The Step-by-Step Guide to Implementing Lean Methodology
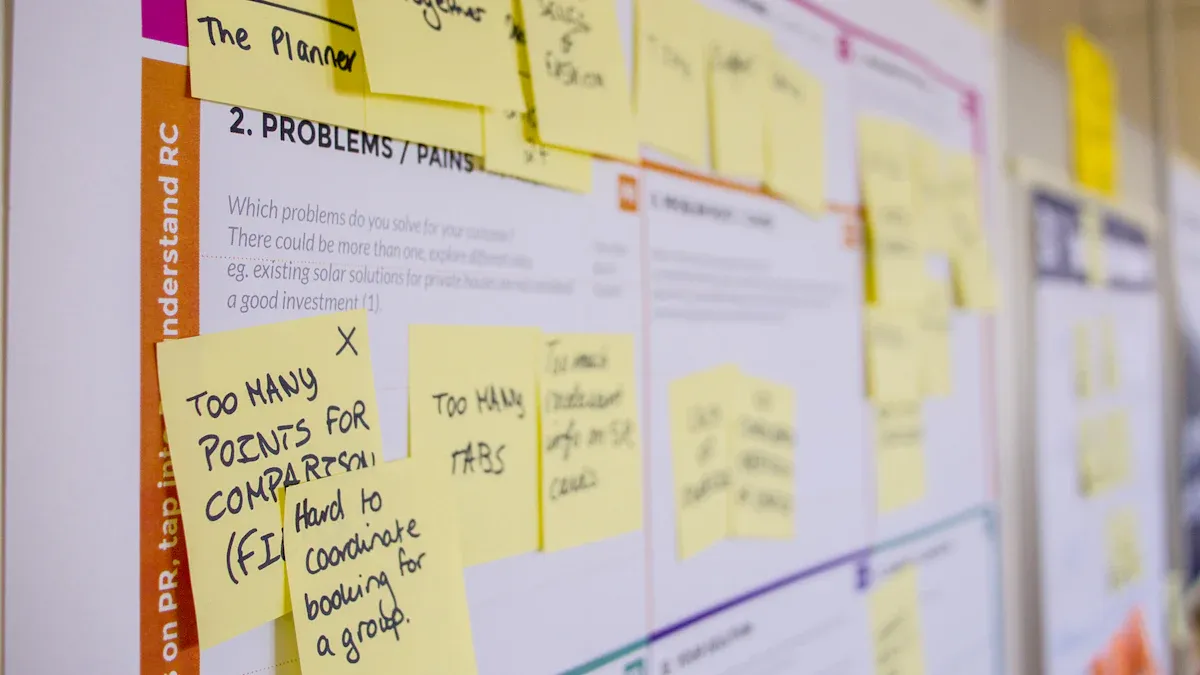
Lean Methodology serves as a structured system for continuous improvement and waste elimination. It empowers teams to focus on value-adding activities, ensuring processes align with customer needs. By fostering efficiency, Lean helps organizations deliver optimal results while minimizing unnecessary steps for both clients and customers.
Across industries, Lean has transformed operations. Manufacturing systems have seen reduced waste and improved quality control, while healthcare teams have enhanced productivity and patient care. These optimization steps not only streamline workflows but also prioritize clients' satisfaction and adaptability to changing demands from customers.
Organizations adopting Lean Methodology often experience significant benefits, including cost savings, reduced bottlenecks, and stakeholder visibility. Its emphasis on continuous improvement encourages teams to refine processes and innovate consistently, ultimately enhancing the experience for both clients and customers.
Key Takeaways
Lean Methodology helps teams improve and remove waste to work better.
Knowing what customers want is key to adding real value.
Mapping steps shows problems and waste, making work smoother.
Creating flow stops delays, making work steady and customers happy.
Pull systems match work to customer needs, cutting extra work and waste.
Always improving builds a habit of fixing and bettering processes.
Lean saves money by cutting waste and using resources wisely.
Training and Lean tools help teams use Lean well and keep improving.
Core Principles of Lean Methodology
Lean Methodology revolves around a set of core principles that guide teams toward efficiency and continuous improvement. These principles include defining value, mapping the value stream, creating flow, establishing pull, and pursuing perfection. Each principle interconnects to form a cohesive system that enhances performance and delivers value to customers.
Define Value
Defining value is the foundation of Lean Methodology. Teams must understand what customers truly need and expect. Value is anything that directly contributes to meeting these needs. For example, in manufacturing, value might involve producing high-quality products that meet customer specifications. In healthcare, it could mean reducing patient wait times while maintaining excellent care standards.
To define value effectively, organizations often use practices like Kaizen, Just-in-Time (JIT), and Kanban. These tools help identify areas where improvements can be made. For instance, Kaizen encourages employees to suggest small, incremental changes that enhance processes. JIT ensures that production aligns with demand, minimizing waste and excess inventory. Kanban provides a visual system for managing workflows and signaling when resources need replenishment.
Lean Practice | Description |
---|---|
Kaizen | Involves all employees in identifying and implementing small, incremental improvements. |
Just-in-Time (JIT) | Aims to produce only what is needed, minimizing inventory and reducing waste. |
Kanban | A visual tool for managing inventory and production, signaling when to replenish supplies. |
By focusing on value, teams can align their efforts with customer priorities, ensuring that every step in the process contributes to the desired outcome.
Map the Value Stream
Mapping the value stream involves visualizing the entire workflow to identify areas of waste and inefficiency. This step helps teams understand how value flows through the system and where it gets interrupted. A value stream map typically includes stages such as the customer, trigger, first process, last process, and final deliverable.
Effective value stream mapping requires separating core and support streams. Teams should determine the desired outcome and work backward to identify the steps needed to achieve it. Common issues uncovered during this process include disconnected processes, unclear information, and long delays. Addressing these problems ensures a smoother workflow and a better customer experience.
Key steps in value stream mapping:
Define core and support streams separately.
Determine the desired outcome and work backward.
Visually map out the value stream, including all stages.
By prioritizing areas of waste, teams can streamline operations and focus on activities that add value.
Create Flow
Creating flow ensures that work progresses steadily and predictably through the system. A consistent flow minimizes interruptions and prevents waste accumulation. For example, in software development, a smooth flow might involve reducing handoff delays between teams to ensure timely delivery.
To achieve good flow, teams must identify and eliminate obstacles causing bottlenecks. Techniques like Just-in-Time production and cross-training employees can enhance efficiency. Monitoring workflows regularly helps maintain uninterrupted progress.
Identify and eliminate obstacles causing delays and bottlenecks.
Use techniques like Just-in-Time (JIT) production and cross-training to enhance efficiency.
Continuously monitor workflows to ensure uninterrupted flow.
A well-maintained flow not only improves reliability but also adds value for customers and stakeholders. Teams that prioritize flow can deliver results faster and with greater consistency.
Establish Pull
Establishing pull ensures that production aligns with real-time customer demand. This principle prevents overproduction and reduces waste by producing only what is needed when it is needed. Teams can achieve this by implementing just-in-time (JIT) practices, which synchronize production schedules with customer requirements.
For example, in manufacturing, a pull system might involve producing components only after receiving an order. This approach eliminates excess inventory and minimizes storage costs. Similarly, in healthcare, pull systems can help manage patient flow by scheduling appointments based on available resources and patient needs. These systems ensure that services are delivered efficiently without unnecessary delays.
To implement a pull system effectively, teams should:
Analyze customer demand patterns to understand real-time needs.
Use visual tools like Kanban boards to signal when production or services should begin.
Monitor and adjust workflows regularly to maintain alignment with demand.
Tip: Teams should focus on communication and collaboration to ensure that all stakeholders understand the pull system. Clear communication helps avoid disruptions and ensures smooth operations.
By aligning production with demand, organizations can enhance efficiency and deliver value to customers. This step is crucial for maintaining a lean and responsive system.
Pursue Perfection
Pursuing perfection involves fostering a culture of continuous improvement. Teams must regularly review processes, identify inefficiencies, and implement changes to achieve optimal performance. This principle encourages organizations to strive for excellence in every aspect of their operations.
Many organizations have successfully pursued perfection using Lean principles. For instance:
Organization | Lean Principles Applied | Outcomes |
---|---|---|
Ford | Kaizen, Six Sigma, Total Quality Management | Improved product quality, reduced costs, decreased waste |
Bank of America | Hybrid of lean manufacturing principles and Six Sigma | Enhanced operational efficiency and customer satisfaction |
General Electric | Lean management, Genba, value stream mapping | Corrected initial bottlenecks, reduced waste, improved process efficiency |
Toyota | Became a leading automaker known for efficient production and high-quality vehicles |
Toyota, for example, has become a leader in the automotive industry by applying its Toyota Production System (TPS). This system focuses on eliminating waste, improving efficiency, and delivering high-quality products. By continuously refining its processes, Toyota has set a benchmark for operational excellence.
To pursue perfection, teams should:
Encourage employees to suggest improvements through practices like Kaizen.
Regularly evaluate workflows to identify areas for refinement.
Use metrics to track progress and measure the impact of changes.
Note: Continuous improvement is not a one-time effort. Teams must remain committed to reviewing and enhancing processes to sustain long-term success.
By embracing a mindset of continuous improvement, organizations can unlock their full potential. This principle ensures that systems and teams consistently deliver value to clients while adapting to changing demands.
Benefits of Lean Methodology
Improved Efficiency
Lean Methodology enhances efficiency by streamlining workflows and eliminating unnecessary steps. Systems and teams can focus on value-adding activities, reducing delays and improving overall productivity. For instance, in manufacturing, Lean practices like Just-in-Time (JIT) production ensure that materials arrive only when needed, minimizing idle time and excess inventory. Similarly, in healthcare, Lean principles help optimize patient flow, reducing wait times and improving care delivery.
Cross-training employees is another strategy that boosts efficiency. By equipping team members with diverse skills, organizations can ensure flexibility and maintain operations even during staff shortages. Regular monitoring of workflows also plays a crucial role. It helps identify bottlenecks and allows teams to address issues promptly, ensuring smooth and uninterrupted processes.
Tip: Encouraging collaboration among teams can further enhance efficiency. Open communication ensures that everyone works toward common goals, reducing misunderstandings and redundancies.
Cost Savings
Lean Methodology significantly reduces costs by eliminating waste and focusing on value-driven processes. Organizations across industries benefit from streamlined operations, which lower production expenses and improve resource utilization. The table below highlights how Lean contributes to cost savings:
Benefit | Description |
---|---|
Enhanced Product Quality | Focuses on reducing defects and variations, resulting in higher-quality products. |
Increased Customer Satisfaction | Faster production times and higher quality products contribute to greater customer satisfaction. |
Reduced Production Costs | Eliminating waste and non-value-added activities significantly lowers production costs. |
Improved Efficiency | Streamlined processes lead to smoother workflows and reduced cycle times. |
Continuous Improvement (Kaizen) | Regularly reviewing and improving processes enhances efficiency and quality. |
For example, in manufacturing, Lean practices reduce material waste and energy consumption, leading to lower operational costs. In software development, Lean principles help teams avoid overproduction by aligning work with customer demand, saving time and resources. These cost-saving measures not only benefit organizations but also allow them to offer competitive pricing to clients.
Enhanced Customer Satisfaction
Lean Methodology prioritizes customer needs, ensuring that systems and teams deliver high-quality products and services efficiently. By focusing on value, organizations can meet or exceed customer expectations. For instance, faster production times and reduced defects result in reliable products that customers trust. In service industries, Lean practices improve response times and personalize experiences, enhancing client satisfaction.
Continuous improvement plays a vital role in maintaining high customer satisfaction levels. Teams regularly review feedback and refine processes to address evolving needs. Visual tools like Kanban boards help track progress and ensure timely delivery, further boosting customer confidence.
Note: Satisfied customers are more likely to remain loyal and recommend services to others. Investing in Lean practices can create a positive cycle of trust and growth for organizations.
Better Team Collaboration
Lean Methodology fosters better collaboration among team members by encouraging open communication and shared goals. Teams work together to identify inefficiencies, brainstorm solutions, and implement improvements. This collective effort builds trust and strengthens relationships within the organization.
One of the key aspects of Lean is its emphasis on transparency. Visual tools like Kanban boards allow teams to track progress and identify bottlenecks in real time. These tools ensure that everyone stays informed about the status of tasks and responsibilities. When team members have a clear understanding of their roles, they can coordinate more effectively and avoid duplication of efforts.
Cross-training is another strategy that enhances collaboration. By equipping employees with diverse skills, organizations create a more versatile workforce. Team members can step in to support one another during peak workloads or staff shortages. This flexibility reduces stress and fosters a sense of unity among employees.
Tip: Encouraging regular team meetings can further improve collaboration. These meetings provide a platform for discussing challenges, sharing updates, and celebrating successes.
Lean also promotes a culture of mutual respect and accountability. Teams take ownership of their work and hold each other accountable for meeting goals. This shared responsibility motivates individuals to perform at their best, contributing to the overall success of the organization.
By prioritizing collaboration, Lean Methodology helps systems and teams achieve greater efficiency and innovation. Organizations that embrace this approach often experience improved morale and stronger team dynamics.
Increased Flexibility
Lean Methodology enhances flexibility by enabling systems and teams to adapt quickly to changing circumstances. This adaptability is crucial in today’s fast-paced business environment, where customer demands and market conditions can shift rapidly.
Lean promotes adaptability, allowing teams to adjust to changing circumstances and customer demands.
It reduces bottlenecks, making processes more fluid and less rigid.
The continuous improvement mindset fosters ongoing refinement of processes, ensuring they evolve as needed.
For example, in manufacturing, Lean practices like Just-in-Time (JIT) production allow teams to align output with real-time demand. This approach minimizes overproduction and ensures that resources are used efficiently. In service industries, Lean principles help organizations respond to customer needs more effectively by streamlining workflows and eliminating unnecessary steps.
Flexibility also stems from Lean’s focus on continuous improvement. Teams regularly review processes to identify areas for refinement. This proactive approach ensures that workflows remain efficient and relevant, even as external conditions change. By embracing this mindset, organizations can stay competitive and deliver consistent value to their clients.
Note: Flexibility is not just about reacting to change. It involves anticipating potential challenges and preparing systems to handle them effectively.
Lean Methodology empowers teams to remain agile and responsive. This flexibility benefits both the organization and its clients, ensuring that systems can meet evolving demands without compromising quality or efficiency.
Step-by-Step Guide to Implementing Lean Methodology
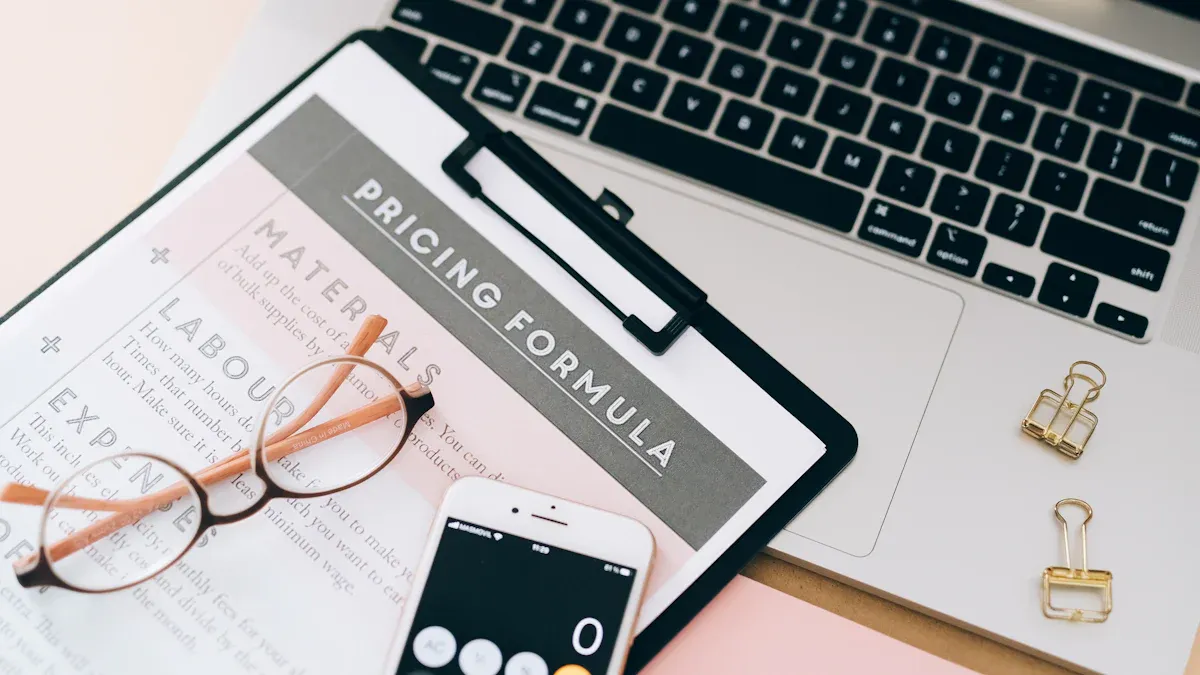
Identify Value
Understand customer needs and expectations.
Understanding customer needs forms the foundation of Lean Methodology. Systems and teams must identify what customers truly value in their products or services. This involves gathering feedback, analyzing market trends, and observing customer behavior. For example, a manufacturing team might focus on producing durable and reliable products, while a healthcare team might prioritize reducing patient wait times and improving care quality. By aligning processes with customer expectations, organizations can ensure that every step contributes to delivering value.
Define what constitutes value in your processes.
Defining value requires a clear understanding of which activities directly contribute to meeting customer needs. Teams should evaluate their workflows to distinguish between value-adding and non-value-adding steps. For instance, in software development, writing and testing code are value-adding activities, while waiting for approvals may not be. By focusing on value-driven processes, organizations can eliminate unnecessary steps and enhance efficiency.
Tip: Regularly revisit customer feedback to ensure that the definition of value evolves with changing expectations.
Map the Value Stream
Visualize the flow of processes.
Mapping the value stream involves creating a visual representation of how work flows through a system. This step helps teams identify inefficiencies and areas of waste. To create an effective value stream map, teams should:
Define core and support streams separately.
Determine the desired outcome and work backward.
Include all stages, from customer triggers to final deliverables.
A value stream map serves as a blueprint for Lean implementation. It links material flow with information flow, providing a unique perspective on the entire process. This visualization also fosters a common language for discussing workflows, ensuring that all stakeholders understand the system.
Identify and prioritize areas of waste.
Once the value stream is mapped, teams can pinpoint sources of waste. These may include delays, redundant steps, or excessive inventory. Prioritizing these areas allows teams to focus their efforts on the most impactful improvements. For example, addressing a bottleneck in production could significantly reduce lead times and enhance customer satisfaction.
Note: A well-mapped value stream not only identifies waste but also clarifies decisions regarding process flow, preventing default actions that may not align with Lean principles.
Create Flow
Streamline workflows to eliminate bottlenecks.
Creating flow ensures that work progresses smoothly through the system without interruptions. Streamlining workflows involves standardizing processes, empowering teams, and fostering collaboration. The table below highlights strategies for eliminating bottlenecks:
Strategy | Description |
---|---|
Streamlining with Standard Processes | Standardizing workflow processes eliminates confusion and enhances efficiency. |
Empowering Your Team | Encouraging team members to share insights can lead to innovative solutions and boost morale. |
Collaboration is Key | Cross-department collaboration helps identify and resolve bottlenecks affecting the entire company. |
Automation also plays a crucial role in streamlining workflows. Automating repetitive tasks, such as approval processes, can significantly reduce delays and improve efficiency.
Ensure smooth transitions between process steps.
Smooth transitions between steps are essential for maintaining a consistent flow. Teams should focus on reducing handoff delays and ensuring that each step is ready to proceed as soon as the previous one is completed. Techniques like cross-training employees can help achieve this by enabling team members to step in when needed, minimizing disruptions.
Tip: Embracing affordable technology can further enhance flow by automating routine tasks and reducing manual errors.
By creating a seamless flow, systems and teams can deliver results more quickly and reliably, ultimately enhancing customer satisfaction.
Establish Pull
Align production with real-time customer demand.
Aligning production with real-time customer demand ensures that systems and teams produce only what is needed, when it is needed. This approach eliminates overproduction and reduces waste. For example, in manufacturing, teams can analyze customer order patterns to adjust production schedules dynamically. This ensures that resources are allocated efficiently and inventory levels remain optimal.
To achieve this alignment, teams should focus on understanding customer behavior. Tools like demand forecasting and data analytics can provide valuable insights into purchasing trends. These insights help organizations anticipate needs and respond promptly. In service industries, such as healthcare, aligning with demand might involve scheduling staff based on patient flow data. This ensures that resources are available during peak times, improving service delivery.
Tip: Teams should regularly review demand data to identify patterns and adjust workflows accordingly. This proactive approach minimizes delays and enhances customer satisfaction.
Implement just-in-time (JIT) practices.
Just-in-time (JIT) practices play a crucial role in establishing pull systems. JIT ensures that materials, products, or services are delivered exactly when they are needed, reducing excess inventory and storage costs. For instance, in a retail setting, JIT might involve restocking shelves based on real-time sales data. This prevents overstocking and ensures that customers find what they need.
Implementing JIT requires close collaboration between teams and suppliers. Clear communication ensures that everyone understands production schedules and delivery timelines. Visual tools like Kanban boards can help track inventory levels and signal when replenishment is necessary. In addition, cross-training employees allows teams to adapt quickly to changes in demand, maintaining smooth operations.
Note: JIT practices not only reduce waste but also improve cash flow by minimizing the capital tied up in inventory. This makes it a valuable strategy for organizations aiming to optimize resources.
Pursue Perfection
Foster a culture of continuous improvement.
Fostering a culture of continuous improvement encourages systems and teams to strive for excellence. Organizations can achieve this by creating an environment where employees feel empowered to suggest changes and experiment with new ideas. Regular ideation sessions, for example, provide a platform for discussing improvements and exploring innovative technologies. Surveys and polls can also help gather employee feedback to identify pain points and areas for enhancement.
Many organizations have successfully implemented continuous improvement strategies. Examples include:
Hosting think tanks to brainstorm new solutions.
Conducting proof-of-concept projects to test ideas on a small scale.
Providing training to help employees adapt to new technologies.
Optimizing processes to reduce waste and boost efficiency.
Organizing stand-up meetings for open team discussions.
These practices not only enhance workflows but also build a sense of ownership among employees. Teams that feel valued and involved are more likely to contribute actively to the organization's success.
Regularly review and refine processes.
Regularly reviewing and refining processes ensures that systems remain efficient and relevant. Teams should evaluate workflows periodically to identify inefficiencies and implement necessary changes. Metrics and key performance indicators (KPIs) can provide valuable insights into process performance. For example, tracking cycle times or defect rates helps pinpoint areas that need improvement.
Organizations can also use editing and quality assurance (QA) processes to maintain high standards. For instance, incorporating QA checks into production workflows ensures that outputs meet customer expectations. Additionally, enhancing workplace environments can boost productivity and morale, further supporting continuous improvement efforts.
Tip: Teams should document changes and monitor their impact over time. This helps identify successful strategies and ensures that improvements are sustained.
By fostering a culture of improvement and regularly refining processes, organizations can achieve long-term success. These practices enable systems and teams to adapt to changing demands while consistently delivering value to clients.
Common Challenges and Solutions in Lean Implementation
Implementing Lean Methodology can transform systems and teams, but it often comes with challenges. Addressing these obstacles effectively ensures a smoother transition and long-term success.
Resistance to Change
Resistance to change is one of the most common hurdles in Lean implementation. Employees may feel uncertain about new processes or fear that changes could disrupt their routines.
Educate employees on Lean benefits.
Education plays a critical role in overcoming resistance. Teams need to understand how Lean practices improve workflows and benefit both employees and customers. Training programs can introduce Lean concepts and demonstrate their practical applications. For example, workshops can show how Lean reduces repetitive tasks, allowing employees to focus on more meaningful work.
Tip: Clear communication about Lean's purpose and benefits fosters trust and reduces skepticism.
Involve teams in the Lean process.
Engaging employees in the transformation process builds ownership and reduces resistance. Teams should participate in identifying inefficiencies and suggesting improvements. This involvement not only empowers employees but also ensures that changes align with their day-to-day realities. Recognizing contributions and celebrating small wins further boosts morale and reinforces the importance of Lean practices.
Lack of Leadership Support
Strong leadership is essential for Lean initiatives to succeed. Without it, teams may lack direction and motivation, leading to stalled progress.
Demonstrate ROI to gain leadership buy-in.
Leaders often hesitate to support Lean due to concerns about its return on investment (ROI). Demonstrating tangible benefits, such as cost savings or improved efficiency, can help gain their commitment. For instance, presenting data on reduced production costs or increased customer satisfaction highlights Lean's value. Leaders who see clear evidence of ROI are more likely to champion Lean initiatives.
Provide training for leaders.
Leadership training ensures that managers understand Lean principles and their role in driving change. Leaders should model Lean behaviors, such as fostering collaboration and prioritizing continuous improvement. Their active participation sends a strong message to teams, reinforcing the importance of Lean practices.
Note: Leadership alignment with Lean goals creates a unified vision, motivating teams to embrace the methodology.
Sustaining Improvements
Sustaining improvements requires ongoing effort. Without proper systems in place, teams may revert to old habits, undermining Lean's long-term impact.
Use metrics to track progress.
Metrics provide a clear picture of progress and highlight areas for improvement. Effective metrics include safety, cost, product quality, and customer satisfaction. For example, tracking time savings can reveal bottlenecks, while monitoring employee satisfaction ensures that changes positively impact the workforce. Regularly reviewing these metrics helps teams stay on track and maintain momentum.
Create accountability systems.
Accountability systems ensure that improvements are sustained over time. Assigning ownership of specific processes encourages teams to take responsibility for maintaining standards. Regular check-ins and performance reviews keep everyone aligned with Lean goals. Visual tools, such as Kanban boards, can also help track tasks and ensure accountability.
Tip: Combining metrics with accountability systems creates a feedback loop that drives continuous improvement.
By addressing these challenges, systems and teams can successfully implement Lean Methodology and achieve lasting results.
Real-World Applications of Lean Methodology
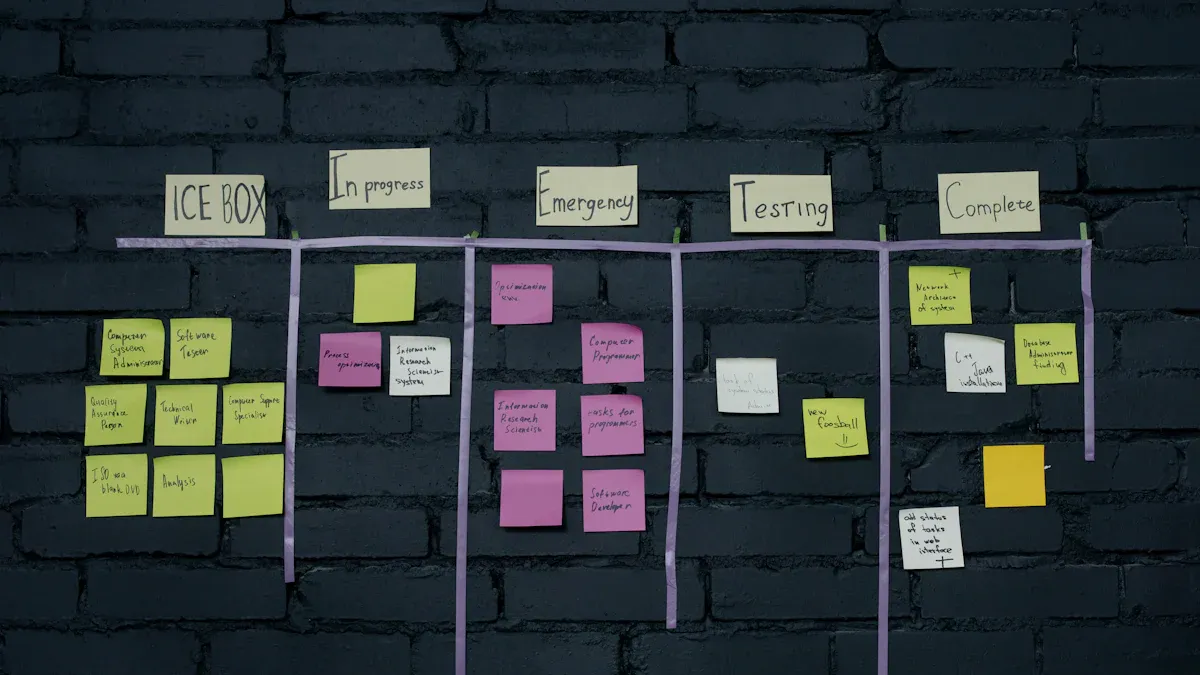
Lean Methodology has proven its versatility across various industries, enabling systems and teams to optimize processes, reduce waste, and deliver value. Below are examples of how Lean principles have been successfully applied in manufacturing, healthcare, and software development.
Lean in Manufacturing
Manufacturing industries have long embraced Lean principles to enhance efficiency and minimize waste. Systems and teams in this sector use Lean tools to streamline production, improve quality, and reduce costs. Several notable examples illustrate the impact of Lean in manufacturing:
FedEx Express improved aircraft maintenance by introducing milestones in their C-check process. This change increased annual C-checks from 14 to 30 and reduced man-hours from 32,715 to 21,535.
Nike implemented a Manufacturing Index and just-in-time production to enhance consistency and minimize excess inventory.
Harley-Davidson utilized Total Productive Maintenance and kaizen to stabilize operations, improve inventory management, and reduce waste.
John Deere adopted automated quality control systems, enabling quicker defect identification and resolution.
Intel focused on reducing works-in-process and waste while maintaining high quality, boosting productivity.
Ford Motor Company applied Lean methodologies to improve assembly line efficiency, enhance product quality, and lower costs.
These examples demonstrate how manufacturing systems and teams can achieve remarkable results by adopting Lean practices. By focusing on waste reduction and process optimization, organizations deliver high-quality products efficiently.
Lean in Healthcare
Healthcare systems have increasingly turned to Lean Methodology to improve patient care and operational efficiency. Lean principles help teams focus on value-adding activities while eliminating wasteful processes. Key benefits of Lean in healthcare include:
Smarter business processes where work aligns with real-time demand.
More effective use of resources, ensuring materials are utilized only when needed.
Improved workforce focus by removing non-value-adding tasks.
Increased efficiency and productivity through enhanced focus on essential activities.
For example, healthcare teams use Lean to streamline patient flow, reduce wait times, and optimize resource allocation. By aligning processes with patient needs, systems deliver better care while minimizing delays. These improvements not only enhance patient satisfaction but also create a more efficient and responsive healthcare environment.
Lean in Software Development
Lean principles have transformed software development by helping teams create value, reduce waste, and improve quality. Effective testing and regular feedback play a crucial role in ensuring high-quality outcomes. Key practices in Lean software development include:
Releasing minimum viable products (MVPs) as an initial strategy.
Adding features based on client or user feedback.
Aligning product development with actual market requirements.
Delivering value to customers swiftly to gain a competitive edge.
Lean also emphasizes continuous improvement, enabling teams to refine their processes and focus on tasks that deliver the most value. By eliminating waste and prioritizing customer needs, software development systems can produce reliable and efficient solutions. This approach ensures that products meet market demands while maintaining high standards of quality.
Tip: Teams in software development benefit from Lean by fostering collaboration and maintaining open communication. Regular feedback loops ensure alignment with customer expectations.
Lean Methodology empowers systems and teams across industries to achieve excellence. Whether in manufacturing, healthcare, or software development, Lean principles drive efficiency, reduce waste, and enhance value delivery. Organizations seeking to optimize their processes can learn from these real-world applications and adapt Lean practices to their unique needs.
Tips for a Successful Lean Journey
Start Small and Scale Gradually
Starting small allows systems and teams to test Lean principles on a manageable scale before expanding. This approach minimizes risks and ensures that processes align with organizational goals. By focusing on smaller initiatives, teams can identify what works and refine their strategies for broader implementation.
Faster Time to Market: Launching a minimum viable product (MVP) enables quicker delivery to customers. Teams can gather feedback early and make necessary adjustments, ensuring the final product meets expectations.
Cost-Efficiency and Resource Optimization: Concentrating on value-adding activities helps avoid unnecessary expenses. Systems can allocate resources more effectively, reducing waste and maximizing output.
Customer-Centric Approach: Engaging customers during the development process ensures that their needs drive decision-making. This fosters loyalty and enhances the overall value delivered.
Tip: Teams should document lessons learned during the initial phase. These insights can guide future scaling efforts, ensuring consistent success.
Invest in Training and Education
Training equips teams with the knowledge and skills needed to implement Lean effectively. Tailored programs ensure that employees at all levels understand their roles in the Lean journey. Organizations should prioritize hands-on learning and continuous support to build confidence and foster collaboration.
Conduct a thorough assessment of organizational needs to customize training content.
Clearly define training objectives to align with company goals.
Recognize that different roles require varying levels of Lean knowledge.
Incorporate hands-on simulations to reinforce concepts and encourage practical application.
Promote teamwork through group activities and discussions.
Measure training effectiveness using metrics and feedback.
Provide ongoing resources for continuous learning and improvement.
Note: Investing in education not only enhances individual performance but also strengthens team collaboration. Well-trained teams are better equipped to identify inefficiencies and drive meaningful change.
Use Lean Tools and Techniques
Lean tools and techniques provide systems with structured methods to eliminate waste and improve efficiency. These tools enable teams to focus on value-adding activities, streamline workflows, and enhance productivity. Organizations that adopt these practices often experience greater flexibility and improved customer satisfaction.
5S: Organizes workspaces to improve efficiency and reduce clutter.
Kaizen: Encourages continuous improvement by involving all employees in identifying and solving problems.
Single-Minute Exchange of Die (SMED): Reduces changeover times, increasing operational efficiency.
Value Stream Mapping (VSM): Visualizes the flow of value in processes, helping teams identify and address bottlenecks.
Tip: Combining these tools with a culture of continuous improvement ensures long-term success. Teams should regularly evaluate their effectiveness and adapt as needed.
By starting small, investing in education, and leveraging Lean tools, systems and teams can create a strong foundation for their Lean journey. These strategies empower organizations to deliver consistent value while adapting to evolving demands. For more insights on Lean implementation, reach out to us.
Celebrate Successes and Learn from Failures
Recognizing achievements and reflecting on setbacks are essential components of a successful Lean journey. Systems and teams that celebrate milestones foster motivation and build a culture of continuous improvement. At the same time, learning from failures ensures that processes evolve and adapt to challenges.
Celebrating successes reinforces positive behaviors and encourages teams to stay committed to Lean principles. Organizations can acknowledge achievements in several ways:
Hosting team lunches or happy hours to reward collective efforts.
Creating visual displays or dashboards to showcase improvement results.
Sharing success stories during meetings to inspire others.
These practices not only boost morale but also highlight the tangible benefits of Lean implementation. For example, a manufacturing team that reduces production time might display their results on a dashboard for everyone to see. This visibility motivates other teams to strive for similar improvements.
Tip: Celebrations should align with the organization's values. Simple gestures, such as verbal recognition or certificates, can have a significant impact on team morale.
Failures, on the other hand, provide valuable learning opportunities. Systems and teams should approach setbacks with a problem-solving mindset. Conducting retrospectives or after-action reviews helps identify root causes and develop strategies to prevent recurrence. For instance, a healthcare team might analyze a delay in patient flow to uncover inefficiencies in scheduling. By addressing these issues, they can refine their processes and improve outcomes.
Encouraging open discussions about failures fosters a culture of transparency and trust. Teams that feel safe to share challenges are more likely to collaborate on solutions. This openness accelerates learning and strengthens the organization's ability to adapt.
Note: Failures should not be viewed as setbacks but as stepping stones toward improvement. Every challenge presents an opportunity to refine processes and enhance performance.
By celebrating successes and learning from failures, systems and teams can sustain momentum in their Lean journey. These practices create an environment where continuous improvement thrives, ensuring long-term success. For more insights on fostering a Lean culture, reach out to us.
Lean Methodology offers systems and teams a structured path to efficiency and value creation. Its principles, such as eliminating waste and fostering continuous improvement, empower organizations to adapt and thrive. Leaders play a crucial role by championing these efforts and encouraging team ownership. Starting small, experimenting, and embracing the plan-do-check-act cycle ensures steady progress. Systems that prioritize collaboration and persistence can overcome challenges and achieve lasting success. By identifying areas for improvement and exploring Lean tools, organizations can begin their transformative journey today.
FAQ
What is Lean Methodology?
Lean Methodology is a system designed to improve efficiency by eliminating waste and focusing on value-adding activities. It helps systems and teams streamline processes, reduce costs, and enhance customer satisfaction. Organizations across industries use Lean to achieve continuous improvement.
How does Lean Methodology benefit systems and teams?
Lean empowers systems and teams to work more efficiently by identifying and removing unnecessary steps. This approach reduces delays, improves collaboration, and ensures that resources are used effectively. Teams can deliver better results while meeting customer expectations.
Can Lean Methodology be applied to non-manufacturing industries?
Yes, Lean applies to various industries, including healthcare, software development, and retail. Systems and teams in these sectors use Lean principles to optimize workflows, improve service delivery, and adapt to changing customer needs. Its versatility makes it valuable for any organization.
What tools are commonly used in Lean Methodology?
Common Lean tools include 5S, Kaizen, Kanban, and Value Stream Mapping. These tools help systems and teams organize workspaces, identify inefficiencies, and improve workflows. For example, Kanban provides a visual way to manage tasks and track progress.
How can teams start implementing Lean Methodology?
Teams can begin by identifying value, mapping the value stream, and eliminating waste. Starting small with manageable projects allows teams to test Lean principles and refine their approach. Training and collaboration are essential for successful implementation.
What challenges might arise during Lean implementation?
Challenges include resistance to change, lack of leadership support, and difficulty sustaining improvements. Systems and teams can overcome these obstacles by educating employees, involving them in the process, and using metrics to track progress. Leadership commitment is also crucial.
How does Lean Methodology improve customer satisfaction?
Lean focuses on delivering value by aligning processes with customer needs. Systems and teams can reduce delays, improve quality, and personalize services. These improvements enhance the customer experience, fostering trust and loyalty.
Where can I learn more about Lean Methodology?
Readers interested in Lean Methodology can explore additional resources or reach out to us for guidance. Our team provides insights and support to help systems and teams implement Lean effectively and achieve lasting results.