Six Sigma Methodology: Your Path to Success
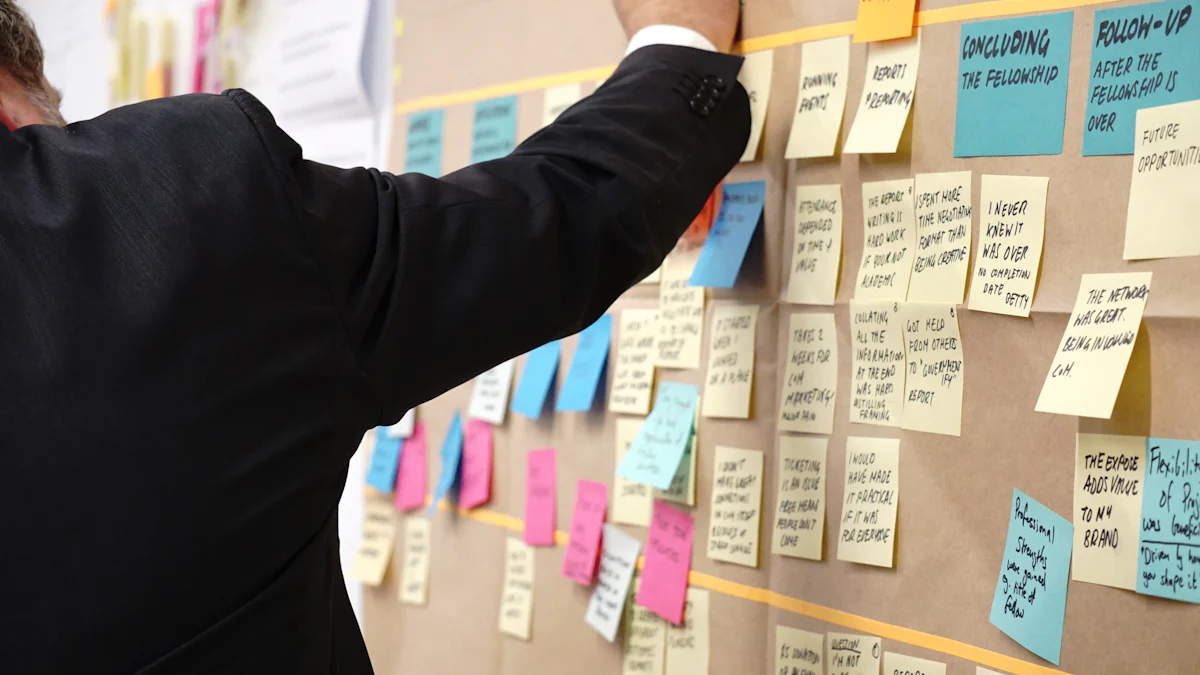
Six Sigma stands as a powerful tool in the realm of Business Management. It focuses on improving processes and reducing defects. Originating from Motorola, this methodology has transformed industries by enhancing efficiency and quality. The six sigma methodology provides a structured approach to problem-solving, making it a path to success for many organizations. By integrating Knowledge and data-driven strategies, companies can refine their Hiring Systems and operational processes. Systems and teams that embrace Six Sigma often see remarkable improvements. For those eager to learn more, reaching out to experts can provide invaluable insights.
Key Takeaways
Six Sigma is a data-driven methodology that enhances business processes by reducing defects and improving quality.
Understanding key concepts like DMAIC and DMADV is essential for effective implementation of Six Sigma.
Focusing on customer requirements ensures that products and services align with client expectations, leading to increased satisfaction.
Data-driven decision-making minimizes guesswork and helps teams identify root causes of issues, leading to more effective solutions.
Continuous improvement is a core principle of Six Sigma, encouraging teams to regularly analyze processes and make necessary adjustments.
Investing in training and certification equips teams with the skills needed to successfully implement Six Sigma practices.
Overcoming challenges such as resistance to change and data collection issues is crucial for the successful adoption of Six Sigma.
Understanding Six Sigma
Definition and Origin
Six Sigma represents a disciplined, data-driven approach aimed at improving business processes. It seeks to eliminate defects and ensure quality. Motorola introduced this methodology in the 1980s. They aimed to enhance their manufacturing processes by reducing variability and defects. Over time, Six Sigma gained popularity across various industries. Companies recognized its potential to improve efficiency and quality.
Key Concepts and Terminology
Six Sigma revolves around several key concepts and terms. Understanding these is crucial for anyone looking to implement the methodology effectively:
Defects: Any instance where a product or service fails to meet customer expectations.
Process Variation: Differences in process performance that can lead to defects.
DMAIC: A structured problem-solving process consisting of five phases: Define, Measure, Analyze, Improve, and Control.
DMADV: Another process used primarily for designing new processes or products, consisting of Define, Measure, Analyze, Design, and Verify.
Sigma Level: A metric that indicates the capability of a process to produce defect-free work.
Systems and teams that adopt Six Sigma often see significant improvements in their operations. They focus on reducing defects and enhancing quality. This leads to increased customer satisfaction and operational efficiency. For those eager to delve deeper into Six Sigma, reaching out to experts can provide invaluable insights and guidance.
Core Principles of Six Sigma
Focus on Customer Requirements
Six Sigma places a strong emphasis on understanding and meeting customer needs. Systems and teams prioritize customer satisfaction by identifying what clients truly value. They gather feedback and analyze data to ensure that products and services align with customer expectations. This focus on customer requirements drives quality management and enhances the overall experience for clients. By consistently delivering what customers want, organizations build trust and loyalty.
Data-Driven Decision Making
In Six Sigma, decisions rely heavily on data and statistical analysis. Teams use statistical quality control to identify patterns and trends within processes. This approach minimizes guesswork and ensures that decisions are based on factual evidence. By employing root cause analysis, they pinpoint the underlying issues affecting quality. This methodical approach leads to more accurate solutions and prevents recurring problems. Lean Six Sigma further enhances this by integrating lean principles, which streamline processes and eliminate waste.
Process Improvement and Variation Reduction
Process improvement lies at the heart of Six Sigma methodology. Teams aim to reduce variation in processes to achieve consistent and high-quality outcomes. By applying statistical quality control, they identify areas where processes deviate from the desired standard. Continuous improvement becomes a core practice as systems and teams strive to refine their operations. Lean Six Sigma complements this by focusing on efficiency and waste reduction. The result is a streamlined process that delivers superior quality and performance.
The DMAIC Process
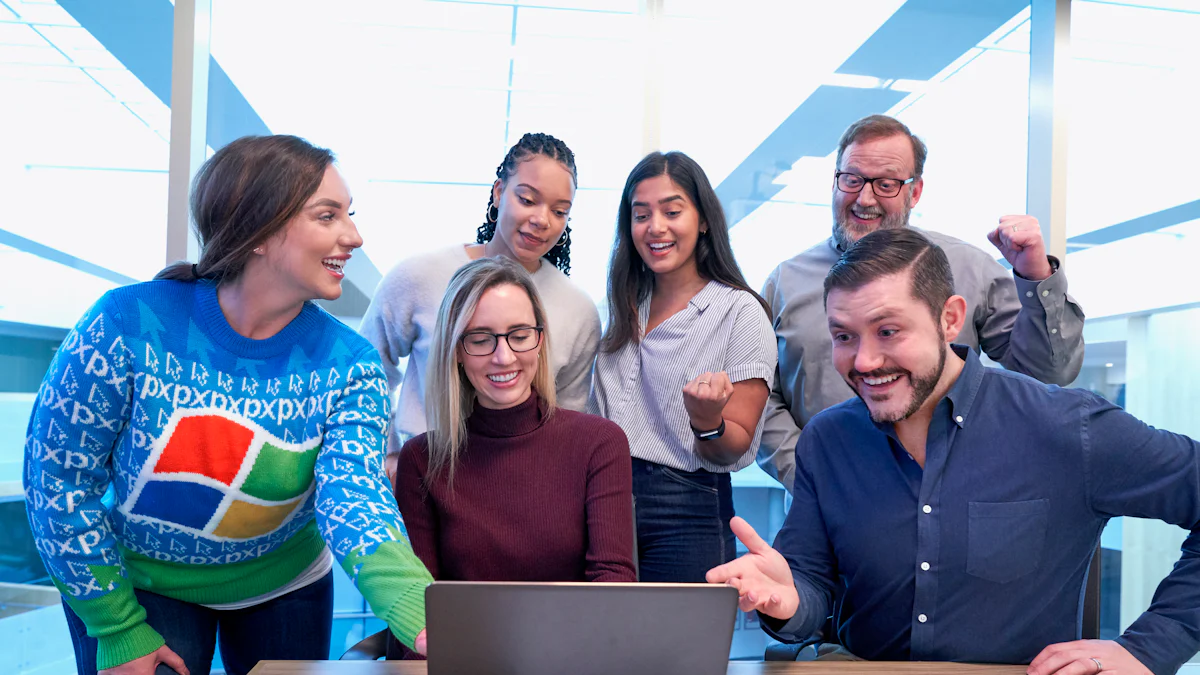
The DMAIC process forms the backbone of Six Sigma methodology. It provides a structured framework for tackling complex problems and driving process improvement. Each phase of DMAIC serves a specific purpose, guiding systems and teams toward achieving optimal results.
Define Phase
In the Define Phase, systems and teams identify the problem or opportunity for improvement. They clearly outline the project goals and scope. This phase involves understanding customer needs and expectations. Teams gather input from stakeholders to ensure alignment with business objectives. By defining the problem accurately, they set a solid foundation for the subsequent phases.
Measure Phase
The Measure Phase focuses on collecting data to understand the current state of the process. Systems and teams establish key performance indicators (KPIs) to quantify the problem. They use various tools to gather accurate and reliable data. This phase helps in identifying the extent of the issue and provides a baseline for comparison. Accurate measurement is crucial for effective analysis and decision-making.
Analyze Phase
During the Analyze Phase, systems and teams delve into the data to uncover root causes of the problem. They employ statistical analysis to identify patterns and correlations. This phase involves brainstorming and hypothesis testing to pinpoint the factors contributing to defects or inefficiencies. By understanding the root causes, teams can develop targeted solutions that address the core issues.
Improve Phase
In the Improve Phase, systems and teams focus on developing and implementing solutions to address the root causes identified in the Analyze Phase. They brainstorm potential improvements and select the most effective strategies. Teams use pilot testing to evaluate the impact of these solutions on the process. This phase emphasizes creativity and innovation, encouraging systems and teams to think outside the box. By refining processes, they aim to enhance efficiency and quality. Successful implementation of improvements leads to significant gains in performance and customer satisfaction. Systems and teams that embrace this phase often see remarkable transformations in their operations.
Control Phase
The Control Phase ensures that the improvements made during the Improve Phase are sustained over time. Systems and teams establish control mechanisms to monitor the process and maintain the gains achieved. They implement standard operating procedures and use control charts to track performance. This phase involves regular audits and reviews to ensure compliance with the new standards. By maintaining control, systems and teams prevent the recurrence of defects and inefficiencies. Continuous monitoring allows for quick identification and correction of any deviations. The Control Phase solidifies the success of the DMAIC process, ensuring long-term benefits for organizations.
The DMADV Process
The DMADV process, a vital component of Six Sigma, focuses on designing new processes or products with precision and quality. Systems and teams employ this methodology to ensure that new developments meet customer expectations and business objectives. Each phase of DMADV plays a crucial role in achieving these goals.
Define Phase
In the Define Phase, systems and teams establish clear objectives for the new process or product. They identify customer needs and expectations, ensuring alignment with business goals. This phase involves gathering input from stakeholders to create a comprehensive project charter. By defining the scope and objectives, systems and teams lay the groundwork for successful project execution.
Measure Phase
During the Measure Phase, systems and teams collect data to understand customer requirements and process capabilities. They establish key metrics to evaluate the performance of the new design. This phase involves benchmarking against industry standards and gathering insights from existing processes. Accurate measurement provides a solid foundation for informed decision-making in subsequent phases.
Analyze Phase
In the Analyze Phase, systems and teams delve into the data to identify potential design options. They use statistical analysis to evaluate different approaches and select the most viable solutions. This phase involves brainstorming and testing hypotheses to ensure that the chosen design meets customer needs. By analyzing data thoroughly, systems and teams can develop innovative solutions that enhance quality and efficiency.
Design Phase
In the Design Phase of the DMADV process, systems and teams focus on creating detailed plans for new processes or products. They translate customer requirements into specific design features. This phase involves developing prototypes and models to visualize the final outcome. Systems and teams use tools like computer-aided design (CAD) software to refine their concepts. They ensure that the design aligns with customer expectations and business objectives. By meticulously planning each aspect, they lay the groundwork for a successful implementation.
Systems and teams conduct design reviews to evaluate the feasibility and effectiveness of their plans. They gather feedback from stakeholders to make necessary adjustments. This collaborative approach ensures that the design meets all requirements and standards. Systems and teams prioritize quality and efficiency in their designs, aiming to deliver superior products or services. By focusing on precision and attention to detail, they create solutions that stand out in the market.
Verify Phase
The Verify Phase serves as the final step in the DMADV process. Systems and teams test the new design to ensure it meets all specifications and performs as intended. They conduct pilot runs and simulations to validate the design's effectiveness. This phase involves rigorous testing to identify any potential issues or areas for improvement. Systems and teams use statistical analysis to verify that the design achieves the desired outcomes.
During the Verify Phase, systems and teams gather data to assess the design's performance. They compare the results against predefined metrics to ensure compliance with quality standards. This phase emphasizes accuracy and reliability, ensuring that the final product or process delivers consistent results. Systems and teams document their findings and make any necessary adjustments to optimize performance.
By completing the Verify Phase, systems and teams confirm that the new design is ready for full-scale implementation. They ensure that it aligns with customer needs and business goals. This thorough verification process guarantees that the final product or process meets the highest standards of quality and efficiency. Systems and teams that follow the DMADV methodology achieve remarkable success in delivering innovative solutions.
Benefits of Implementing Six Sigma
Enhanced Quality and Efficiency
Six Sigma significantly enhances quality and efficiency in business operations. Systems and teams that adopt this quality control methodology focus on reducing the defect rate in their processes. They employ statistical tools to identify areas for quality improvement. By doing so, they ensure that products and services consistently meet high standards. This approach leads to a noticeable increase in operational efficiency. Teams streamline their processes, eliminating unnecessary steps and reducing waste. Lean Six Sigma principles further support this by integrating lean practices with Six Sigma's rigorous quality management techniques. As a result, organizations experience a boost in productivity and overall performance improvement.
Cost Reduction
Implementing Six Sigma results in substantial cost reduction for organizations. Systems and teams identify inefficiencies and waste within their processes. By addressing these issues, they reduce operational costs significantly. The methodology emphasizes data-driven decision-making, which helps teams allocate resources more effectively. Lean Six Sigma further aids in minimizing waste, ensuring that every resource contributes to value creation. This focus on efficiency translates into lower production costs and increased profitability. Organizations that embrace Six Sigma often see a positive impact on their bottom line, making it a valuable investment for long-term success.
Increased Customer Satisfaction
Customer satisfaction lies at the heart of Six Sigma methodology. Systems and teams prioritize understanding and meeting customer needs. They gather feedback and analyze data to ensure that products and services align with customer expectations. This commitment to quality management leads to higher levels of customer satisfaction. By consistently delivering what customers want, organizations build trust and loyalty. Six Sigma's focus on continuous improvement ensures that systems and teams remain responsive to changing customer demands. As a result, clients experience enhanced satisfaction, leading to repeat business and positive word-of-mouth referrals. For those eager to learn more about achieving these benefits, reaching out to experts can provide invaluable insights.
Real-World Examples of Six Sigma Success
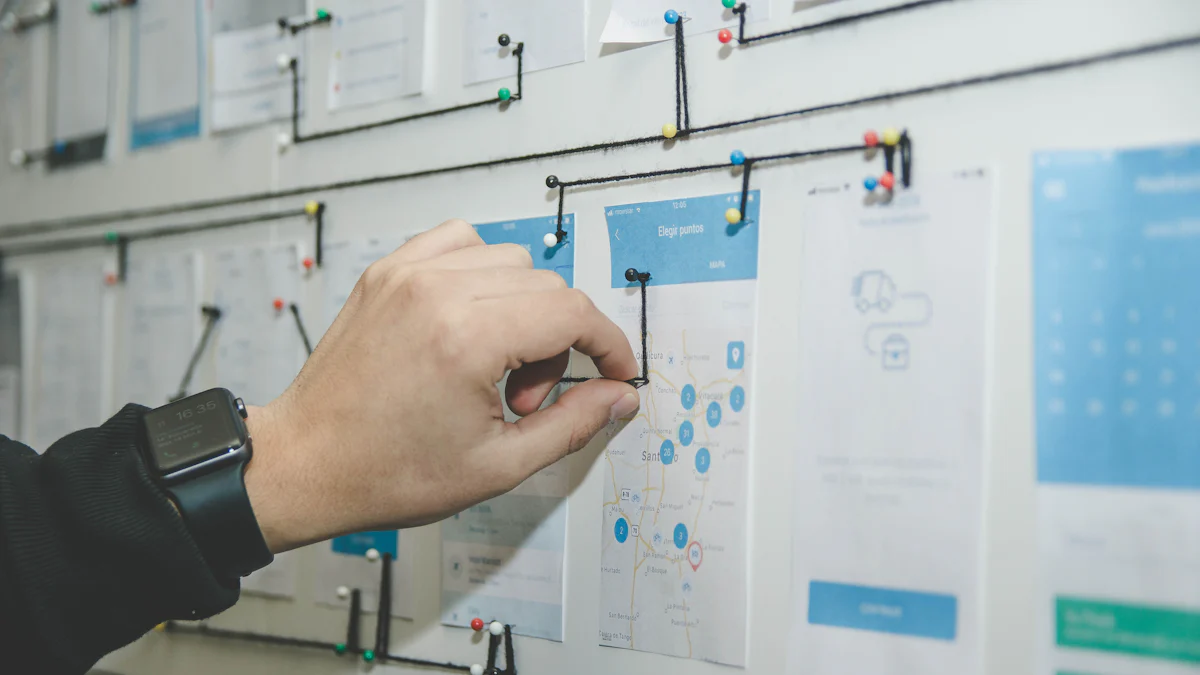
Case Study 1: Motorola's Quality Improvement
Motorola pioneered the Six Sigma methodology in the 1980s. They aimed to enhance their manufacturing processes by reducing defects and variability. Systems and teams at Motorola focused on data-driven decision-making. They identified areas for improvement and implemented changes. This approach led to significant quality improvements. Motorola's commitment to Six Sigma resulted in a drastic reduction in defects. Their products met higher standards, which increased customer satisfaction. The success of Six Sigma at Motorola set a precedent for other organizations. It demonstrated the potential of this methodology to transform business operations. For those eager to learn more about Motorola's journey, reaching out to experts can provide invaluable insights.
Case Study 2: General Electric's Operational Excellence
General Electric (GE) embraced Six Sigma in the 1990s. They sought to achieve operational excellence across their diverse business units. Systems and teams at GE adopted the DMAIC process to tackle complex challenges. They focused on process improvement and variation reduction. This approach led to enhanced efficiency and cost savings. GE's commitment to Six Sigma resulted in billions of dollars in savings. Their operations became more streamlined and effective. The success of Six Sigma at GE showcased its versatility and impact. It highlighted the methodology's ability to drive significant improvements in various industries. For those interested in GE's success story, reaching out to experts can provide valuable guidance.
Getting Started with Six Sigma
Embarking on the journey of Six Sigma can transform systems and teams into efficient, quality-driven entities. This section provides essential guidance for those eager to integrate Six Sigma into their operations.
Training and Certification
Training forms the backbone of a successful Six Sigma implementation. Systems and teams should prioritize enrolling in comprehensive training programs. These programs cover the fundamental principles and methodologies of Six Sigma. Participants gain insights into data-driven decision-making and process improvement techniques. Certification follows training, validating the skills acquired. It serves as a testament to an individual's proficiency in Six Sigma practices. Organizations often prefer certified professionals, as they bring structured problem-solving capabilities to the table. For those eager to excel, pursuing certification can open doors to numerous opportunities in quality management.
Tools and Resources
Equipping systems and teams with the right tools and resources is crucial for effective Six Sigma implementation. Various software solutions assist in data analysis and process mapping. These tools enable teams to visualize processes and identify areas for improvement. Lean Six Sigma tools, such as value stream mapping and root cause analysis, further enhance efficiency. Access to online resources, including webinars and forums, provides continuous learning opportunities. Systems and teams benefit from staying updated with the latest trends and techniques in Six Sigma. By leveraging these resources, they can drive significant improvements in their operations.
Tips for Beginners
Beginners embarking on the Six Sigma journey should focus on a few key strategies. First, systems and teams should start small. Selecting a manageable project allows them to apply Six Sigma principles effectively. They should emphasize understanding customer needs and gathering relevant data. This approach ensures that improvements align with client expectations. Collaboration within teams fosters diverse perspectives and innovative solutions. Beginners should also seek mentorship from experienced practitioners. Learning from experts provides invaluable insights and accelerates the learning curve. By following these tips, systems and teams can successfully navigate the initial stages of Six Sigma implementation.
Overcoming Challenges in Six Sigma Implementation
Implementing Six Sigma can transform organizations, but it comes with its own set of challenges. Systems and teams often encounter obstacles that can hinder progress. Understanding these challenges and developing strategies to overcome them is crucial for successful implementation.
Common Obstacles
Resistance to Change: Many employees resist new methodologies. They may feel comfortable with existing processes. This resistance can slow down Six Sigma adoption. Systems and teams must address this by fostering a culture of openness and adaptability.
Lack of Training: Inadequate training can lead to poor implementation. Employees may not fully understand Six Sigma principles. This gap can result in ineffective quality management. Comprehensive training programs are essential to equip teams with the necessary skills.
Insufficient Resources: Implementing Six Sigma requires time and resources. Some organizations struggle to allocate these effectively. This can impede progress and affect quality improvement efforts. Systems and teams need to plan resource allocation carefully.
Data Collection Issues: Accurate data is vital for Six Sigma success. Poor data collection can lead to incorrect root cause analysis. This affects decision-making and performance improvement. Systems and teams must ensure robust data collection processes.
Strategies for Success
Promote a Culture of Continuous Improvement: Encourage systems and teams to embrace change. Highlight the benefits of Six Sigma and lean six sigma. This approach fosters a positive attitude towards quality management and improvement.
Invest in Training and Development: Provide comprehensive training for all team members. Ensure they understand Six Sigma tools and techniques. Certification programs can validate their skills and enhance their confidence.
Allocate Resources Wisely: Plan resource allocation strategically. Ensure systems and teams have the necessary tools and support. This enables them to focus on quality improvement and achieve desired outcomes.
Enhance Data Collection Processes: Implement robust data collection methods. Ensure accuracy and reliability in data gathering. This supports effective root cause analysis and informed decision-making.
Engage Leadership Support: Secure commitment from leadership. Their support can drive Six Sigma initiatives forward. Leaders can champion the methodology and motivate systems and teams.
By addressing these challenges, systems and teams can successfully implement Six Sigma. They can achieve significant quality improvement and performance enhancement. For those eager to learn more, reaching out to experts can provide invaluable insights.
The six sigma methodology stands as a cornerstone in achieving operational excellence. Systems and teams that embrace six sigma witness remarkable transformations. They enhance quality, reduce costs, and boost customer satisfaction. Six sigma empowers organizations to refine processes and eliminate defects. This leads to success across various domains. By focusing on data-driven decision-making, systems and teams ensure consistent improvement. For those eager to explore further, reaching out to experts can provide invaluable insights. Six sigma remains a powerful tool for those seeking sustained success.
FAQ
What is Six Sigma?
Six Sigma is a data-driven methodology that aims to improve business processes by reducing defects and variability. It focuses on enhancing quality and efficiency in operations. Systems and teams use Six Sigma to identify and eliminate the root causes of defects, ensuring consistent and high-quality outcomes.
How does Six Sigma benefit organizations?
Organizations benefit from Six Sigma through improved quality, reduced costs, and increased customer satisfaction. Systems and teams streamline processes, leading to enhanced operational efficiency. By focusing on data-driven decision-making, they achieve significant performance improvements.
What is the difference between DMAIC and DMADV?
DMAIC and DMADV are both Six Sigma methodologies. DMAIC stands for Define, Measure, Analyze, Improve, and Control. It focuses on improving existing processes. DMADV stands for Define, Measure, Analyze, Design, and Verify. It is used for designing new processes or products. Systems and teams choose the appropriate methodology based on their specific needs.
Why is customer focus important in Six Sigma?
Customer focus is crucial in Six Sigma because it ensures that products and services meet client expectations. Systems and teams prioritize understanding customer needs, leading to higher satisfaction and loyalty. By aligning processes with customer requirements, organizations build trust and enhance their reputation.
How can systems and teams get started with Six Sigma?
Systems and teams can start with Six Sigma by enrolling in training programs and obtaining certification. They should equip themselves with the right tools and resources for effective implementation. Starting with manageable projects allows them to apply Six Sigma principles successfully. For more guidance, reaching out to experts can provide invaluable insights.
What challenges might systems and teams face during implementation?
Systems and teams may encounter challenges such as resistance to change, lack of training, and insufficient resources. Accurate data collection can also pose difficulties. Addressing these obstacles requires promoting a culture of continuous improvement and investing in training and development.
How does Six Sigma ensure continuous improvement?
Six Sigma ensures continuous improvement by emphasizing data-driven decision-making and process optimization. Systems and teams regularly analyze data to identify areas for enhancement. They implement changes and monitor results to maintain quality and efficiency. This ongoing effort leads to sustained success.
Can Six Sigma be applied in any industry?
Yes, Six Sigma can be applied across various industries, including manufacturing, healthcare, and services. Systems and teams tailor the methodology to suit their specific industry needs. By focusing on quality and efficiency, they achieve remarkable improvements regardless of the sector.
What role does leadership play in Six Sigma implementation?
Leadership plays a vital role in Six Sigma implementation by providing support and direction. Leaders champion the methodology and motivate systems and teams. Their commitment drives Six Sigma initiatives forward, ensuring successful adoption and sustained improvements.
How can systems and teams measure the success of Six Sigma?
Systems and teams measure the success of Six Sigma by evaluating key performance indicators (KPIs) and comparing them to predefined goals. They assess improvements in quality, efficiency, and customer satisfaction. Regular audits and reviews help ensure that the gains achieved are maintained over time. For further insights, reaching out to experts can provide valuable guidance.