Lean Thinking in Action How to Achieve Better Results

Lean Thinking serves as a powerful framework for creating value while minimizing waste and resource consumption in business management. By focusing on streamlining processes and eliminating inefficiencies, it enables organizations to achieve remarkable results. For instance:
A telecom infrastructure provider has used Lean methodologies to address workflow disruptions and reduce operational costs in their hiring systems.
A high-end fashion retailer has embraced Lean principles to improve agility and overcome operational inefficiencies in their business management practices.
A rapidly growing tech firm has adopted Lean Enterprise strategies to enhance efficiency amidst rising costs in their hiring systems.
Industries such as healthcare, hospitality, and food and beverage have also reaped significant benefits from Lean Thinking. Healthcare systems, for example, have improved patient care quality and reduced waiting times through Lean Thinking. This approach underscores the importance of continuous improvement and empowers teams to deliver exceptional outcomes in their processes.
Key Takeaways
Lean Thinking helps cut waste and increase value in work.
Knowing what customers need is key to giving good solutions.
Mapping steps in a process shows problems and fixes waste.
Smooth workflows cut delays and make work faster and better.
A pull system matches production to what customers really want.
Small changes, called Kaizen, can lead to big improvements over time.
Teamwork and trust help people share ideas and improve together.
Start small with Lean ideas; fix one thing at a time for success.
Understanding Lean Thinking
What is Lean Thinking?
Lean Thinking is a systematic approach to enhancing efficiency by creating value while minimizing waste. It originated from the Toyota Production System (TPS), which was developed in post-World War II Japan. Key figures like Taiichi Ohno and Shigeo Shingo designed TPS to address resource constraints and improve production efficiency. Over time, this framework evolved into Lean management, which emphasizes continuous improvement and adaptability to changing market demands.
Lean Thinking focuses on identifying what customers truly value and aligning processes to deliver that value effectively. By eliminating non-essential activities, organizations can streamline workflows and achieve better results. This approach has been widely adopted across industries, enabling teams to reduce inefficiencies and foster a culture of improvement.
The Philosophy Behind Lean
The philosophy of Lean Thinking revolves around maximizing value while minimizing waste. Unlike traditional management frameworks, Lean prioritizes customer needs and continuous improvement. It encourages organizations to view their operations as interconnected systems, where every activity contributes to delivering value.
Key aspects of this philosophy include:
Value: Understanding value from the customer’s perspective is the foundation of Lean Thinking.
Respect for People: Empowering teams and respecting their contributions are central to Lean transformation.
Continuous Improvement: Lean fosters a mindset of ongoing enhancement, ensuring that systems adapt to evolving demands.
This philosophy sets Lean apart by emphasizing collaboration, adaptability, and a relentless pursuit of perfection. It transforms not only processes but also the culture within organizations, enabling teams to thrive in dynamic environments.
Key Principles of Lean Thinking
The principles of Lean Thinking provide a structured framework for achieving operational excellence. These principles guide organizations in identifying inefficiencies, improving workflows, and delivering greater value to customers. The five key principles are:
Value: Define value based on the customer’s needs, not the producer’s assumptions.
Value Stream: Map the entire process required to deliver value and identify areas of waste.
Flow: Ensure that value-creating steps proceed smoothly without interruptions or delays.
Pull: Align production with customer demand to avoid overproduction and excess inventory.
Perfection: Strive for continuous improvement by eliminating waste and enhancing processes.
These principles form the backbone of Lean transformation. They help organizations create a seamless flow of activities, reduce inefficiencies, and foster a culture of innovation. By adhering to these principles, teams can achieve sustainable improvements and deliver exceptional results.
Tip: Organizations embarking on a Lean transformation should start by understanding these principles and applying them incrementally. Small, consistent changes can lead to significant long-term benefits.
Core Principles of Lean Thinking
Identifying Value
Identifying value is the cornerstone of lean thinking. Organizations must determine what their customers truly need and prioritize delivering it. Value represents the benefits that customers are willing to pay for, whether it is a product feature, service quality, or timely delivery. By focusing on value, teams can eliminate unnecessary activities that do not contribute to customer satisfaction.
For example, a manufacturing company might identify value as producing high-quality products with minimal defects. In contrast, a healthcare provider may define value as reducing patient wait times while maintaining excellent care standards. Understanding value from the customer’s perspective allows organizations to align their processes with customer expectations, ensuring maximum value delivery.
Mapping the Value Stream
Mapping the value stream involves visualizing the entire process required to deliver value to the customer. This step helps organizations identify inefficiencies and areas of waste within their workflows. A value stream map provides a clear picture of how materials and information flow through the system, highlighting bottlenecks and non-value-adding activities.
A current state map captures the actual flow of materials and information, revealing inefficiencies.
A future state map visualizes the desired improvements in the process.
Identifying choke points allows teams to focus on specific areas that slow down operations.
For instance, a software development team might use value stream mapping to analyze their coding and testing processes. By pinpointing delays in testing, they can implement solutions to improve efficiency and ensure continuous flow. This approach not only enhances productivity but also improves quality by addressing issues at their root.
Creating Flow
Creating flow ensures that value-adding steps proceed smoothly without interruptions or delays. A continuous flow minimizes waste and maximizes efficiency by reducing idle time between tasks. This principle emphasizes the importance of maintaining a steady rhythm in operations, enabling teams to deliver value consistently.
One-piece flow is a key concept in this principle. It involves completing one unit of work at a time, moving it seamlessly through each stage of the process. For example, an assembly line that adopts one-piece flow can reduce waiting times and improve overall efficiency. Similarly, a customer service team can streamline their workflow by addressing one query at a time, ensuring faster resolution and higher quality service.
By creating flow, organizations can achieve a balance between speed and quality. This principle not only enhances operational efficiency but also fosters a culture of continuous improvement, where teams strive to refine their processes and deliver exceptional results.
Establishing a Pull System
A pull system is a cornerstone of lean thinking that aligns production and inventory management with actual customer demand. Unlike traditional push systems, which rely on forecasts to drive production, pull systems ensure that goods are produced only when needed. This approach minimizes waste and enhances operational efficiency.
Did you know? Approximately $163 billion in inventory is wasted globally each year. Pull systems address this issue by reducing overstocking and improving inventory management.
Pull systems offer several benefits:
They enhance efficiency by producing only what is required.
They significantly reduce the risk of overstocking and associated costs.
They adapt to real-time customer demand, ensuring a more responsive supply chain.
For example, in a pull-based supply chain, production and distribution are driven by actual orders rather than speculative forecasts. This ensures that resources are allocated efficiently, and value is delivered to customers without unnecessary delays. Teams implementing pull production often experience smoother workflows and better alignment with customer expectations.
By establishing a pull system, organizations can create a more agile and responsive operation. This principle not only reduces waste but also fosters a culture of continual improvement, where teams consistently refine their processes to meet evolving customer needs.
Continuous Improvement (Kaizen)
Continuous improvement, or Kaizen, is a fundamental principle of lean thinking. It emphasizes small, incremental changes that collectively lead to significant improvements over time. Kaizen encourages teams to identify inefficiencies, analyze root causes, and implement solutions that enhance value delivery.
One notable example of Kaizen in action involved a company struggling with frequent delays in shipping finished products. A cross-functional team conducted a root cause analysis, reviewing shipping records, interviewing staff, and analyzing communication logs. They discovered that machine breakdowns, caused by a lack of preventative maintenance, were the primary issue. By implementing a preventative maintenance schedule and improving interdepartmental communication, the team significantly reduced delays and established a new standard operating procedure.
Kaizen fosters a mindset of continuous improvement by empowering teams to take ownership of their processes. It encourages collaboration and innovation, ensuring that systems remain adaptable to changing demands. Organizations that embrace Kaizen often experience enhanced efficiency, reduced waste, and improved customer satisfaction.
Tip: To successfully implement Kaizen, teams should focus on small, manageable changes rather than attempting large-scale overhauls. This approach builds momentum and ensures sustainable improvement over time.
By integrating Kaizen into their operations, organizations can create a culture of continuous improvement. This not only drives better results but also ensures that teams remain aligned with the principles of lean thinking.
Lean Thinking in Action
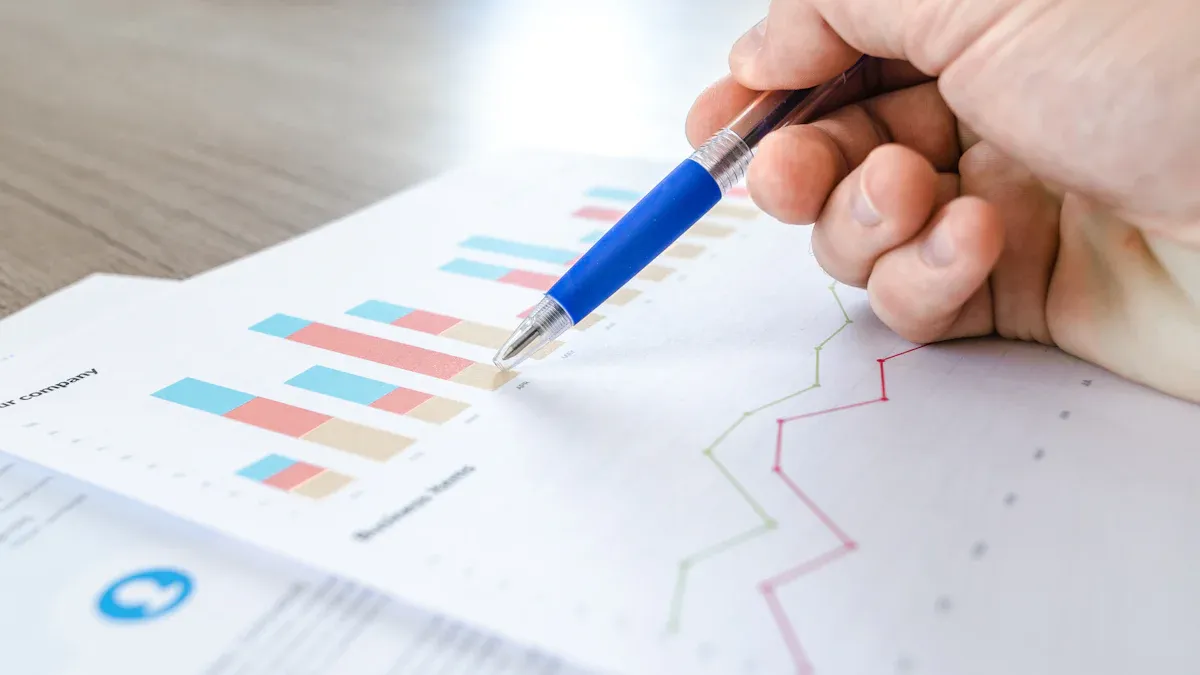
Lean Thinking in Manufacturing
Lean Thinking has revolutionized manufacturing by optimizing processes and reducing waste. Rooted in the Toyota Production System, it emphasizes efficiency and customer value. Many companies have adopted lean methodologies to achieve remarkable results.
Company | Lean Methodology Used | Results Achieved |
---|---|---|
FedEx Express | Milestones in C-check process | Increased C-checks from 14 to 30 per year; reduced man-hours from 32,715 to 21,535. |
Nike | Manufacturing Index, Just-in-Time production | Reduced waste and improved consistency across 800 factories. |
Harley-Davidson | Total Productive Maintenance, 5S, JIT | Improved productivity, reduced transportation expenses, and maintained optimal inventory levels. |
John Deere | Automated quality control mechanisms | Enhanced defect detection and increased product output. |
Kimberly-Clark | Automation of transportation management system | Freed up analysts for proactive work and streamlined processes. |
Intel | Lean techniques for quality control | Boosted productivity while maintaining high product quality. |
Ford Motor Company | Kaizen, Six Sigma, Total Quality Management | Improved product quality, reduced costs, and minimized waste. |
These examples demonstrate how lean principles, such as Just-in-Time production and Kaizen, help systems and teams achieve operational excellence. By focusing on customer value and eliminating inefficiencies, manufacturing organizations can enhance productivity and maintain high-quality standards.
Lean Thinking in Healthcare
Healthcare systems have embraced lean thinking to improve efficiency and patient outcomes. By eliminating wasteful processes and focusing on priority areas, teams can deliver better care. Lean methodologies have enabled healthcare providers to manage demand effectively and enhance patient satisfaction.
Lean Thinking has helped healthcare systems eliminate wasteful processes.
It has enabled better management of demand.
Focus on priority areas has led to significant improvements in patient care.
The NHS has experienced reduced waiting times and faster treatment.
Overall quality of care and patient satisfaction have increased.
For example, hospitals using lean principles have streamlined patient flow, reduced waiting times, and improved treatment accuracy. Teams that adopt lean methodologies can focus on delivering customer value, ensuring that patients receive timely and effective care. This approach not only enhances operational efficiency but also fosters a culture of continuous improvement in healthcare.
Lean Thinking in Software Development
Lean Thinking has significantly influenced software development, particularly through Agile methodologies. Teams apply lean principles to optimize workflows, eliminate waste, and deliver customer value efficiently.
Specify value from the user’s point of view. Value is defined as what the customer is willing to pay for.
Map the value stream. Analyze and improve the delivery process by spotting bottlenecks.
Create flow. Optimize the internal process of delivery to deliver features quickly.
Establish pull. Work on initiatives only when customer need is established.
Seek perfection. Repeat the process to define the best possible value without waste.
By integrating these principles, software development teams can enhance collaboration, reduce delays, and deliver high-quality products. For instance, mapping the value stream helps identify bottlenecks in coding and testing, while creating flow ensures seamless progress. Teams that embrace lean thinking can adapt to changing customer needs and maintain a competitive edge in the fast-paced tech industry.
Lean Thinking in Daily Life
Lean Thinking extends beyond industries and organizations; it can transform daily life by improving personal productivity and reducing waste. Applying its principles helps individuals streamline their routines, focus on value-adding activities, and achieve better results in their personal and professional lives.
One effective way to integrate Lean Thinking into daily life is through Value Stream Mapping. This involves identifying and documenting activities that hold value, such as time management, health, and well-being. By analyzing daily routines, individuals can pinpoint tasks that contribute to their goals and eliminate those that do not. For example, someone aiming to improve their fitness might prioritize regular exercise while reducing time spent on unproductive activities like excessive screen time.
Visual Management tools also play a crucial role in applying Lean Thinking principles. Tools like vision boards or Kanban boards provide a clear visual representation of tasks and progress. A Kanban board, for instance, organizes tasks into categories such as "To Do," "In Progress," and "Completed." This system helps individuals stay organized, track their progress, and maintain focus on their priorities. Visual tools not only enhance clarity but also foster a sense of accomplishment as tasks move toward completion.
Another key principle is Continuous Improvement, which encourages regular evaluation and adjustment of personal processes. Individuals can periodically review their routines to identify inefficiencies and implement small changes for better outcomes. For instance, someone struggling with morning productivity might experiment with preparing for the day the night before. Over time, these incremental adjustments lead to significant improvements in efficiency and effectiveness.
Tip: Start small when applying Lean Thinking to daily life. Focus on one area, such as time management, and gradually expand to other aspects. Consistency is key to achieving lasting results.
By adopting Lean Thinking in daily life, individuals can create systems that align with their goals and values. These systems enable them to reduce waste, enhance productivity, and maintain a balanced lifestyle. Whether through mapping value streams, using visual tools, or embracing continuous improvement, Lean Thinking empowers people to achieve more with less effort.
Steps to Implement Lean Thinking
Assess Current Processes
The first step in implementing lean thinking involves assessing current processes to identify inefficiencies and areas for improvement. Organizations must gain a solid understanding of lean principles before diving into process improvement. This foundational knowledge helps teams recognize opportunities for change and align their efforts with lean methodologies.
A thorough assessment begins with a current state analysis. Teams should examine workflows, identify pain points, and pinpoint bottlenecks that hinder efficiency. For example, redundant steps in a workflow or poorly designed layouts can slow down operations. By mapping out these processes, organizations can visualize inefficiencies and prioritize areas for improvement.
Tip: Conducting a current state assessment provides a clear picture of existing challenges. This step lays the groundwork for targeted improvements that align with lean principles.
Identify and Eliminate Waste
Eliminating waste is a core aspect of lean thinking. Waste refers to any activity that does not add value to the customer. Identifying and addressing these inefficiencies can significantly enhance operational efficiency and reduce costs.
Common types of waste include defects, unnecessary transportation, waiting, and excessive motion. For instance, defects result in wasted time and materials, while poor workstation layouts can lead to unnecessary movement within a work center. Teams should analyze their processes to uncover these inefficiencies and implement solutions to address them.
Defects: Time and resources spent on correcting errors.
Transportation: Unnecessary movement of inventory or people.
Waiting: Idle time for resources or customers.
Motion: Inefficient movements within a workspace.
For example, a manufacturing team might redesign their production layout to minimize transportation waste, while a customer service team could streamline workflows to reduce waiting times. These targeted actions help organizations align their processes with lean principles, ensuring value delivery without unnecessary delays.
Engage and Empower Teams
Engaging and empowering teams is essential for successful lean implementation. Employees play a critical role in identifying inefficiencies and driving improvements. Organizations should foster a culture where team members feel valued and encouraged to contribute ideas.
Empowerment begins with education. Teams should receive training on lean principles and methodologies to understand their role in the improvement process. Cross-training employees to perform multiple tasks can also enhance flexibility and reduce bottlenecks. For example, a cross-functional team with diverse skills can tackle complex problems more effectively.
Callout: Empowered teams drive innovation and sustain continuous improvement. Encouraging collaboration and providing necessary support ensures long-term success.
Organizations should also establish mechanisms for employees to propose changes and seek leadership support. This collaborative approach not only enhances engagement but also ensures that improvements align with organizational goals. By involving employees at all levels, organizations can create a culture of continuous improvement that drives sustainable success.
Monitor and Continuously Improve
Monitoring progress and fostering continuous improvement are vital components of Lean Thinking. Systems and teams must consistently evaluate their performance to ensure alignment with Lean principles. This ongoing assessment helps identify areas for refinement and maintain momentum toward achieving operational excellence.
Organizations can utilize various tools and metrics to track their progress effectively. Continuous improvement indicators play a crucial role in assessing performance. Metrics such as safety, cost, product quality, overall equipment efficiency (OEE), time savings, customer satisfaction, return on investment (ROI), and employee satisfaction provide valuable insights. Dashboards offer a visual representation of these key performance indicators, enabling real-time tracking and trend analysis. For instance, a manufacturing team might use dashboards to monitor OEE and identify bottlenecks in their production process.
Digital tools like UTrakk further enhance the monitoring process. UTrakk, a Daily Management System, supports structured continuous improvement efforts. It features digital Gemba Walks, which allow teams to observe workflows directly and identify inefficiencies. Additionally, its dashboards facilitate quick problem identification and action tracking. These tools empower teams to address issues promptly and maintain a steady focus on improvement.
Regular reviews and feedback loops are essential for sustaining progress. Teams should schedule periodic evaluations to analyze their performance metrics and identify opportunities for enhancement. For example, a healthcare team might review patient satisfaction scores and adjust their workflows to reduce waiting times. These reviews encourage a proactive approach to problem-solving and ensure that improvements align with organizational goals.
Collaboration among team members also drives continuous improvement. Engaging employees at all levels fosters a sense of ownership and accountability. Cross-functional teams can brainstorm solutions, share insights, and implement changes effectively. This collaborative environment not only enhances problem-solving but also strengthens team cohesion.
Tip: Establishing a culture of transparency and open communication ensures that all team members remain informed and aligned with improvement objectives.
By leveraging tools, metrics, and collaborative strategies, organizations can monitor their progress and sustain continuous improvement. This approach enables systems and teams to adapt to evolving demands, deliver consistent value, and achieve long-term success.
Fostering a Lean Culture
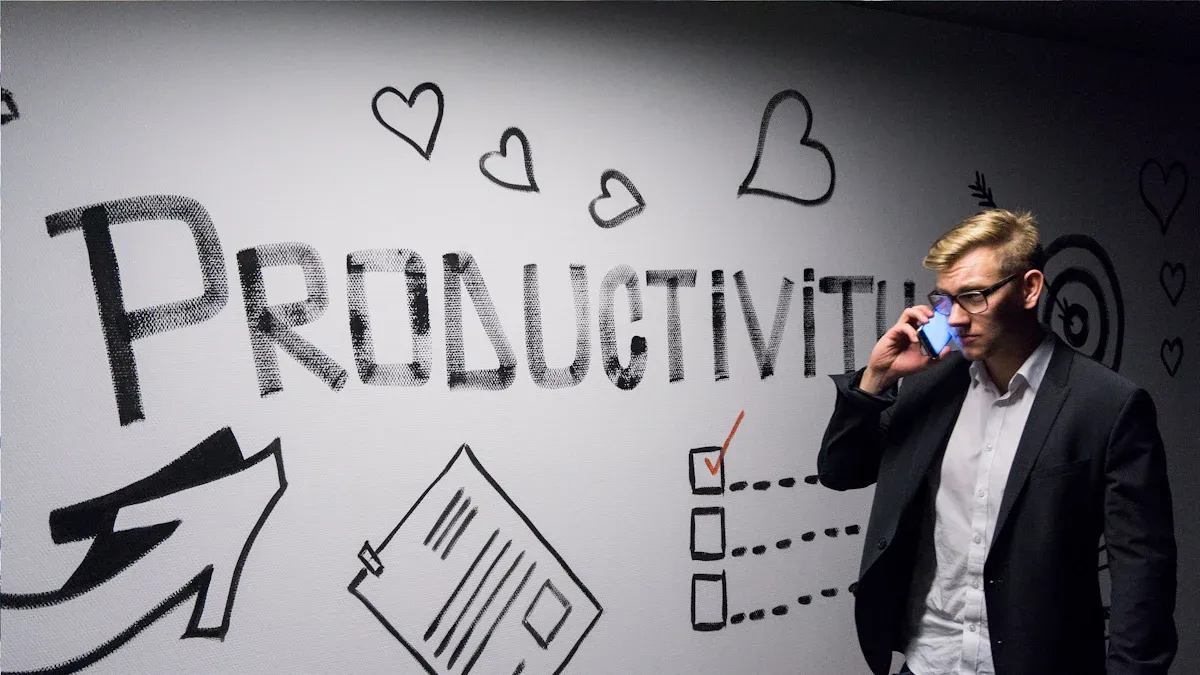
Leadership’s Role in Lean Thinking
Leadership plays a pivotal role in establishing and sustaining a lean culture. Effective leaders act as role models, demonstrating commitment to lean principles and fostering an environment of continuous improvement. Their actions set the tone for the entire organization, ensuring alignment with lean thinking.
Lean leadership emphasizes respect for people and their contributions.
Leaders guide teams by example, actively participating in process improvements.
They adopt a coaching mindset, empowering employees to solve problems and enhance workflows.
Note: CEOs and Presidents must fully embrace their role as the "exemplar" lean leader to build a lasting lean culture. By engaging directly in processes, leaders inspire teams to adopt lean practices and maintain focus on delivering value.
Leadership also involves creating a shared vision that prioritizes customer focus and operational excellence. By aligning organizational goals with lean management principles, leaders ensure that systems and teams remain dedicated to eliminating waste and maximizing value delivery.
Respect for People and Team Empowerment
Respect for people forms the foundation of a lean culture. Organizations that prioritize dignity and empowerment create an environment where employees feel valued and motivated to contribute. This approach fosters collaboration and innovation, driving sustainable improvement.
To promote respect and empowerment, lean leaders should:
Investigate root causes to address issues effectively.
Align individual goals with organizational objectives.
Lean thinking extends beyond tools and techniques; it represents a cultural transformation. Shared beliefs and behaviors that emphasize respect and continuous improvement enable teams to thrive. Organizations can further support this transformation by:
Providing training and development opportunities.
Encouraging open communication and collaborative problem-solving.
Recognizing and rewarding employee contributions.
Ensuring a safe and ergonomic work environment.
For example, empowering employees to identify and eliminate waste not only enhances efficiency but also strengthens their sense of ownership. This alignment between individual and organizational goals creates a cohesive culture that drives long-term success.
Building a Mindset of Continuous Improvement
A mindset of continuous improvement is essential for sustaining a lean culture. This mindset encourages teams to seek opportunities for growth and refinement, ensuring that processes remain adaptable to changing demands.
Practical strategies for fostering this mindset include:
Kanban Boards: Visualize tasks and workflows to identify bottlenecks and enhance collaboration.
Streamlined Meetings: Keep meetings brief and focused to improve productivity.
Decentralization: Empower team members to make decisions, fostering accountability and innovation.
Enhanced Communication: Maintain clear communication to reduce misunderstandings.
Cultural Integration: Embed continuous improvement into the organization's values and practices.
For instance, a team using Kanban boards can track progress visually, ensuring transparency and efficiency. Similarly, decentralizing decision-making empowers employees to take initiative, driving innovation and problem-solving. These practices not only enhance operational performance but also reinforce a culture of growth and adaptability.
By integrating these strategies, organizations can cultivate a lean culture that prioritizes value delivery and continuous improvement. This cultural shift enables systems and teams to achieve better results while maintaining alignment with lean principles.
Overcoming Challenges in Lean Thinking
Resistance to Change
Resistance to change often emerges as a significant obstacle when implementing lean thinking. Employees and stakeholders may hesitate to adopt new practices due to uncertainty or fear of the unknown. Addressing this resistance requires clear communication and proactive engagement.
Organizations should begin by articulating the vision and benefits of lean thinking. Explaining how it enhances efficiency and reduces waste helps stakeholders understand its value. Misconceptions or fears about lean principles must also be addressed to build trust and confidence. For example, some employees may believe that lean thinking leads to job cuts, while in reality, it focuses on optimizing processes and empowering teams.
Involving employees in the transformation process fosters a sense of ownership. Cross-functional teams can collaborate to identify inefficiencies and propose solutions. Providing training and coaching equips individuals with the skills needed to adapt to new workflows. Recognizing and rewarding achievements further motivates teams and reinforces positive behavior.
Visual management tools, such as dashboards or kaizen events, can monitor progress and highlight successes. Celebrating milestones and learning from setbacks encourages continuous improvement and reduces resistance over time. By addressing emotional responses and gathering feedback, organizations can create an environment where change feels less daunting and more achievable.
Misunderstanding Lean Principles
Misunderstanding lean principles can hinder effective implementation. Many individuals mistakenly view lean as a set of tools rather than a comprehensive philosophy. This misconception often leads to superficial changes that fail to deliver lasting results.
Educating teams about the core principles of lean is essential. For instance, lean thinking prioritizes creating value for customers while minimizing waste. It requires a deep understanding of interconnected systems and a commitment to continuous improvement. Organizations must emphasize that lean is not just about techniques but also about fostering a culture of collaboration and adaptability.
Another common misconception is that lean experts should possess complete knowledge of every aspect of the field. In reality, lean thinking encompasses diverse areas, and no single individual can master them all. Encouraging teams to focus on learning and applying principles rather than striving for perfection ensures a more practical approach.
Organizations should also be cautious about relying on inaccurate resources. Many online articles misrepresent lean principles, leading to confusion. Teams should seek guidance from credible sources and experienced practitioners to ensure proper implementation. By clarifying these misconceptions, systems and teams can align their efforts with the true essence of lean thinking.
Sustaining Long-Term Commitment
Sustaining long-term commitment to lean thinking requires persistence and strategic planning. Organizations must treat lean as an ongoing journey rather than a one-time initiative. Leadership plays a crucial role in maintaining focus and allocating resources to support continuous improvement.
Leaders should begin by conducting a thorough assessment of current processes. This evaluation helps identify inefficiencies and sets the stage for defining a future state vision. Clear goals and a comprehensive implementation plan provide direction and ensure alignment with organizational objectives.
Piloting lean initiatives in targeted areas allows teams to test strategies and refine their approach. Extensive training and coaching prepare employees to embrace new practices. Measuring progress through key performance indicators highlights successes and identifies areas for improvement. Celebrating achievements reinforces commitment and motivates teams to sustain their efforts.
Adaptability is key to long-term success. Organizations must remain flexible and open to change as they encounter new challenges. Regular reviews and feedback loops enable systems and teams to refine their processes and maintain alignment with lean principles. By fostering a culture of continuous improvement, organizations can achieve lasting results and thrive in dynamic environments.
Lean Thinking offers a transformative approach to achieving operational excellence. Its principles—value, value stream, flow, pull, and perfection—guide systems and teams to eliminate waste and deliver customer-focused results. Real-world examples, such as Toyota’s production efficiency and Starbucks’ service consistency, highlight its practical impact. Starting small, like mapping a single process, allows teams to build momentum and confidence. By embracing Lean as a cultural shift, organizations can empower their teams, foster continuous improvement, and achieve sustainable success. The journey begins with one step—aligning processes with Lean principles to create lasting value.
FAQ
What is the main goal of lean thinking?
Lean thinking aims to maximize value while minimizing waste. It helps systems and teams streamline processes, improve efficiency, and focus on delivering what customers truly need. This approach fosters continuous improvement and ensures better results across various industries.
How does lean thinking benefit organizations?
Lean thinking benefits organizations by reducing inefficiencies, enhancing productivity, and improving customer satisfaction. Systems and teams can achieve operational excellence by identifying waste, creating flow, and aligning processes with customer demands. These improvements lead to sustainable growth and competitive advantages.
Can lean thinking be applied outside of manufacturing?
Yes, lean thinking applies to many fields, including healthcare, software development, and daily life. Systems and teams in these areas use its principles to optimize workflows, eliminate waste, and deliver value. Its adaptability makes it a powerful tool for diverse industries.
What are the key principles of lean thinking?
The key principles include identifying value, mapping the value stream, creating flow, establishing a pull system, and pursuing continuous improvement. These principles guide systems and teams in eliminating waste and delivering value efficiently.
How can teams start implementing lean thinking?
Teams can start by assessing current processes, identifying inefficiencies, and eliminating waste. Engaging employees, providing training, and fostering a culture of continuous improvement are essential steps. Starting small and building momentum ensures sustainable success.
What challenges might arise when adopting lean thinking?
Common challenges include resistance to change, misunderstanding lean principles, and sustaining long-term commitment. Addressing these issues requires clear communication, proper training, and leadership support. Systems and teams must remain adaptable and focused on continuous improvement.
How does lean thinking promote continuous improvement?
Lean thinking encourages systems and teams to regularly evaluate processes, identify inefficiencies, and implement small, incremental changes. This approach fosters a culture of innovation and adaptability, ensuring that workflows remain efficient and aligned with customer needs.
Where can readers learn more about lean thinking?
Readers interested in learning more about lean thinking can explore additional resources or reach out to experts. Systems and teams seeking guidance can contact us for tailored support and insights into implementing lean principles effectively.