Mastering Process Improvement: Key Methodologies Explained
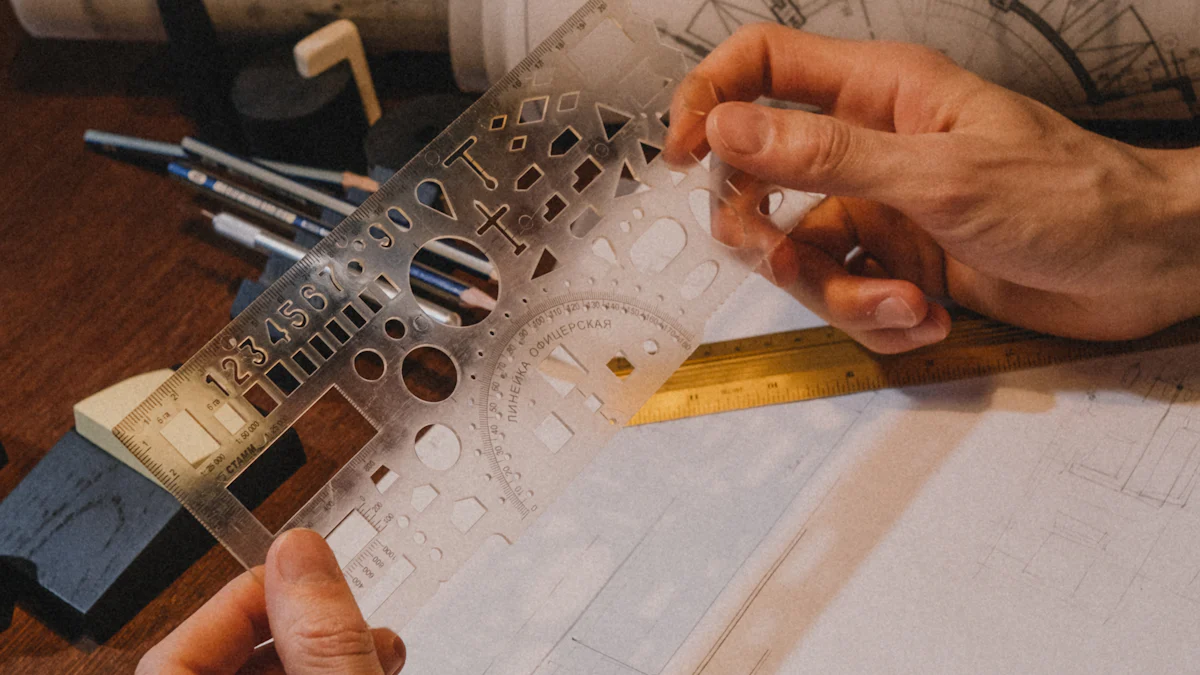
Process improvement methodologies serve as structured approaches to enhance business processes, aiming to boost efficiency and effectiveness. This methodology for process improvement, including Lean and Six Sigma, plays a pivotal role in business success. They help organizations increase productivity, improve product quality, and enhance customer satisfaction. Companies that actively engage employees in these initiatives often see a 14% increase in productivity and a 19% boost in employee satisfaction. Mastering these methodologies equips businesses with the agility and adaptability needed to thrive in today's competitive marketplace. For more insights, systems and teams can reach out to us for tailored resources and guidance.
Key Takeaways
Understanding process improvement methodologies like Lean, Six Sigma, and Agile is essential for enhancing business efficiency and effectiveness.
Engaging employees in process improvement initiatives can lead to significant boosts in productivity and job satisfaction.
Implementing Lean principles helps organizations maximize value by minimizing waste, leading to improved product quality and customer satisfaction.
Six Sigma's data-driven approach focuses on reducing defects and variability, ensuring consistent quality and enhanced customer experiences.
Adopting Agile methodologies fosters flexibility and collaboration, allowing teams to quickly adapt to changes and deliver high-quality results.
Total Quality Management (TQM) emphasizes continuous improvement and employee involvement, driving higher customer satisfaction and operational efficiency.
Businesses should carefully select the right process improvement methodology that aligns with their specific needs and goals for optimal results.
Understanding Process Improvement Methodologies
Definition and Purpose
Process improvement methodologies provide structured approaches to enhance business processes. They aim to evaluate existing workflows, identify inefficiencies, and optimize operations. By doing so, organizations can achieve greater efficiency, reduce costs, and deliver superior customer outcomes. These methodologies, such as Six Sigma, Lean, and Agile, guide teams in modeling current processes, setting improvement targets, and implementing prioritized ideas. This systematic approach ensures that businesses continuously refine their operations to meet evolving demands.
Importance in Business Contexts
In today's competitive market, understanding process improvement methodologies is crucial for business success. These methodologies help organizations eliminate inefficiencies, improve productivity, and enhance quality. By fostering transparency and accountability, they lead to better customer experiences and higher profitability. Businesses that adopt these methodologies can adapt to changing needs and streamline workflows. For instance, systems and teams that implement these strategies often see significant improvements in operational efficiency and customer satisfaction. Companies looking to explore these methodologies further can reach out to us for expert guidance and tailored resources.
Lean Process Improvement
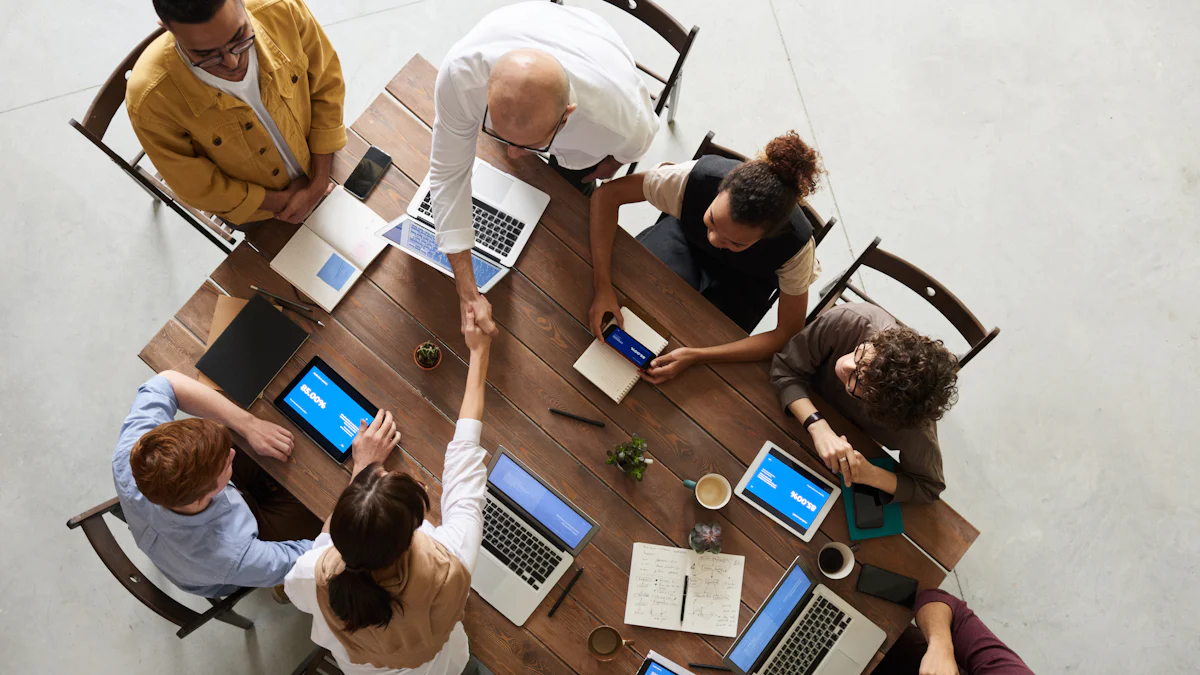
Lean process improvement stands as a cornerstone in the realm of process improvement methodologies. This approach focuses on maximizing value while minimizing waste, ensuring that every step in a process contributes to the final product's value. By adopting lean principles, organizations can streamline operations and enhance efficiency.
Principles of Lean
Lean principles revolve around creating more value for customers with fewer resources. The core idea is to eliminate waste and ensure that every action adds value. Lean methodology emphasizes understanding customer needs and aligning processes to meet those needs efficiently. It encourages continuous improvement and empowers employees to identify and solve problems. Henry Ford famously implemented lean concepts, setting up a highly productive organization that transformed raw materials into finished cars efficiently.
Benefits of Lean
The benefits of lean process improvement are manifold. Organizations that implement lean can expect increased efficiency and reduced costs. By eliminating waste, they can focus on activities that add value, leading to improved product quality and customer satisfaction. Lean also fosters a culture of continuous improvement, where employees actively seek ways to enhance processes. This approach not only boosts productivity but also enhances employee morale and engagement.
Applying Lean in Business
Applying lean in business involves a strategic approach to process improvement. Companies start by mapping out their current processes to identify areas of waste. They then implement changes to streamline operations and enhance value delivery. Toyota's implementation of Kaizen principles exemplifies this, revolutionizing the automotive industry by empowering employees to continuously improve manufacturing processes. Systems and teams that embrace lean often see significant improvements in operational efficiency and customer satisfaction. For businesses eager to explore lean process improvement further, reaching out to us can provide tailored resources and expert guidance.
Six Sigma Methodology
Six Sigma stands as a prominent process improvement methodology, renowned for its data-driven approach to enhancing process quality. This methodology aims to identify and eliminate defects and variability, striving for near-perfection with a goal of no more than 3.4 defects per million opportunities. By focusing on statistical analysis, Six Sigma helps organizations achieve consistency and customer satisfaction.
Principles of Six Sigma
The principles of Six Sigma revolve around reducing process variation and improving quality. It employs a structured approach known as DMAIC, which stands for Define, Measure, Analyze, Improve, and Control. This framework guides teams through identifying problems, measuring current performance, analyzing root causes, implementing improvements, and controlling future process performance. By adhering to these principles, organizations can ensure that their processes consistently deliver high value to customers.
Benefits of Six Sigma
Implementing Six Sigma offers numerous benefits. Organizations can expect improved process efficiency and reduced costs. By minimizing defects, they enhance product quality and customer satisfaction. Six Sigma also fosters a culture of continuous improvement, where employees use data to drive decision-making. In healthcare, for instance, Lean Six Sigma has successfully reduced surgical complications in repetitive procedures, demonstrating its effectiveness in improving quality of care and reducing costs.
Applying Six Sigma in Business
Applying Six Sigma in business involves a commitment to data-driven decision-making. Companies begin by defining their process goals and collecting relevant data. They then analyze this data to identify areas for improvement. For example, manufacturing industries often use Six Sigma to optimize for consistency and customer satisfaction. Systems and teams that embrace Six Sigma can achieve significant improvements in operational efficiency and product quality. Businesses eager to explore Six Sigma further can reach out to us for tailored resources and expert guidance.
Agile Methodology for Process Improvement
Agile methodology has revolutionized how organizations approach process improvement. This methodology emphasizes flexibility, collaboration, and customer-centricity. Agile allows teams to adapt quickly to changes and deliver high-quality results. By focusing on iterative development, Agile helps organizations improve processes and respond to evolving customer needs.
Principles of Agile
Agile principles prioritize individuals and interactions over processes and tools. Teams work closely with stakeholders to understand their needs and deliver valuable solutions. Agile encourages continuous improvement through regular feedback and reflection. Teams use frameworks like Scrum and Kanban to manage work efficiently. These frameworks help teams break down complex projects into manageable tasks, ensuring steady progress and timely delivery.
Benefits of Agile
Agile offers numerous benefits for organizations seeking to enhance their processes. It fosters a culture of collaboration and transparency, leading to better communication and teamwork. Agile's iterative approach allows teams to identify and address issues early, reducing risks and improving quality. Organizations that adopt Agile often see faster project delivery and increased customer satisfaction. For example, systems and teams that implement Agile methodologies report a 15% increase in project delivery speed, enhancing their competitive edge.
Applying Agile in Business
Applying Agile in business involves embracing a mindset of flexibility and adaptability. Teams start by defining clear goals and priorities, then work in short cycles to deliver incremental improvements. Regular meetings, such as daily stand-ups and sprint reviews, keep everyone aligned and focused. Agile empowers teams to make decisions and take ownership of their work, leading to higher engagement and productivity. Businesses looking to explore Agile further can reach out to us for tailored resources and expert guidance.
Total Quality Management (TQM)
Total Quality Management (TQM) stands as a comprehensive approach to improving business processes. This methodology emphasizes continuous improvement, customer satisfaction, and full-team involvement. TQM encourages organizations to focus on quality in every aspect of their operations, ensuring that they deliver maximum value to customers.
Principles of TQM
The principles of TQM revolve around several key concepts:
Customer Focus: Organizations prioritize understanding and meeting customer needs. They strive to exceed customer expectations by delivering high-quality products and services.
Continuous Improvement: TQM promotes an ongoing effort to enhance processes. Teams regularly assess their workflows, identify areas for improvement, and implement changes to increase efficiency and effectiveness.
Employee Involvement: Every team member plays a crucial role in the quality improvement process. TQM fosters a culture where employees feel empowered to contribute ideas and take ownership of their work.
Data-Driven Decision Making: Organizations use data to guide their decisions. By analyzing performance metrics, they can identify trends, measure success, and make informed choices about process improvements.
Benefits of TQM
Implementing TQM offers numerous benefits to organizations:
Enhanced Customer Satisfaction: By focusing on quality and customer needs, businesses can improve their products and services, leading to higher customer satisfaction and loyalty.
Increased Efficiency: Continuous improvement efforts help organizations streamline their processes, reducing waste and increasing productivity.
Improved Employee Morale: When employees actively participate in the improvement process, they feel valued and engaged, leading to higher job satisfaction and morale.
Competitive Advantage: Organizations that consistently deliver high-quality products and services can differentiate themselves from competitors, gaining a competitive edge in the market.
Applying TQM in Business
Applying TQM in business involves several steps:
Commitment from Leadership: Successful TQM implementation requires strong support from top management. Leaders must demonstrate their commitment to quality and set clear goals for the organization.
Training and Development: Employees need training to understand TQM principles and tools. This equips them with the skills necessary to contribute to the improvement process.
Process Evaluation: Teams assess their current processes to identify areas for improvement. They gather data, analyze performance, and set targets for enhancement.
Implementation of Changes: Organizations implement changes to improve processes and increase value delivery. They monitor progress and adjust strategies as needed to achieve desired outcomes.
Systems and teams that embrace TQM often see significant improvements in operational efficiency and customer satisfaction. Businesses eager to explore TQM further can reach out to us for tailored resources and expert guidance.
Kaizen and Continuous Improvement
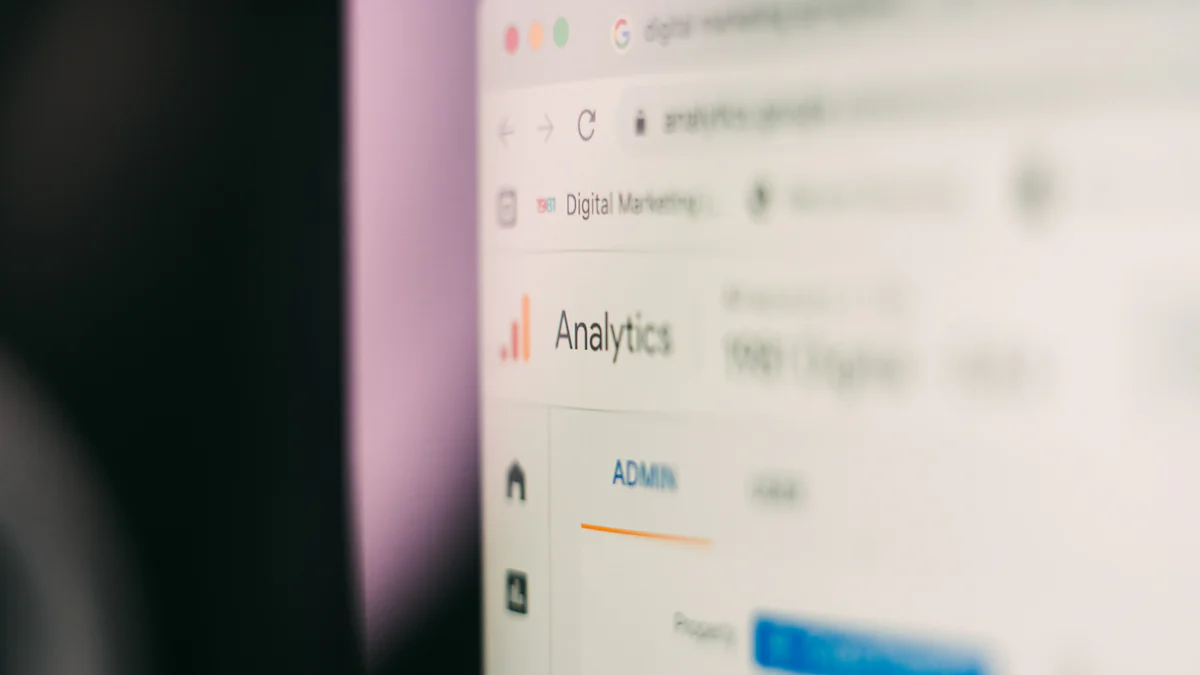
Kaizen, a Japanese term meaning "change for better," embodies the philosophy of continuous improvement. This approach encourages organizations to make small, incremental changes to processes, enhancing efficiency and value over time. Kaizen has become a cornerstone in various industries, driving significant improvements in both quality and productivity.
Principles of Kaizen
Kaizen principles focus on involving all employees in the improvement process. Everyone, from top management to frontline workers, contributes ideas for enhancing operations. This inclusive approach fosters a culture of collaboration and innovation. Kaizen emphasizes the importance of identifying waste and streamlining processes to maximize value. By continuously evaluating and refining workflows, organizations can adapt to changing demands and maintain a competitive edge.
Benefits of Kaizen
The benefits of Kaizen are evident across multiple sectors. In the automotive industry, Toyota famously implemented Kaizen principles to revolutionize its manufacturing processes. This led to increased efficiency and reduced waste, setting a benchmark for lean methodology. In healthcare, hospitals have adopted Kaizen to improve patient care and reduce errors. For instance, Virginia Mason Medical Center in Seattle used Kaizen to cut patient wait times and enhance overall patient experiences. These examples highlight how Kaizen-driven organizations achieve remarkable improvements in operational efficiency and customer satisfaction.
Applying Kaizen in Business
Applying Kaizen in business involves a commitment to ongoing improvement. Organizations start by assessing their current processes to identify areas for enhancement. Employees at all levels participate in brainstorming sessions to generate ideas for change. These ideas are then tested and implemented, with results monitored to ensure effectiveness. A bank in Japan successfully reduced customer wait times by 90% through Kaizen practices, demonstrating the potential impact of this approach. Systems and teams that embrace Kaizen often see significant improvements in efficiency and value delivery. Businesses eager to explore Kaizen further can reach out to us for tailored resources and expert guidance.
Business Process Reengineering (BPR)
Business Process Reengineering (BPR) represents a radical approach to process improvement. This methodology involves the fundamental rethinking and redesign of business processes to achieve dramatic improvements in critical performance measures such as cost, quality, service, and speed. BPR aims to help organizations maintain a competitive advantage by transforming their operations to deliver maximum value.
Principles of BPR
The principles of BPR focus on several key areas:
Radical Redesign: BPR requires a complete overhaul of existing processes. It challenges the status quo by questioning the assumptions underlying current workflows. This principle encourages organizations to think creatively and explore new ways of delivering value.
Process Orientation: BPR emphasizes understanding and optimizing entire processes rather than individual tasks. By taking a holistic view, organizations can identify inefficiencies and streamline operations to enhance value delivery.
Cross-Functional Teams: Successful BPR implementation relies on collaboration across different departments. Cross-functional teams bring diverse perspectives and expertise, enabling organizations to design innovative solutions that address complex challenges.
Technology Integration: Information technology plays a crucial role in BPR. Advanced technologies enable organizations to automate processes, improve data management, and enhance communication. By leveraging IT capabilities, businesses can achieve significant improvements in efficiency and effectiveness.
Benefits of BPR
Implementing BPR offers numerous benefits:
Enhanced Efficiency: By redesigning processes, organizations can eliminate redundancies and reduce cycle times. This leads to increased productivity and cost savings.
Improved Quality: BPR focuses on delivering high-quality outcomes by optimizing processes. Organizations can enhance product and service quality, leading to greater customer satisfaction.
Increased Flexibility: BPR enables organizations to adapt quickly to changing market conditions. By streamlining processes, businesses can respond more effectively to customer needs and emerging opportunities.
Competitive Advantage: Organizations that successfully implement BPR can differentiate themselves from competitors. By delivering superior value, they can gain a competitive edge in the marketplace.
Applying BPR in Business
Applying BPR in business involves several steps:
Identify Processes for Reengineering: Organizations begin by identifying processes that require improvement. They assess current workflows to pinpoint areas of inefficiency and potential value enhancement.
Assemble Cross-Functional Teams: Cross-functional teams collaborate to redesign processes. They bring together diverse skills and perspectives to develop innovative solutions.
Leverage Technology: Organizations integrate advanced technologies to support process redesign. IT capabilities enable automation, data analysis, and improved communication.
Implement Changes: Businesses implement redesigned processes and monitor their impact. They track performance metrics to ensure that changes deliver the desired value.
Systems and teams that embrace BPR often see significant improvements in operational efficiency and customer satisfaction. Businesses eager to explore BPR further can reach out to us for tailored resources and expert guidance.
Comparing Process Improvement Methodologies
Organizations often face the challenge of selecting the most suitable process improvement methodology to enhance their operations. Each methodology offers unique benefits and focuses on different aspects of process enhancement. Understanding these differences is crucial for making informed decisions that align with organizational goals.
Choosing the Right Methodology
Selecting the right methodology requires a thorough understanding of the organization's specific needs and objectives. Businesses must consider factors such as the nature of their processes, the desired outcomes, and the resources available. For instance, Lean focuses on eliminating waste and maximizing value, making it ideal for organizations aiming to streamline operations. On the other hand, Six Sigma emphasizes reducing variability and defects, which suits industries where precision and quality are paramount.
Organizations should also evaluate their current process maturity and the level of change they are willing to undertake. Business Process Reengineering (BPR) involves radical redesign, suitable for companies ready for significant transformation. In contrast, Kaizen promotes continuous, incremental improvements, making it a better fit for businesses seeking gradual enhancements.
Consulting firms like The Hackett Group can provide valuable insights and support in choosing the right methodology. They offer expertise and objectivity, helping organizations leverage best practices and learn from top-performing companies. Engaging with such firms can bring a fresh perspective and ensure that the chosen methodology aligns with industry standards and organizational goals.
Hybrid Approaches
In some cases, a single methodology may not fully address an organization's needs. Hybrid approaches, which combine elements from multiple methodologies, can offer a more comprehensive solution. For example, integrating Lean and Six Sigma can provide a balanced focus on efficiency and quality. This combination, known as Lean Six Sigma, allows organizations to streamline processes while maintaining high standards of quality.
Hybrid approaches also enable organizations to tailor process improvement strategies to their unique contexts. By blending methodologies, businesses can address specific challenges and capitalize on the strengths of each approach. For instance, combining Agile with Total Quality Management (TQM) can enhance flexibility and customer focus while ensuring continuous quality improvement.
Companies like Centric Consulting specialize in helping organizations implement hybrid approaches. They offer tools and techniques from various methodologies, enabling businesses to optimize operations across the enterprise. By focusing on continuous improvement, organizations can drive competitive advantage and achieve sustainable success.
In summary, mastering various process improvement techniques like Lean, Six Sigma, Agile, TQM, Kaizen, and BPR can significantly enhance business operations. Each methodology offers unique benefits, helping organizations identify potential areas for improvement and implement improvements effectively. Continuous process improvement remains crucial for maintaining competitiveness. Businesses should carefully select the right methodology that aligns with their specific needs. Systems and teams that embrace these strategies often see increased productivity and employee satisfaction. For tailored guidance, organizations can reach out to us to identify potential solutions and optimize their processes.
FAQ
What are the most common process improvement methodologies?
Organizations often use several methodologies to enhance their processes. The most common ones include Lean, Six Sigma, Process Reengineering, Agile, Total Quality Management (TQM), and Kaizen. Each methodology offers unique strategies to identify inefficiencies and implement improvements.
How do these methodologies benefit businesses?
These methodologies help businesses streamline operations, reduce costs, and improve product quality. By adopting these approaches, organizations can enhance customer satisfaction and gain a competitive edge. Systems and teams that implement these strategies often see significant improvements in productivity and efficiency.
Can businesses use more than one methodology?
Yes, businesses can adopt hybrid approaches by combining elements from different methodologies. For example, integrating Lean and Six Sigma can provide a balanced focus on efficiency and quality. This flexibility allows organizations to tailor their process improvement strategies to their specific needs.
How do organizations choose the right methodology?
Choosing the right methodology depends on the organization's goals, resources, and process maturity. Businesses should consider factors such as the nature of their processes and desired outcomes. Consulting firms can offer valuable insights and support in selecting the most suitable approach.
What role does technology play in process improvement?
Technology plays a crucial role in process improvement by enabling automation, data analysis, and enhanced communication. Organizations can leverage advanced technologies to streamline operations and achieve significant improvements in efficiency and effectiveness.
How do these methodologies ensure continuous improvement?
Methodologies like Kaizen and TQM emphasize continuous improvement by encouraging regular assessments and refinements. Organizations that adopt these approaches foster a culture of ongoing enhancement, ensuring they adapt to changing demands and maintain a competitive edge.
Are there specific industries that benefit more from these methodologies?
While all industries can benefit from process improvement methodologies, sectors like manufacturing, healthcare, and technology often see significant gains. These methodologies help address industry-specific challenges, such as reducing defects in manufacturing or improving patient care in healthcare.
How can businesses measure the success of process improvement initiatives?
Businesses can measure success by setting clear improvement targets and tracking performance against these goals. Regular assessments and data analysis help organizations evaluate the effectiveness of implemented changes and ensure results are sustained.
What is the role of employees in process improvement?
Employees play a vital role in process improvement by contributing ideas and taking ownership of their work. Methodologies like Kaizen and TQM emphasize employee involvement, fostering a culture of collaboration and innovation.
How can businesses learn more about implementing these methodologies?
Businesses interested in exploring these methodologies further can reach out to systems and teams for tailored resources and expert guidance. Engaging with experienced consultants can provide valuable insights and support in optimizing processes and achieving sustainable success.