, test it in one department, evaluate its impact, and then expand it across the organization. This approach ensures that improvements are data-driven and sustainable. By embracing the PDCA cycle, systems and teams can foster a culture of continuous improvement and adapt to evolving challenges.
Step 3: Engage Teams and Foster a Lean Culture Through Training and Communication
Engaging teams and fostering a lean culture are essential for successful implementation. Training programs enhance employees' understanding of lean principles and methodologies, empowering them to contribute to improvement efforts. Communication plays a vital role in building trust and ensuring alignment with organizational goals.
A lean culture encourages collaboration and knowledge sharing. Employees who understand how their contributions impact the organization are more likely to engage with their work. This engagement boosts morale, reduces turnover, and strengthens teamwork. For example, a company might use workshops to teach employees about lean tools like Kanban boards or the 5S methodology. These tools help teams organize workflows, track progress, and identify bottlenecks.
Organizations that prioritize training and communication create an environment where continuous improvement thrives. Leaders should recognize employees' efforts and celebrate small wins to maintain momentum. By fostering a lean culture, systems and teams can achieve long-term success and deliver exceptional value to customers.
Step 4: Implement Lean Tools Like 5S, Kanban, and Visual Management
Systems and teams can enhance their operations by adopting lean tools such as 5S, Kanban, and visual management. These tools simplify workflows, reduce inefficiencies, and promote a culture of continuous improvement.
The 5S methodology focuses on organizing and maintaining a clean, efficient workspace. It includes five steps: Sort, Set in Order, Shine, Standardize, and Sustain. For example, a manufacturing team might use 5S to declutter workstations, ensuring that only essential tools remain. This approach minimizes wasted motion and improves productivity. Service industries can also benefit by applying 5S to digital environments, organizing files and systems for easier access.
Kanban is another powerful tool that helps systems and teams manage workflows. It uses visual boards to track tasks and ensure smooth progress. Each task moves through stages, such as "To Do," "In Progress," and "Completed." This method prevents bottlenecks and aligns work with demand. For instance, a software development team might use Kanban to prioritize features based on customer needs, ensuring timely delivery.
Visual management enhances communication and transparency. It uses charts, graphs, and other visual aids to display key information. Teams can quickly identify issues and make informed decisions. In a healthcare setting, visual management might involve dashboards showing patient flow or resource availability. This tool ensures that everyone stays informed and aligned with organizational goals.
By implementing these lean tools, systems and teams can streamline processes and improve efficiency. These methods foster collaboration and create a foundation for sustainable success.
Step 5: Measure Progress and Iterate for Continuous Improvement
Measuring progress is essential for sustaining lean practices. Systems and teams must track performance to identify areas for improvement and ensure alignment with goals. Metrics such as cycle time, defect rates, and customer satisfaction provide valuable insights.
Regular assessments help teams evaluate the effectiveness of lean initiatives. For example, a manufacturing team might monitor production times to ensure that changes reduce delays. Service industries can measure response times to improve customer experiences. These evaluations highlight successes and reveal opportunities for further refinement.
Iteration plays a critical role in continuous improvement. Teams should use feedback and data to adjust processes and test new approaches. The Plan-Do-Check-Act (PDCA) cycle supports this iterative process. For instance, a retail team might test a new inventory system, analyze its impact, and refine it based on results. This approach ensures that improvements remain relevant and effective.
Technology can enhance measurement and iteration. Tools like data analytics and IoT provide real-time insights, enabling teams to respond quickly to challenges. By leveraging these technologies, systems and teams can maintain a competitive edge.
Measuring progress and iterating improvements ensure that lean thinking becomes an integral part of organizational culture. Teams that commit to this process can achieve lasting success and deliver exceptional value to customers.
Real-World Example: Lean Thinking in Action
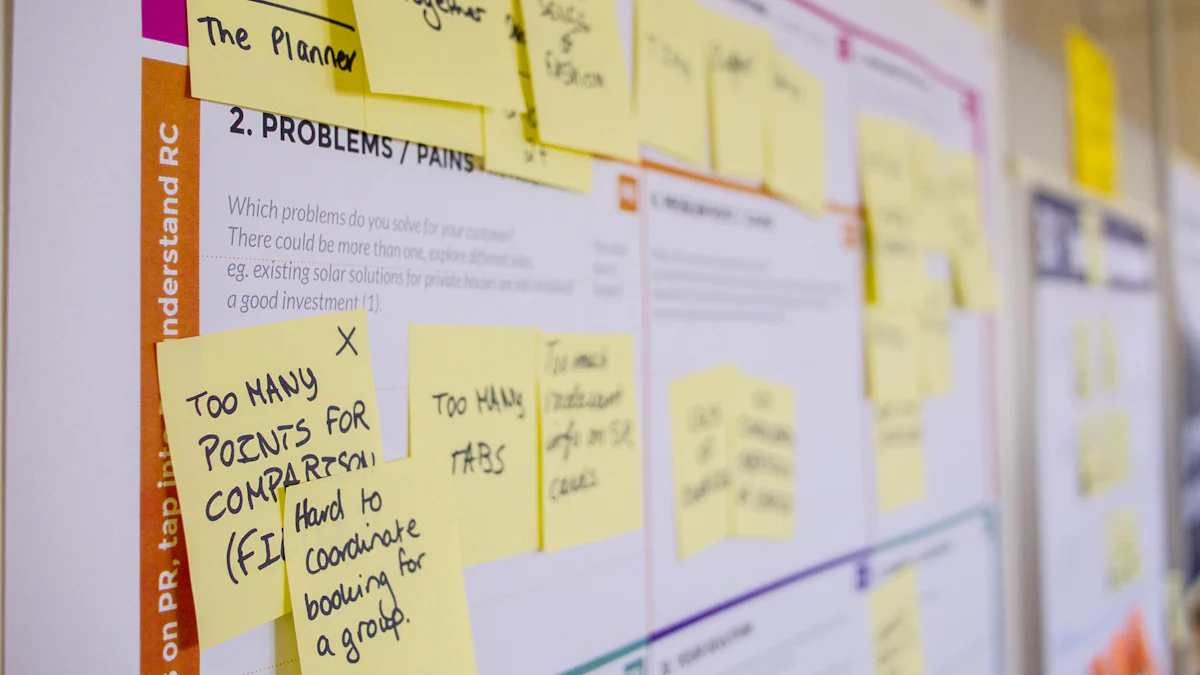
Case Study: Lean Transformation in a Healthcare System
A healthcare system implemented a lean transformation to address inefficiencies and improve patient care. The initiative focused on reducing waiting times, enhancing patient flow, and optimizing resource utilization. Monthly quality reports revealed that long waiting times negatively impacted patient satisfaction, which stood at 62% before the transformation. The system's leadership recognized the need to adopt lean principles to create maximum value for patients.
The transformation began with a thorough assessment of existing processes using value stream mapping. This tool helped systems and teams identify bottlenecks in patient intake and discharge procedures. By eliminating redundant steps and streamlining workflows, the healthcare system reduced waiting times by 40%. For example, reorganizing staff schedules ensured that patients received timely care without unnecessary delays.
The lean initiative also emphasized continuous improvement through the Plan-Do-Check-Act (PDCA) cycle. Teams tested new scheduling methods in one department before expanding them across the organization. This iterative approach allowed the system to refine processes based on real-time feedback. As a result, patient satisfaction increased from 62% to 80%, demonstrating the effectiveness of lean strategies in improving quality outcomes.
Technology played a crucial role in the transformation. The system integrated digital tools to monitor patient flow and resource allocation. Real-time data enabled teams to make informed decisions, further enhancing efficiency. By leveraging lean thinking, the healthcare system not only improved operational performance but also delivered exceptional value to its patients.
Key Takeaways: Improved Patient Flow, Reduced Wait Times, and Enhanced Resource Utilization
This case study highlights several key outcomes of lean transformation in healthcare:
Improved patient flow through streamlined processes and better resource management.
Reduced waiting times by 40%, leading to higher patient satisfaction.
Enhanced resource utilization, ensuring that staff and equipment were used effectively.
Other industries have achieved similar results by adopting lean principles. For instance, Virginia Mason Medical Center reduced patient wait times by 40% and improved satisfaction through patient-centered care. Boeing implemented lean manufacturing and Six Sigma, cutting production time by 30% and defects by 50%. Walmart optimized its supply chain with lean strategies, achieving significant cost savings and agility.
These examples demonstrate the versatility of lean thinking across sectors. Systems and teams that embrace lean principles can achieve measurable improvements in quality and efficiency. Organizations seeking to enhance their operations should consider adopting lean strategies to deliver greater value to their customers.
Overcoming Challenges in Lean Implementation
Common Pitfalls and Failure Modes: Resistance to Change, Lack of Leadership Support, and Misaligned Goals
Organizations often encounter significant obstacles when implementing lean thinking. Resistance to change remains one of the most common challenges. Employees may feel uncertain about new processes or fear that lean practices will disrupt their routines. Leadership opposition can further complicate efforts, especially if leaders fail to see the value of lean transformation. Without their support, teams may struggle to maintain momentum.
Partial adoption across departments also poses a risk. When only select areas embrace lean, inconsistencies arise, leading to inefficiencies. Another common pitfall involves training only a few subject matter experts. High turnover rates can then disrupt lean systems, leaving teams without the necessary knowledge to sustain improvements. Misaligned goals between leadership and teams exacerbate these issues, creating confusion and reducing the effectiveness of lean initiatives.
To overcome these pitfalls, organizations must invest in comprehensive training and ensure that all members, from leadership to frontline employees, understand and commit to lean principles. This approach fosters respect for people and builds a foundation for long-term success.
Strategies to Build Buy-In and Overcome Resistance: Communication, Training, and Quick Wins
Building buy-in for lean transformation requires clear communication and active engagement. Leaders should explain the reasons behind the initiative, emphasizing how it improves efficiency and reduces waste. Employees need to understand the "why," "what," and "how" of lean to feel confident in their roles during the transformation.
Training programs play a crucial role in overcoming resistance. Educating employees about lean benefits and tools, such as value stream mapping, empowers them to contribute to the process. Involving employees at all levels in decision-making fosters ownership and trust. Leaders should also address concerns by providing honest answers and listening to feedback.
Quick wins can help demonstrate the value of lean thinking. For example, teams might implement a small change, such as reorganizing a workspace using the 5S methodology, to show immediate results. Sharing success stories from other departments or organizations further reinforces the benefits of lean practices. These strategies not only build trust but also create momentum for larger transformations.
Sustaining Lean Practices Over Time: Embedding Lean into Organizational Culture and Leadership
Sustaining lean practices requires embedding them into the organization's culture and leadership. Leaders must champion lean philosophy by allocating resources, rewarding achievements, and modeling respect for people. This commitment ensures that lean becomes a mindset rather than a one-time project.
Training and development opportunities keep employees engaged and informed. Regular workshops and refresher courses help teams stay aligned with lean principles. Transparency and trust also play a vital role. Leaders should maintain open communication, sharing progress and challenges to keep employees motivated.
Establishing a robust governance structure supports long-term success. Organizations can monitor key performance indicators and conduct regular project reviews to ensure relevance. Tools like value stream mapping and Kanban boards provide visual insights into processes, helping teams identify areas for improvement.
By fostering a culture of ownership and continuous improvement, organizations can sustain lean practices over time. This approach not only enhances efficiency but also strengthens the organization's ability to adapt to future challenges.
Lean Thinking remains a vital strategy for eliminating waste and delivering value in 2025. Its principles empower systems and teams to optimize processes, enhance customer satisfaction, and foster continuous improvement. Organizations that embrace Lean Thinking can achieve several benefits:
Increased efficiency and productivity through streamlined workflows.
Enhanced customer satisfaction by focusing on their needs.
Improved employee engagement by encouraging ownership and problem-solving.
Stronger competitive advantage through agility and responsiveness.
The Lean journey begins with a commitment to understanding customer value and eliminating inefficiencies. By adopting Lean principles and tools, systems and teams can create sustainable success. Start today and build a culture of continuous improvement to thrive in the evolving market landscape.
FAQ
What is Lean Thinking, and why is it important in 2025?
Lean Thinking is a methodology that eliminates waste and improves efficiency in systems and teams. In 2025, it addresses modern challenges like digital overload and resource mismanagement, helping organizations adapt to economic, environmental, and technological pressures while delivering maximum value to customers.
How can systems and teams identify waste effectively?
Systems and teams can use tools like Value Stream Mapping, Gemba Walks, and Root Cause Analysis. These methods help visualize processes, uncover inefficiencies, and address the root causes of waste. Identifying waste ensures smoother workflows and better resource utilization.
What are the eight types of waste in Lean Thinking?
The eight wastes include defects, overproduction, waiting, non-utilization of talent, transportation, inventory, motion, and extra processing. Each type represents inefficiencies that reduce value delivery. Systems and teams must address these wastes to optimize performance and enhance customer satisfaction.
How does Lean Thinking apply to remote work in 2025?
Lean Thinking improves remote workflows by streamlining communication, reducing delays, and eliminating redundant tasks. Tools like Kanban boards help systems and teams manage tasks visually, ensuring alignment with demand and enhancing productivity in virtual environments.
What role does leadership play in Lean implementation?
Leadership drives Lean success by championing its principles, allocating resources, and fostering a culture of continuous improvement. Leaders must communicate goals clearly, support training initiatives, and recognize team achievements to sustain Lean practices over time.
Can Lean Thinking integrate with advanced technologies?
Yes, Lean Thinking integrates seamlessly with technologies like AI and IoT. These tools provide real-time data, enabling systems and teams to monitor processes, predict inefficiencies, and make informed decisions. Technology enhances Lean practices and ensures adaptability in dynamic markets.
How can organizations sustain Lean practices long-term?
Organizations sustain Lean practices by embedding them into their culture. Regular training, transparent communication, and leadership support ensure continuous improvement. Systems and teams should measure progress, iterate processes, and celebrate small wins to maintain momentum.
Where can systems and teams start their Lean journey?
Systems and teams should begin by defining customer value and mapping their value streams. Identifying inefficiencies and implementing Lean tools like 5S or Kanban creates a strong foundation. For more guidance, reach out to experts who specialize in Lean Thinking strategies.