Why Lean Methodology Boosts Team Efficiency
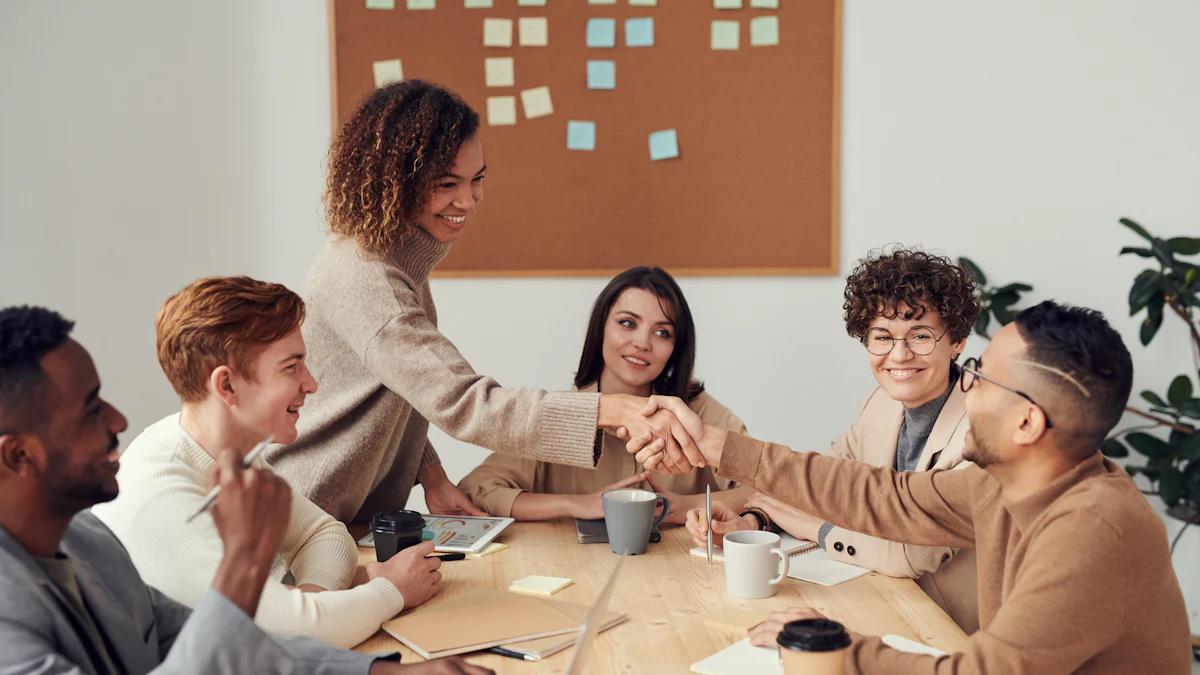
Lean methodology transforms how teams operate by focusing on eliminating waste and enhancing efficiency. It encourages teams to streamline their processes, ensuring every action adds value. By fostering a culture of continuous improvement, lean empowers teams to adapt quickly and deliver high-quality outcomes. This approach, rooted in business management principles, has proven effective across industries, from hiring systems to sales. Combining lean with agile practices further enhances collaboration and adaptability, enabling teams to achieve sustainable success. Organizations adopting this methodology often experience improved productivity, reduced costs, and stronger team engagement.
Key Takeaways
Lean methodology focuses on eliminating waste to enhance team efficiency, ensuring every action adds value.
Implementing continuous improvement (Kaizen) encourages teams to make small, incremental changes that lead to significant efficiency gains over time.
Empowering teams with autonomy in decision-making fosters a culture of ownership, accountability, and faster problem-solving.
Utilizing tools like Kanban boards and value stream mapping helps visualize workflows, identify bottlenecks, and streamline processes.
Engaging team members in goal-setting promotes collaboration and innovation, leading to better outcomes and higher morale.
Organizations adopting lean practices often experience improved productivity, reduced costs, and enhanced customer satisfaction.
Addressing resistance to change through clear communication and training is crucial for successful lean implementation.
What is Lean Methodology?
Lean methodology is a systematic approach designed to enhance efficiency by eliminating waste and focusing on delivering maximum value. It emphasizes continuous improvement and encourages teams to refine their processes to achieve better outcomes. This methodology prioritizes customer value focus, ensuring that every action contributes directly to meeting customer needs. By streamlining workflows and reducing unnecessary steps, lean methodology helps organizations optimize their operations and achieve sustainable success.
Definition of Lean Methodology
Lean methodology revolves around the principle of creating more value with fewer resources. It seeks to identify and eliminate activities that do not contribute to value creation. Teams using this approach aim to deliver high-quality results while minimizing delays, defects, and excess costs. The methodology promotes a culture of ongoing improvement, where teams consistently evaluate their processes to find opportunities for refinement. This focus on efficiency and value creation makes lean methodology a powerful tool for businesses across various industries.
Origins and Core Focus
Historical background and its roots in manufacturing
The origins of lean can be traced back to Toyota in the late 1940s, following World War II. Faced with limited resources, Toyota's founder, Kiichiro Toyoda, and engineers like Taiichi Ohno and Shigeo Shingo developed the Toyota Production System (TPS). This system aimed to reduce inventory costs and improve efficiency by eliminating waste. Over time, these principles evolved into what is now known as lean methodology.
In 1990, the book The Machine That Changed the World introduced lean principles to a global audience. It outlined key concepts such as specifying value, identifying the value stream, and pursuing perfection. These ideas, initially rooted in manufacturing, have since expanded to other sectors, proving their versatility and effectiveness.
Emphasis on efficiency and delivering value to customers
Lean methodology focuses on efficiency by ensuring that every process step adds value. It eliminates wasteful practices like overproduction, waiting, and defects, which can hinder productivity. By prioritizing customer value focus, lean ensures that teams concentrate on activities that directly benefit the customer. This approach not only enhances operational efficiency but also strengthens customer satisfaction by delivering high-quality outcomes quickly and consistently.
The core of lean lies in its ability to adapt and evolve. While its roots are in manufacturing, its principles have been successfully applied to healthcare, software development, and other industries. This adaptability highlights its universal appeal and effectiveness in driving value creation across diverse fields.
Key Principles of Lean Methodology That Drive Efficiency
Eliminating Waste
Definition of waste in processes
Waste refers to any activity or resource within a process that does not add value to the final product or service. Lean methodology identifies waste as a primary obstacle to efficiency. By focusing on the elimination of waste, teams can streamline workflows and ensure that every step contributes meaningfully to the desired outcome. This approach helps organizations reduce unnecessary costs and improve overall productivity.
Examples of common types of waste (e.g., overproduction, waiting, defects)
Lean principles categorize waste into several types, each of which hinders efficiency:
Overproduction: Producing more than what is needed leads to excess inventory and storage costs.
Waiting: Idle time caused by delays in processes or dependencies between tasks slows down progress.
Defects: Errors in products or services require rework, increasing time and resource consumption.
Excess Motion: Unnecessary movement of people or materials adds no value to the process.
Overprocessing: Performing more work or using higher-quality resources than required wastes effort and materials.
For example, in manufacturing, reducing defects through lean process improvement can enhance product quality and customer satisfaction. Similarly, in healthcare, waste reduction has led to shorter patient response times and lower operational costs.
Continuous Improvement (Kaizen)
Explanation of Kaizen and its role in Lean
Kaizen, a Japanese term meaning "change for the better," lies at the heart of continuous improvement in lean methodology. It emphasizes small, incremental changes rather than large-scale overhauls. Teams regularly evaluate their processes to identify inefficiencies and implement adjustments. This iterative approach fosters a culture of learning and adaptability, ensuring that systems evolve to meet changing demands.
Kaizen plays a critical role in lean by encouraging employees at all levels to contribute ideas for improvement. This collective effort not only enhances efficiency but also boosts team morale and engagement.
How small, incremental changes lead to significant efficiency gains
Small changes, when applied consistently, can yield substantial results over time. For instance, a lean initiative in project management showed that high-intensity lean projects were three times more likely to finish ahead of schedule. By addressing minor inefficiencies, teams can create flow in their operations, reducing bottlenecks and improving delivery times.
In industries like manufacturing, continuous process improvement has led to a 30% increase in productivity and a 25% reduction in lead times. These gains demonstrate how incremental adjustments can drive significant efficiency improvements across various sectors.
Empowering Teams
Encouraging team autonomy and decision-making
Lean methodology empowers teams by granting them autonomy in decision-making. When employees have the authority to address issues directly, they can respond to challenges more quickly. This empowerment fosters a sense of ownership and accountability, motivating teams to perform at their best.
For example, agile practices often complement lean by promoting self-organizing teams. This combination enables teams to adapt to changes and deliver value more efficiently.
Benefits of collaboration and faster problem-solving
Collaboration thrives in a lean environment. Teams work together to identify problems, brainstorm solutions, and implement improvements. This collective effort accelerates problem-solving and enhances communication. Transparent workflows, supported by tools like Kanban boards, ensure that everyone stays aligned on goals and progress.
By empowering teams and fostering collaboration, lean creates an environment where innovation and efficiency flourish. Organizations that adopt these practices often experience higher employee satisfaction and retention, further contributing to long-term success.
Practical Benefits of Lean Methodology for Teams
Faster Delivery Times
Lean reduces bottlenecks by streamlining workflows and focusing on the elimination of waste. Teams identify unnecessary steps in their processes and remove them to create a smoother flow of tasks. This approach ensures that resources are allocated efficiently, allowing teams to deliver results faster. For example, by addressing delays caused by waiting or overproduction, lean principles help teams maintain momentum and meet deadlines consistently.
A notable success story highlights how a lean initiative led to a 25% reduction in lead times and a 30% increase in productivity. These improvements not only enhanced operational efficiency but also boosted employee morale. Such outcomes demonstrate how lean enables teams to achieve faster delivery times while maintaining high performance.
Improved Communication and Collaboration
Lean fosters transparency by encouraging teams to visualize their workflows. Tools like Kanban boards provide a clear overview of tasks, responsibilities, and progress. This visibility ensures that every team member stays informed and aligned with project goals. Improved communication reduces misunderstandings and promotes a collaborative environment.
Teamwork thrives under lean practices. Employees work together to identify inefficiencies and propose solutions, creating a culture of shared responsibility. This collaborative approach accelerates problem-solving and strengthens relationships within the team. By prioritizing transparency and teamwork, lean enhances both efficiency and customer satisfaction.
Higher Quality Outcomes
Lean emphasizes quality by addressing defects and reducing errors in processes. Teams focus on delivering value to the customer by ensuring that every step contributes to a high-quality outcome. Waste reduction plays a crucial role in this process, as it eliminates unnecessary actions that could compromise quality.
Continuous improvement under lean principles helps teams refine their workflows and maintain consistent standards. For instance, organizations that adopt lean often experience fewer defects and less rework, leading to better products and services. These benefits of lean management not only improve operational outcomes but also enhance customer satisfaction and loyalty.
How to Implement Lean Methodology in Your Team
Actionable Steps for Adoption
Start with a process audit to identify waste
Teams should begin by conducting a thorough process audit. This step involves analyzing workflows to pinpoint inefficiencies and areas of waste. For example, identifying delays caused by waiting times or unnecessary steps can reveal opportunities for improvement. A detailed audit helps teams understand where resources are being misused and where value is not being added. By focusing on these areas, teams can create a roadmap for implementing lean practices effectively.
A process audit also encourages transparency. Teams gain a clear understanding of their current operations, which fosters collaboration and alignment. Leaders play a critical role in guiding this step, ensuring that the audit remains objective and actionable. This foundational step sets the stage for continuous improvement and long-term success.
Involve the team in setting goals and priorities
Engaging the team in goal-setting ensures that everyone aligns with the objectives of lean methodology. Teams should collectively define priorities based on the findings of the process audit. For instance, if reducing defects is a priority, the team can focus on strategies to enhance quality control. Involving team members in this process fosters a sense of ownership and accountability.
Collaboration during goal-setting also promotes innovation. Team members often bring unique perspectives and ideas that can lead to creative solutions. Leaders should encourage open communication and provide a platform for employees to share their insights. This inclusive approach not only strengthens team morale but also enhances the effectiveness of lean implementation.
Tips for Overcoming Challenges
Address resistance to change with clear communication
Resistance to change is a common challenge when adopting lean. Teams may feel uncertain about new processes or fear additional workload. Leaders must address these concerns through clear and consistent communication. Explaining the benefits of lean, such as faster delivery times and improved collaboration, helps build trust and understanding.
Leaders should also provide regular updates on progress and celebrate small wins. For example, highlighting how a new workflow reduced waiting times can demonstrate the tangible benefits of lean practices. Open dialogue allows team members to voice their concerns and feel heard, which reduces resistance and fosters a positive attitude toward change.
"Lean Managers play a crucial role in making Lean strategies work by leading teams, ensuring understanding of tasks, and helping achieve goals." This insight underscores the importance of leadership in overcoming resistance and driving successful implementation.
Provide training and resources for team members
Training equips teams with the skills and knowledge needed to implement lean effectively. Workshops, online courses, and hands-on sessions can help employees understand the principles of lean methodology and how to apply them in their roles. For example, training on tools like Kanban boards or value stream mapping can enhance efficiency and collaboration.
Providing resources, such as guides or access to experts, ensures that teams feel supported throughout the transition. Leaders should also encourage continuous learning by offering opportunities for skill development. This investment in training not only improves the implementation process but also boosts employee confidence and engagement.
By addressing challenges proactively and involving the team at every step, organizations can successfully adopt lean methodology. These strategies create a strong foundation for continuous improvement and sustainable success.
Real-World Examples of Lean Methodology in Action
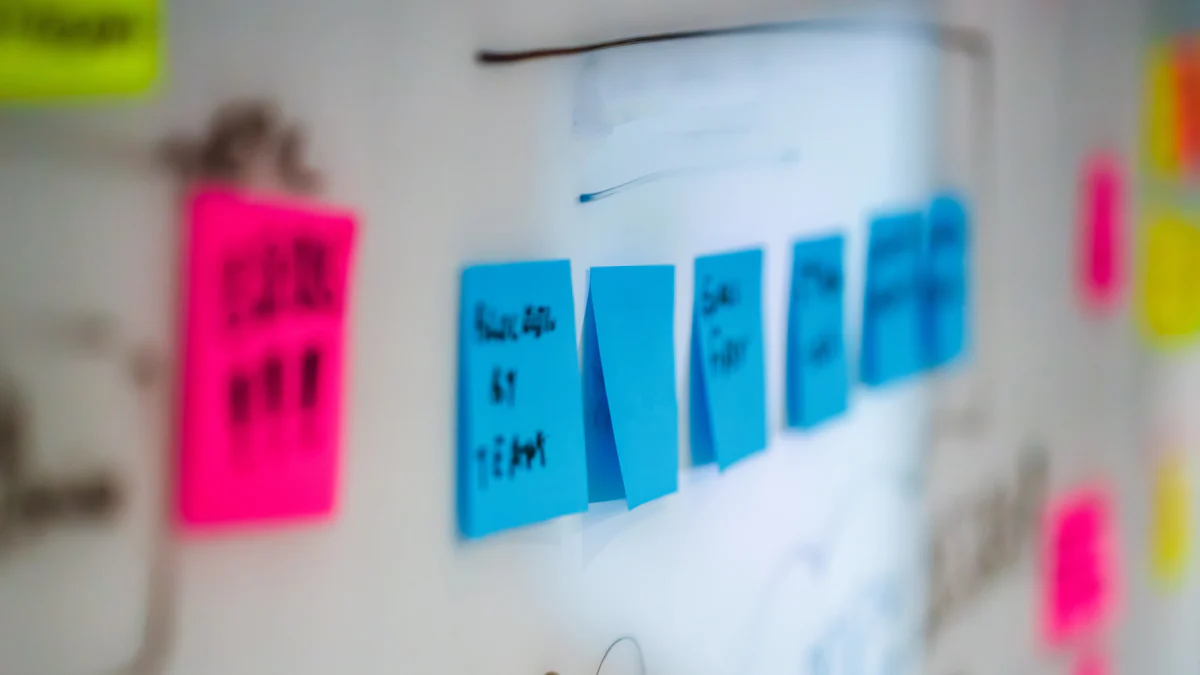
Case Study 1: Toyota’s Lean Manufacturing System
Toyota stands as a global leader in efficiency and innovation, largely due to its adoption of the Toyota Production System. This system, developed in the 1940s, laid the foundation for what is now known as lean manufacturing. Toyota's approach focused on eliminating waste, improving workflows, and delivering value to customers. By implementing practices such as just-in-time production and continuous improvement, Toyota revolutionized the automotive industry.
The results of this system have been remarkable. Toyota consistently ranks among the largest automakers in the world. Its ability to produce high-quality vehicles efficiently has set a benchmark for other industries. The principles of lean manufacturing, originating from Toyota, have since been adopted by organizations across sectors, proving their versatility and effectiveness.
"The Toyota Production System is not just a manufacturing strategy; it is a philosophy that prioritizes efficiency and respect for people." This philosophy has inspired countless businesses to rethink their processes and strive for excellence.
Case Study 2: Lean Implementation in Healthcare to Reduce Wait Times
Healthcare systems worldwide have embraced lean methodology to improve patient care and operational efficiency. By identifying and eliminating waste, hospitals and clinics have streamlined their processes, leading to better outcomes for patients. For example, many healthcare facilities have reduced wait times by optimizing workflows and reallocating resources effectively.
One notable success involved a hospital that applied lean principles to its emergency department. By analyzing patient flow and addressing bottlenecks, the team reduced average wait times by 30%. This improvement not only enhanced patient satisfaction but also allowed medical staff to focus on delivering quality care.
Lean's adaptability has made it a powerful tool in healthcare. It ensures that every step in the process adds value, whether through faster diagnoses or more efficient treatment plans. The success of lean in healthcare demonstrates its potential to transform industries beyond manufacturing.
Common Misconceptions About Lean Methodology
Myth: Lean is only for manufacturing
Many believe lean applies exclusively to manufacturing, given its origins in the Toyota Production System. However, this assumption overlooks its adaptability. Lean principles extend far beyond factory floors, offering value to industries like healthcare, software development, and education. For example, hospitals use lean to reduce patient wait times, while software teams apply it to streamline workflows and deliver faster results.
Lean’s focus on eliminating waste and enhancing efficiency makes it versatile. Teams across various sectors can tailor its principles to meet their unique goals. By emphasizing customer value and continuous improvement, lean proves effective in optimizing processes, regardless of the industry.
"Lean’s scope extends well beyond mere process improvement; it encompasses a holistic approach to business performance."
This adaptability highlights lean’s relevance in diverse environments, debunking the myth that it is limited to manufacturing.
Myth: Lean sacrifices quality for speed
Another common misconception is that lean prioritizes speed at the expense of quality. In reality, lean emphasizes delivering value to customers, which includes maintaining high-quality standards. Teams using lean focus on reducing defects, rework, and inefficiencies that compromise quality. By addressing these issues, they achieve faster delivery times without sacrificing excellence.
For instance, lean encourages continuous improvement through small, incremental changes. This approach ensures that teams refine their processes while upholding quality. Organizations adopting lean often report fewer errors and higher customer satisfaction, proving that speed and quality can coexist.
"Lean principles consider the customer value of any action or decision to ensure needs are always met or exceeded."
This focus on value creation demonstrates that lean enhances both efficiency and quality, dispelling the myth that one must come at the cost of the other.
Myth: Lean is too rigid for creative teams
Some argue that lean’s structured approach stifles creativity. This belief stems from a misunderstanding of its principles. Lean does not impose rigid rules; instead, it provides a framework for teams to identify inefficiencies and innovate solutions. Creative teams, such as those in marketing or design, can use lean to streamline their workflows and focus on producing impactful work.
Lean promotes collaboration and empowers teams to make decisions. By fostering a culture of continuous improvement, it encourages experimentation and innovation. Teams can adapt lean practices to suit their creative processes, ensuring flexibility while achieving efficiency.
"Lean is highly adaptable and can be molded to suit different organizational needs and goals."
This adaptability makes lean an asset for creative teams, proving that it supports, rather than hinders, innovation.
Tools and Resources to Support Lean Implementation
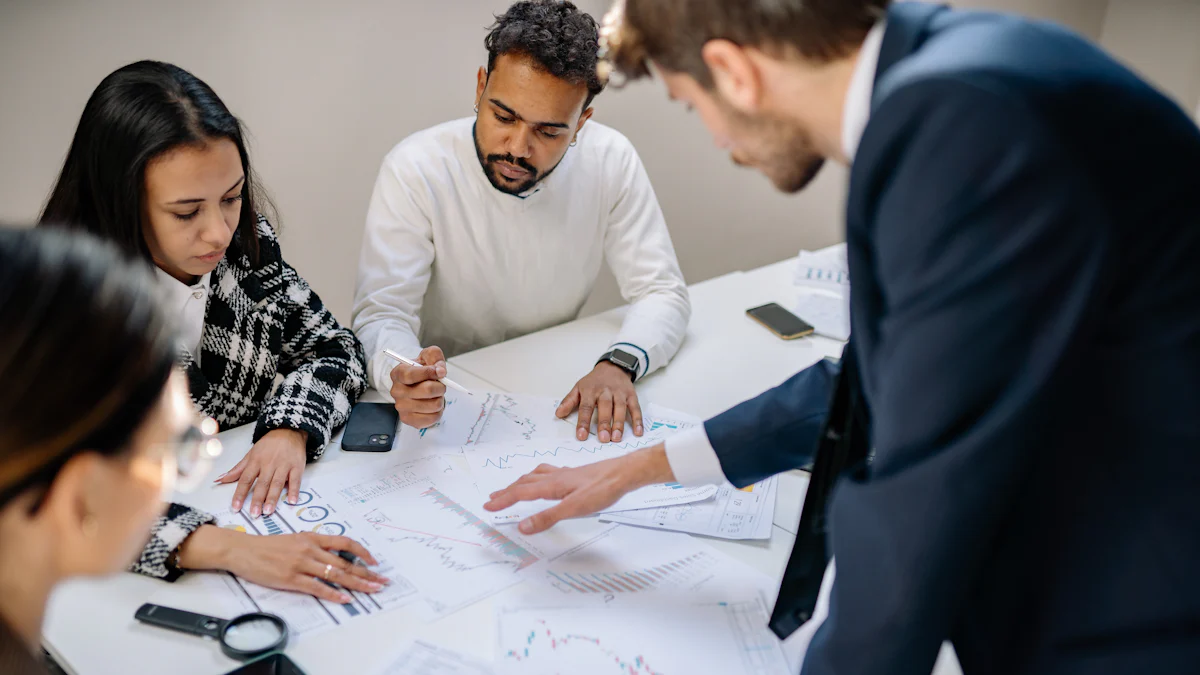
Popular Lean Tools
Kanban Boards
Kanban boards serve as a visual workflow management tool that helps teams organize tasks and track progress. By displaying work items on a board, teams can easily identify bottlenecks and inefficiencies in their processes. This tool enhances communication and coordination across departments, ensuring that everyone stays aligned with project goals.
Kanban boards come in various forms, such as physical boards with colored cards or digital platforms with interactive features. Teams practicing lean often rely on Kanban to visualize their workflows and actively manage tasks. For example, a software development team can use Kanban to monitor coding, testing, and deployment stages, ensuring smooth transitions between each phase. This method not only improves efficiency but also fosters accountability within the team.
"Kanban simplifies workflow management by making tasks visible and actionable, enabling teams to address issues promptly and maintain momentum."
Value Stream Mapping
Value stream mapping provides a comprehensive view of the steps involved in delivering a product or service to customers. This tool allows teams to analyze the flow of materials, information, and activities within their processes. By creating a value stream map, teams can identify non-value-adding steps and eliminate waste effectively.
This tool proves invaluable for organizations aiming to optimize their operations. For instance, a manufacturing team can use value stream mapping to reduce lead times and improve product quality. Similarly, in lean software development, teams can map out their processes to streamline coding and testing workflows. Visualizing the entire value stream helps teams focus on activities that directly contribute to customer satisfaction.
"Value stream mapping enables teams to pinpoint inefficiencies and innovate solutions, ensuring that every step adds value to the customer."
Recommended Books and Training Programs
"The Lean Startup" by Eric Ries
Eric Ries' The Lean Startup offers practical insights into applying lean principles to startups and innovation-driven projects. The book emphasizes the importance of building a minimum viable product (MVP) and iterating based on customer feedback. This approach aligns with lean methodology's focus on continuous improvement and delivering value efficiently.
Readers will find actionable strategies for reducing waste and optimizing workflows in dynamic environments. The book serves as a valuable resource for entrepreneurs and teams seeking to implement lean practices in their operations.
"The Lean Startup provides a roadmap for teams to innovate effectively while minimizing risks and maximizing customer value."
"Lean Thinking" by James P. Womack and Daniel T. Jones
James P. Womack and Daniel T. Jones' Lean Thinking delves into the core principles of lean methodology. The authors outline five key steps: specifying value, mapping the value stream, creating flow, establishing pull, and pursuing perfection. These concepts guide teams in eliminating waste and enhancing efficiency.
The book includes real-world examples from various industries, demonstrating the versatility of lean principles. Teams can use this resource to gain a deeper understanding of lean and apply its practices to achieve sustainable success.
"Lean Thinking equips teams with the knowledge to transform their processes and deliver exceptional results."
The Role of Lean Management in Sustaining Efficiency
Lean Management Practices
Respect for people as a core tenet
Lean management emphasizes respect for people as a foundational principle. This approach recognizes that employees are not just resources but critical contributors to the success of any organization. By fostering an environment where individuals feel valued, lean management encourages active participation in continuous improvement initiatives. Teams become more engaged when their ideas and efforts are acknowledged, leading to higher morale and productivity.
Respect for people also involves empowering employees to take ownership of their work. Lean systems encourage team members to identify inefficiencies and propose solutions. This empowerment not only enhances efficiency but also builds trust and collaboration within the organization. As one expert noted, lean creates a culture where everyone, from leadership to frontline workers, plays a role in driving improvement.
"Lean is a culture of continuous improvement that involves everyone in the organization, from top management to frontline workers."
By prioritizing respect for people, lean management ensures that employees remain motivated and committed to achieving organizational goals.
Leadership’s role in fostering a Lean culture
Leadership plays a pivotal role in embedding lean principles into an organization’s culture. Leaders must set the tone by demonstrating a commitment to continuous improvement and efficiency. They guide teams in identifying waste, streamlining processes, and focusing on activities that deliver value to the customer. Effective leaders also provide the necessary resources and training to support lean initiatives.
Transparent communication is another critical aspect of leadership in lean management. Leaders must clearly articulate the benefits of lean practices and involve teams in decision-making processes. This approach reduces resistance to change and fosters a sense of shared responsibility. As one expert highlighted, lean management requires constant monitoring and adjustment, making leadership essential for sustaining long-term success.
"Lean is not a quick fix, but a long-term commitment that requires constant monitoring, evaluation, and adjustment."
Strong leadership ensures that lean principles become ingrained in the organization, creating a sustainable culture of efficiency and innovation.
Long-Term Benefits of Lean Management
Sustainable efficiency and adaptability
Lean management drives sustainable efficiency by eliminating waste and optimizing workflows. Organizations that adopt lean principles consistently review their processes to ensure every step adds value. This ongoing evaluation helps teams adapt to changing market demands and maintain high performance over time. For example, lean practices in manufacturing have reduced resource consumption while improving product quality, demonstrating their long-term impact.
The adaptability of lean systems allows organizations to navigate challenges effectively. By focusing on continuous improvement, teams can respond quickly to disruptions and implement solutions that enhance efficiency. This resilience positions businesses to thrive in competitive environments and achieve lasting success.
"Lean methodologies can lead to a more engaged workforce, higher quality products and services, and a stronger, more resilient business model."
Sustainable efficiency and adaptability make lean management a valuable strategy for organizations seeking to remain competitive and innovative.
Enhanced employee satisfaction and retention
Lean management contributes to higher employee satisfaction by creating a supportive and empowering work environment. Teams feel more engaged when they have the autonomy to make decisions and contribute to process improvements. This sense of ownership fosters pride in their work and strengthens their connection to the organization.
Additionally, lean practices promote collaboration and transparency, which enhance workplace relationships. Employees who feel respected and valued are more likely to remain loyal to their organization. As one expert observed, lean improves employee morale by involving them in continuous improvement activities and recognizing their contributions.
"Lean manufacturing can improve employee morale and engagement by empowering them to participate in continuous improvement activities and take ownership of their work."
By prioritizing employee satisfaction, lean management not only boosts retention but also creates a motivated workforce that drives organizational success.
Lean methodology transforms team operations by focusing on the elimination of waste, fostering continuous improvement, and empowering individuals. Its principles enable teams to achieve faster delivery times, enhance collaboration, and produce higher-quality outcomes. By prioritizing value creation and streamlining processes, lean ensures that every action contributes to customer satisfaction. Teams can begin by identifying inefficiencies and involving members in setting goals. This approach not only drives efficiency but also builds a culture of innovation and adaptability. Embracing lean practices unlocks a team’s full potential, paving the way for sustainable success.
FAQ
What is the main focus of Lean methodology?
Lean methodology focuses on eliminating waste and improving efficiency to maximize customer value. It emphasizes refining processes to ensure every step adds value. If a process does not contribute to customer satisfaction, it is considered wasteful and should be reduced or eliminated. This approach helps teams deliver consistent results while fostering continuous improvement.
Why is it important to debunk common misconceptions about Lean?
Misconceptions about Lean can prevent organizations from fully embracing its potential. For instance, many believe Lean is only for manufacturing or that it sacrifices quality for speed. By addressing these myths, businesses can adopt Lean with a clearer understanding. This enables them to drive continuous improvement, enhance customer value, and thrive in competitive environments.
"Lean is not confined to manufacturing; it applies to various industries, including healthcare, software development, and education."
How does Lean methodology differ from other process improvement approaches?
Lean stands out by prioritizing customer value and waste elimination. Unlike other methods, it focuses on small, incremental changes rather than large-scale overhauls. This approach fosters adaptability and ensures teams continuously refine their processes. Lean also emphasizes respect for people, empowering teams to take ownership of their work and contribute to improvements.
What are some common types of waste identified in Lean?
Lean identifies several types of waste that hinder efficiency, including:
Overproduction: Producing more than needed.
Waiting: Delays between process steps.
Defects: Errors requiring rework.
Excess Motion: Unnecessary movement of people or materials.
Overprocessing: Performing tasks beyond what is required.
By addressing these wastes, teams can streamline workflows and improve productivity.
Can Lean methodology be applied outside of manufacturing?
Absolutely. While Lean originated in manufacturing, its principles apply to various industries. For example, healthcare organizations use Lean to reduce patient wait times, and software teams implement it to streamline development processes. Lean’s adaptability makes it a valuable tool for any sector aiming to enhance efficiency and deliver value.
What tools support Lean implementation?
Several tools help teams implement Lean effectively:
Kanban Boards: Visualize workflows and track progress.
Value Stream Mapping: Analyze processes to identify inefficiencies.
These tools provide clarity and enable teams to focus on activities that add value. For example, Kanban boards help software teams monitor coding and testing stages, ensuring smooth transitions.
Where can one find resources to learn more about Lean principles?
The Lean Enterprise Institute offers comprehensive guides on Lean Management principles. Books like The Lean Startup by Eric Ries and Lean Thinking by James P. Womack and Daniel T. Jones also provide valuable insights. These resources help teams understand Lean concepts and apply them effectively.
"Lean Thinking equips teams with the knowledge to transform their processes and deliver exceptional results."
How does Lean empower teams?
Lean empowers teams by granting them autonomy in decision-making. This approach encourages employees to address challenges directly and propose solutions. It fosters collaboration, accelerates problem-solving, and builds a sense of ownership. Empowered teams often feel more engaged and motivated, leading to higher productivity and innovation.
What are the benefits of continuous improvement in Lean?
Continuous improvement, or Kaizen, ensures teams regularly evaluate and refine their processes. Small, incremental changes lead to significant efficiency gains over time. For example, addressing minor bottlenecks can reduce delivery times and improve quality. This iterative approach fosters adaptability and positions teams for long-term success.
How can organizations overcome resistance to Lean implementation?
Resistance to change often arises during Lean adoption. Clear communication about its benefits, such as faster delivery and improved collaboration, can ease concerns. Providing training and involving teams in goal-setting also fosters acceptance. Leaders play a crucial role by guiding teams and celebrating small wins to build trust and momentum.
"Lean is a long-term commitment that requires leadership, transparency, and continuous effort to succeed."